Шпоночные соединения образуются шпонкой — металлическим стержнем, находящимся одновременно в пазах вала и устанавливаемой на него детали (ступицы). Шпонки служат для передачи крутящего момента от вала к ступице или, наоборот, от ступицы к валу. Кроме того, шпонки обеспечивают фиксацию ступицы на валу в осевом положении. По условиям эксплуатации шпоночные соединения подразделяются на напряженные и ненапряженные. Напряженными называют соединения, в которых при отсутствии внешних сил и моментов постоянно действуют внутренние силы упругости, возникающие в результате предварительного затягивания.
В зависимости от конструкции различают шпоночные соединения с призматическими, сегментными, направляющими, скользящими и клиновыми шпонками, каждое из которых имеет свои достоинства и недостатки.
Призматические шпонки имеют прямоугольное сечение, противоположные грани у них параллельны. Работают эти шпонки боковыми сторонами. Призматические шпонки изготавливаются в двух исполнениях: с закругленными и плоскими торцами. Соединение шпонки с валом неподвижное напряженное. В паз ступицы шпонка входит с зазором.
Сегментные шпонки подобно призматическим работают боковыми гранями. При необходимости по длине вала могут устанавливаться две, а иногда и три шпонки. К достоинствам сегментных шпонок относится простота изготовления как самих шпонок, так и пазов под них, к недостаткам — необходимость изготовления глубоких пазов в валах, что снижает прочность последних. В связи с этим сегментные шпонки применяют только для передачи сравнительно небольших моментов.
Направляющие шпонки применяют в тех случаях, когда ступица должна иметь возможность перемещаться вдоль вала. Такие шпонки крепят к валу при помощи винтов. Для крепления шпонки к валу в ней выполняют два отверстия, имеющих углубления под головки винтов. Еще одно отверстие выполняется в шпонке для подвода смазки. Соединение шпонки с пазом вала неподвижное плотное, а с пазом ступицы — свободное с зазором,
Скользящие шпонки применяют вместо направляющих в тех случаях, когда требуется значительное перемещение ступицы вдоль вала. Шпонка имеет цапфу, которая входит в отверстие, выполненное в ступице, перемещаемой вдоль вала. При изменении положения ступицы на валу шпонка перемещается вместе со ступицей по пазу вала.
Клиновые шпонки в совокупности с валом и ступицей образуют напряженное соединение. Они представляют собой клин прямоугольного сечения с уклоном 1:100, Работают такие шпонки широкими гранями и обеспечивают неподвижное крепление детали на валу. Клиновые шпонки плохо центрируются, поэтому применяются только для неответственных тихоходных передач.
При сборке шпоночного соединения большое значением имеет строгое соблюдение посадок в соединении шпонки с валом и ступицей. Одной из основных причин неправильного распределения нагрузки и смятия шпонки является увеличение зазора в соединении. К смятию может также привести неправильное расположение паза на валу нередко наблюдается и перекос осей пазов относительно оси вала, что значительно затрудняет сборку шпоночного соединения и вызывает перекос охватывающей детали на валу.
Входной контроль шпоночных пазов.
Прежде чем приступить к сборке шпоночных соединений, особенно ответственных, необходимо произвести контроль размеров шпоночного паза на валу и его расположения относительно оси вала.
Контроль глубины паза (рис. 1, а) осуществляется при помощи шаблона и щупа.
Проверку положения боковых сторон шпоночного паза относительно его оси осуществляют при помощи клиновых плиток (рис. 1, б), которые укладывают в паз, а затем щупом контролируют зазоры в точках I и II. При отсутствии перекоса боковых стенок паза зазор должен быть одинаковым.
Отклонение от параллельности стенок шпоночного паза относительно оси вала может быть определен индикаторным прибором (рис. 1, в). При отсутствии отклонения от параллельности показания индикатора на одном и другом конце паза должны быть одинаковы.
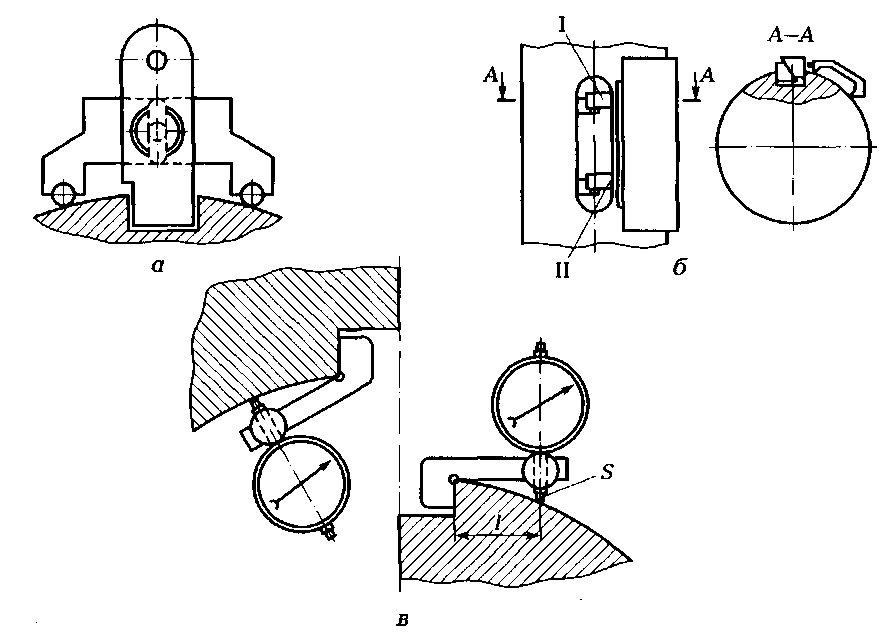
а — глубины шпоночного паза; б — положения стенок паза относительно его оси; в — перекоса паза относительно его оси; I, II — точки установки измерительных призм; S — измерительная ножка индикатора; l — расстояние от боковой поверхности шпоночного паза до точки контакта измерительной ножки индикатора с поверхностью вала
Сборка шпоночного соединения.
Сборку шпоночного соединения начинают с пригонки шпонки по пазу вала, предварительно притупив острые кромки пазов и шпонок. После пригонки шпонку устанавливают в пазу вала, обеспечивая указанную на чертеже посадку. Поскольку, в большинстве случаев, шпонка устанавливается в пазу вала по посадке с натягом, то для ее установки следует использовать медный молоток, струбцину или пресс.
При установке направляющих шпонок следует, используя отверстия под винты, выполненные в шпонке, в качестве кондуктора просверлить отверстия в пазу вала и нарезать в них резьбу для крепежных винтов и после этого закрепить шпонку в пазу вала.
После установки шпонки в паз вала необходимо проверить высоту выступающей части при помощи микрометрической головки и мостика (рис. 2, а). В тех случаях когда на валу устанавливают несколько шпонок, их взаимное положение проверяют так, как это показано на рис. 2, б). На шпонки устанавливают приспособление с раздвижными ножками 2, снабженными цилиндрическими валиками 3, и фиксируют положение ножек винтом 4. По показаниям индикатора часового типа 1 при перемещении приспособления вдоль оси вала по поверхностям шпонок определяют взаимное положение последних (при перемещении приспособления показания индикатора не должны изменяться, т.е, стрелка отсчетного устройства должна оставаться неподвижной).
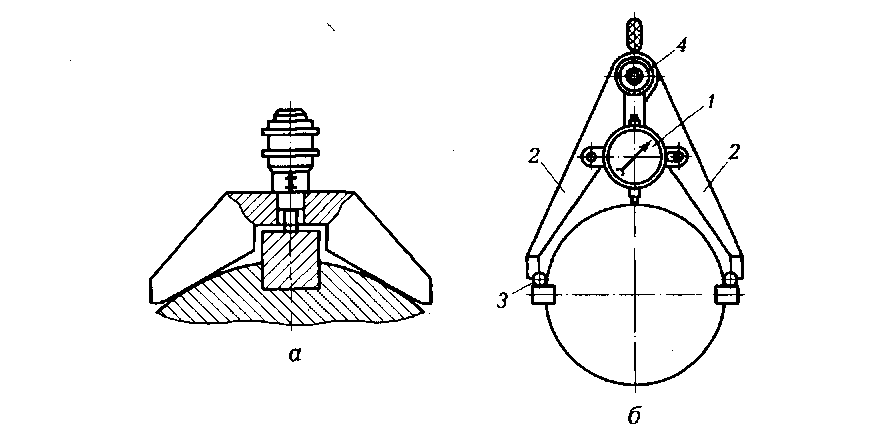
а — высоты выступающей части; б — взаимного расположения шпонок на валу: 1 — индикатор: 2 — раздвижные ножки; 3 — цилиндрический валик; 4 — винт
Таблица 1. Типичные дефекты при выполнении пригоночных работ
Дефект | Причина | Способ предупреждения или исправления |
Ступица устанавливается на вал слишком туго | Мала ширина паза ступицы или его глубина | Пригнать более точно паз по шпонке |
Для установки шпонки в паз вала требуется слишком большое усилие | Плохо пригнана шпонка | Повторить пригонку шпонки по пазу вала |
Шпонка не удерживается на валу | Снят слишком большой слой материала с поверхности шпонки | Заменить шпонку и вновь пригнать ее по пазу вала |
Сборка соединений со скользящими шпонками начинается с пригонки шпонки по пазу ступицы и ее установки в этом пазу, после чего осуществляется пригонка паза вала по шпонке. После сборки при перемещении ступицы не должно наблюдаться ее качания относительно вала.
В процессе выполнения пригоночных работ при сборке шпоночных соединений могут появиться различные дефекты, причины появления которых и способы предупреждения приведены в табл. 1.