Ручная дуговая сварка — дуговая сварка, при которой возбуждение дуги, подача электрода и его перемещение производятся вручную. В процессе сварки электрод перемещают по направлению к изделию по мере плавления электрода, вдоль соединяемых кромок и поперек соединения (поперечные колебания) для получения необходимых формы и сечения шва.
Это наиболее универсальный способ, который позволяет без замены сварочного инструмента и оборудования (при правильно выбранном сварочном режиме) выполнять швы различных типов в любом пространственном положении в цеховых и монтажных условиях. Покрытыми электродами сваривают черные и цветные металлы и различные сплавы и выполняют наплавку слоев с особыми свойствами. Для возбуждения и стабильного горения дуги используют специальные источники постоянного или переменного тока с крутопадающей внешней вольт-амперной характеристикой.
Сущность процесса ручной дуговой сварки.
Возбуждение (зажигание) дуги происходит при кратковременном замыкании электрической сварочной цепи между изделием и концом электрода и быстром отводе электрода на расстояние 2…4 мм, в результате чего в парогазовом промежутке возникает дуговой разряд (рис. 1). Теплота, выделяющаяся в дуговом разряде, обеспечивает плавление стержня и покрытия электрода и металла соединяемых деталей.
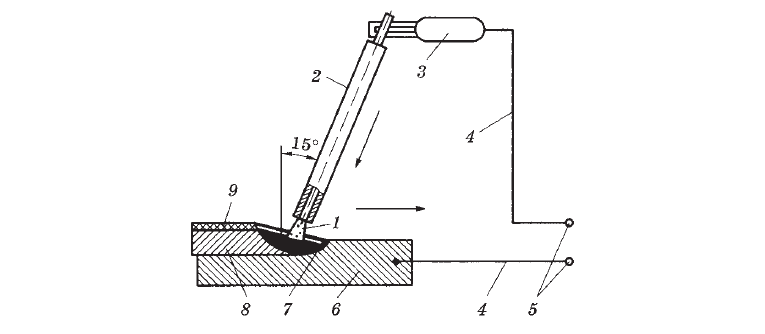
1 — сварочная дуга; 2 — электрод; 3 — электрододержатель; 4 — сварочные провода; 5 — источник питания; 6 — свариваемая деталь; 7 — сварочная ванна; 8 — сварной шов; 9 — шлаковая корка; стрелки показывают направление движения электрода в процессе сварки.
При плавлении стержня капли жидкого электродного металла проходят через дуговой промежуток. Перенос электродного металла происходит в большинстве случаев без коротких замыканий. Размер капель и частота переноса определяются параметрами режима. С ростом сварочного тока диаметр капель уменьшается, а частота переноса увеличивается. С повышением напряжения на дуге диаметр капель увеличивается. При этом снижается частота переноса и растет время пребывания капель на торце электрода, где возможно их взаимодействие с атмосферой, что обусловливает повышенное выгорание легирующих элементов.
Расплавляющееся покрытие образует шлак и газы. Шлак обволакивает капли электродного металла, но не полностью предохраняет металл от взаимодействия с атмосферой, поэтому необходима и газовая защита. С этой целью в электродные покрытия вводят газообразующие компоненты. Основной и электродный металлы расплавляются, образуя сварочную ванну. Размеры сварочной ванны зависят от режима сварки и обычно не превышают следующих значений: по глубине проплавления — 7 мм, по ширине — 15 мм и по длине — 30 мм. Шлак с каплями электродного металла попадает в сварочную ванну и всплывает на ее поверхность. По мере удаления дуги расплавленный металл сварочной ванны охлаждается и затвердевает, образуя сварной шов. Жидкий шлак, покрывающий ванну, также затвердевает и на поверхности шва появляется твердая шлаковая корка, удаляемая после сварки.
Таким образом, покрытие электрода обеспечивает газошлаковую защиту металла сварного соединения от взаимодействия с воздухом и металлургическую обработку металла в ванне. Основными преимуществами способа являются универсальность и простота оборудования. Недостаток — невысокая производительность и применение ручного труда. Невысокая производительность обусловлена малыми допустимыми значениями плотности тока, а также тем, что металл шва формируется в основном за счет электродного металла.
Ограничение плотности тока вызвано низкой допустимой температурой нагрева электрода проходящим сварочным током, которая для покрытий с большим содержанием органических веществ не превышает 200°С, а для покрытий основного типа — не более 700°С. При большой силе тока наблюдается перегрев электрода. В результате ухудшаются защитные свойства покрытия, наблюдается его осыпание со стержня, нарушается стабильность плавления электрода.
Формирование шва в основном за счет электродного металла объясняется невысокой глубиной проплавления при сварке. Доля участия основного металла в формировании шва обычно не более 35%. В этих условиях определяющим в производительности процесса становится коэффициент наплавки, значение которого зависит от физико-химических свойств покрытия, рода тока и его полярности, состава электрода, режима сварки и изменяется обычно в пределах 8…12 г/А⸳ч.
При расчете количества электродов, расходуемых на сварку данного шва, исходят из коэффициента расплавления электрода, который больше коэффициента наплавки на количество электродного металла, теряемого на разбрызгивание и испарение и определяемого коэффициентом потерь. Величина коэффициента потерь изменяется в пределах от 5 до 15% в зависимости от плотности тока в электроде, состава покрытия и режима сварки. Если учесть, что при сварке покрытыми электродами до 15% длины стержня электрода теряется в виде неиспользуемых отходов (огарков), то общие потери электродного металла на угар, разбрызгивание и огарки могут быть до 30%.
Основные параметры режимов при ручной дуговой сварке.
Под режимом сварки понимают совокупность контролируемых параметров, при которой обеспечивается устойчивое горение дуги и получение швов заданных размеров, формы и свойств. Параметры режима подразделяют на основные и дополнительные. К основным параметрам относят диаметр электрода, силу сварочного тока, род и полярность его, напряжение дуги. К дополнительным параметрам — наклон и поперечные колебания электрода, положение шва в пространстве, число проходов.
Диаметр электродов выбирают в зависимости от толщины металла, катета шва, положения шва в пространстве. Примерное соотношение между толщиной металла S и диаметром электрода d при сварке шва в нижнем положении следующее:
S, мм | 1…2 | 3…5 | 4…10 | 12…24 | 30…60 |
d, мм | 2…3 | 3…4 | 4…5 | 5…6 | 6 и более |
Выполнение вертикальных, горизонтальных и потолочных швов независимо от толщины свариваемого металла производится электродами небольшого диаметра (до 4 мм), так как при этом меньше стекание жидкого металла и шлака из сварочной ванны. При сварке многослойных швов для лучшего провара корня шва первый шов сваривают электродом диаметром 3…4 мм, а последующие — электродами большего диаметра.
Сила сварочного тока обычно устанавливается в зависимости от выбранного диаметра электрода. При сварке швов в нижнем положении величину тока подсчитывают, пользуясь эмпирическими формулами:
Iсв = Kd или Iсв = (20 + 6d)d,
где d — диаметр электрода, мм; K — коэффициент, зависящий от диаметра электрода и имеющий следующие значения:
d, мм | 2 | 3 | 4 | 5 | 6 |
К | 25…30 | 30…45 | 35…50 | 40…45 | 45…60 |
При сварке на вертикальной плоскости силу тока уменьшают на 10…15%, а в потолочном положении — на 15…20% против значения, выбранного для нижнего положения.
Род тока и полярность устанавливают в зависимости от вида электродного покрытия, состава свариваемого металла и его толщины. При сварке постоянным током обратной полярности на электроде выделяется больше теплоты. Поэтому обратная полярность применяется при сварке тонких деталей с целью предотвращения прожога, при сварке легированных сталей во избежание их перегрева и при сварке электродами с основным покрытием, когда требуется повышенное выделение теплоты на электроде для плавления тугоплавких компонентов покрытия. Переменный ток можно использовать при сварке углеродистых сталей электродами с кислыми, рутиловыми и целлюлозными покрытиями.
Напряжение дуги при ручной дуговой сварке устанавливается в пределах 20…36 В и регламентируется производителем электродов. Число проходов определяют, учитывая, что площадь поперечного сечения металла, наплавляемого за один проход, при которой обеспечиваются оптимальные условия формирования, должна составлять: для первого прохода (при сварке корня шва F1 = (6…8) d) ; для последующих проходов Fn = (6…8) d, но не более 40 мм2.
Технология сварки различных типов соединений и швов ручной дуговой сваркой.
Подготовка и сборка сварных соединений перед ручной дуговой сваркой.
Основные типы, конструктивные элементы и размеры сварных соединений из сталей, а также сплавов на железоникелевой и никелевой основах, выполняемых ручной дуговой сваркой, установлены ГОСТ 5264-80. В нем предусмотрено четыре типа соединений в зависимости от толщины свариваемых деталей.
По форме подготовленных кромок соединения бывают с отбортовкой кромок, без скоса кромок и со скосом кромок — одной или двух. Выполнять швы можно как с одной стороны соединений (односторонние), так и с двух сторон (двусторонние).
При расположении свариваемых деталей под углом основные типы, конструктивные элементы и размеры швов сварных соединений установлены ГОСТ 11534-75, которым предусмотрены формы подготовки кромок и размеры выполнения швов угловых и тавровых соединений.
От состояния поверхности свариваемых кромок в значительной мере зависит качество сварных швов. Подготовка кромок под сварку состоит в тщательной очистке их от ржавчины, окалины, грязи, масла и других инородных покрытий. Кромки очищают стальными вращающимися щетками, гидропескоструйным и дробеметным способами, шлифовальными кругами, пламенем сварочной горелки, травлением в растворах кислот и щелочей.
Подготовленные детали собирают под сварку. При сборке важно выдержать необходимые зазоры и совмещение кромок. Точность сборки проверяют шаблонами, измерительными линейками и различного рода щупами. Сборку выполняют в специальных приспособлениях или на выверенных стеллажах. Временное закрепление деталей производят струбцинами, скобами или прихваткой короткими швами. Количество прихваток и их размер определяются технологической документацией.
Общие технические приемы при ручной дуговой сварке.
Технология ручной дуговой сварки предусматривает выполнение следующих операций: возбуждение дуги, перемещение электрода в процессе сварки, выполнение швов в определенном порядке в зависимости от особенностей сварных соединений и заварка кратера.
Для образования заданных размеров сварного шва и требуемой формы проплавления электроду придается сложное движение в трех направлениях.
Первое движение — это движение электрода в направлении оси со скоростью его плавления для поддержания определенной длины дуги, которая зависит от марки и диаметра электрода и ориентировочно должна быть в пределах
Lд = (0,5…1,1) d,
где Lд — длина дуги, мм; d — диаметр электрода, мм.
Длинная дуга способствует более интенсивному окислению и азотированию расплавляемого металла, что приводит к пористости металла шва, и увеличивает разбрызгивание.
Второе движение электрода направлено вдоль оси шва и производится со скоростью сварки.
В результате этих двух движений образуется узкий шов шириной не более 1,5 диаметра электрода. Такими швами сваривают тонкий металл, а также корень шва при многослойной (многопроходной) сварке.
Третье движение — это колебание конца электрода поперек оси шва, которое необходимо для образования валика определенной ширины, хорошего провара кромок и замедления остывания сварочной ванны. Колебательные движения электрода поперек оси шва (рис. 2) могут быть различными — в зависимости от формы, размеров и положения шва в пространстве. При сварке с поперечными колебаниями ширина валика может составлять (2…4)d, а форма проплавления зависит от траектории движения и изменяется в поперечном сечении шва в соответствии с количеством теплоты, вводимой в основной металл, обратно пропорциональным скорости перемещения конца электрода.
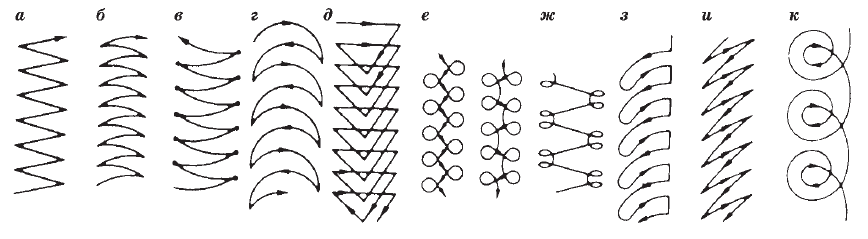
а, б — при обычной сварке; в—ж — с усиленным прогревом кромок; з, и — с усиленным прогревом одной кромки; к — с прогревом корня шва.
Заканчивают сварку заваркой кратера, который образуется в шве при обрыве дуги и является местом скопления неметаллических включений и зарождения трещин. Для этого электрод держат неподвижно до естественного обрыва дуги или укорачивают дугу вплоть до частых коротких замыканий, после чего ее резко обрывают. При перерывах в процессе сварки, например при смене электрода, следует переплавить застывший металл кратера и только после этого продолжить процесс.
Техника выполнения стыковых и угловых швов при ручной дуговой сварке.
Стыковые соединения без скоса кромок, со скосом одной или двух кромок сваривают однослойными или многослойными (многопроходными) швами с одной стороны или с двух сторон стыка. Сварку выполняют на весу, на остающейся стальной подкладке или с предварительной подваркой корня шва (рис. 3). Первый слой и подварку корня шва выполняют электродом диаметром 3…4 мм.
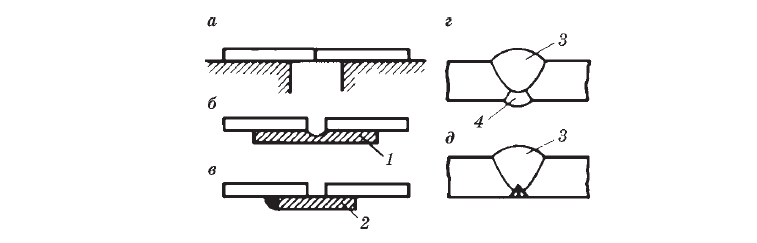
а — на весу; б — на медной съемной подкладке; в — на остающейся стальной подкладке; г — с предварительным подварочным швом; д — удаление непровара в корне шва для последующей подварки; 1, 2 — медная и стальная подкладки; 3, 4 — основной и подварочный швы.
В ответственных конструкциях при односторонней сварке на весу корень шва удаляют механической обработкой или газовой поверхностной строжкой, а затем накладывают подварочный шов.
Угловые швы применяют при сварке угловых, тавровых и нахлесточных соединений. Сварка угловых швов в нижнем положении может производиться вертикальным электродом «в лодочку» или наклонным электродом (рис. 4).
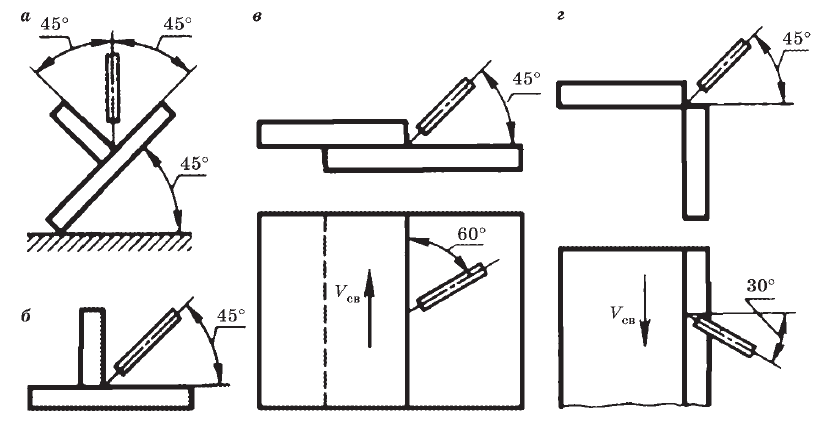
а — «в лодочку»; б-г — наклонным электродом в угол.
Сварка угловых швов «в лодочку» обеспечивает требуемое формирование шва и хороший провар корня и стенок без опасности образования подрезов, а также имеется возможность выполнять за один проход швы большого сечения. Однако при катете более 12 мм рекомендуют применять многослойные швы и собирать детали с минимальным зазором для предупреждения вытекания металла сварочной ванны.
При сварке угловых швов наклонным электродом, возможно образование подрезов на вертикальной полке, а также неполное проплавление корня шва или кромки горизонтальной детали, поэтому при катете более 8 мм сварку ведут многопроходным швом (рис. 5). Для лучшего провара корня шва первый слой выполняют узким швом электродом диаметром 3…4 мм без колебательных движений.
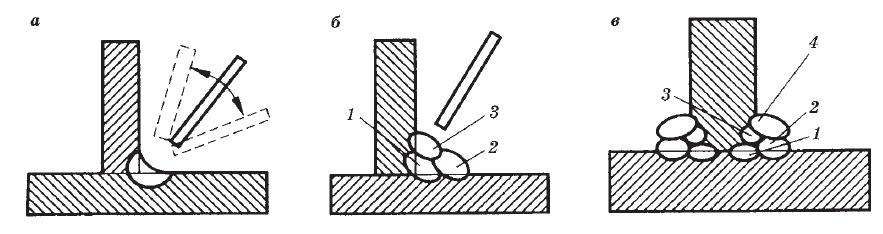
1-4 — последовательность выполнения проходов.
Техника сварки металла различной толщины при ручной дуговой сварке.
При сварке листов толщиной 0,5…3 мм возможно сквозное проплавление металла (прожог), поэтому применяют малые токи, отбортовку кромок, теплоотводящие или остающиеся подкладки.
Сварку с отбортовкой кромок выполняют на постоянном токе, часто на спуск в полувертикальном положении (45…65°).
При использовании временных теплоотводящих подкладок (массивных медных и бронзовых плит или брусков) сборку осуществляют без зазора, обеспечивая плотное прилегание свариваемых листов к подкладке.
Остающиеся подкладки применяют при сварке встык. Сварку ведут с проплавлением элементов из тонколистового металла и приваркой их к подкладке.
С увеличением толщины металла в сварных соединениях возрастают объемные сварочные напряжения, которые создают опасность возникновения и развития в швах трещин, поэтому сварку толстолистовых конструкций ведут различными способами (рис. 6).

а — двойным слоем; б — блоками; в — каскадом; I-III — участки; 1—8 — последовательность сварки слоев.
Металл толщиной 15…20 мм сваривают способом двойного слоя. На участке I (рис. 6, а) длиной 250…300 мм, наплавляют первый слой шва, счищают с него шлак и по горячему металлу первого слоя (не ниже 150…200 °С) накладывают второй слой.
Металл толщиной 20…25 мм и более сваривают блоками или каскадом. Сварку блоками (рис. 6, б) выполняют отдельными участками, а промежутки между ними заполняют до того, как будет завершена сварка всего шва. При сварке каскадом (рис. 6, в) каждый последующий участок многослойного шва перекрывает весь предыдущий участок или его часть. При V-образной подготовке кромок длина участка — 300…400 мм, а при Х-образной подготовке — 500…800 мм.
Металл толщиной 30 мм и более часто сваривают одновременно два сварщика, находящихся с противоположных сторон соединения.
Сварка швов различной протяженности при ручной дуговой сварке.
В зависимости от длины швы разделяют на короткие (300…350 мм), средние (350…1000 мм) и длинные (свыше 1000 мм).
Короткие швы сваривают от одного конца шва к другому (напроход); швы средней длины — от середины соединения к концам; длинные швы — обратноступенчатым способом, при котором сварной шов выполняется следующими один за другим участками в направлении, обратном приращению шва (рис. 7). Длина ступени (участка) —100…350 мм, причем ступени более длинные при сварке толстого металла. При выполнении многослойных швов также используется обратноступенчатый способ, при этом смежные участки вышележащих слоев сваривают в направлении, обратном сварке нижележащих швов. Концы швов смежных участков должны быть смещены на 25…30 мм.
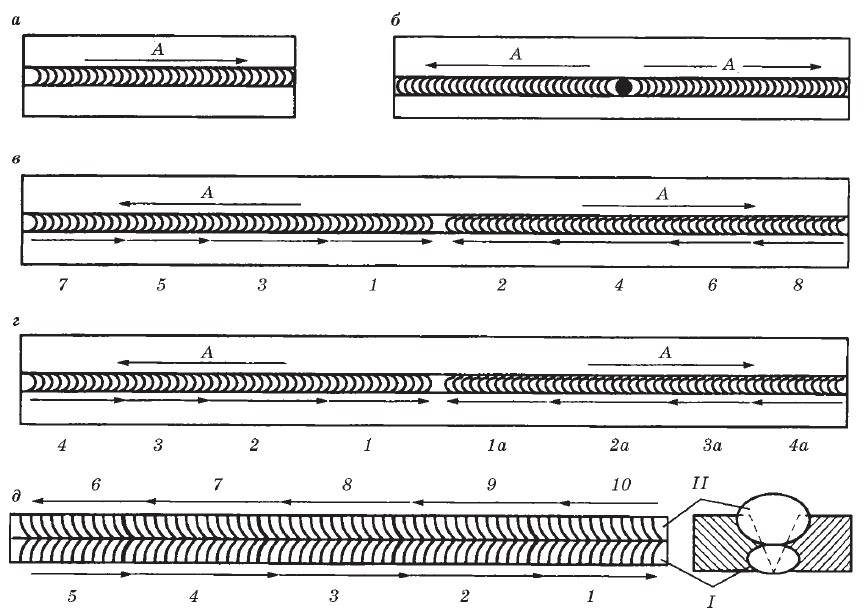
а — сварка «на проход»; б — от середины к краям; в—д — сварка длинных швов обратноступенчатым способом; 1—10 — порядок и направление сварки участков шва; А — общее направление сварки; I, II — слои шва.
Особенности сварки в различных пространственных положениях при ручной дуговой сварке.
В зависимости от положения в пространстве существенно изменяются условия формирования шва, поэтому для получения заданной формы шва необходимо назначать соответствующие режим и технику сварки (табл. 1).
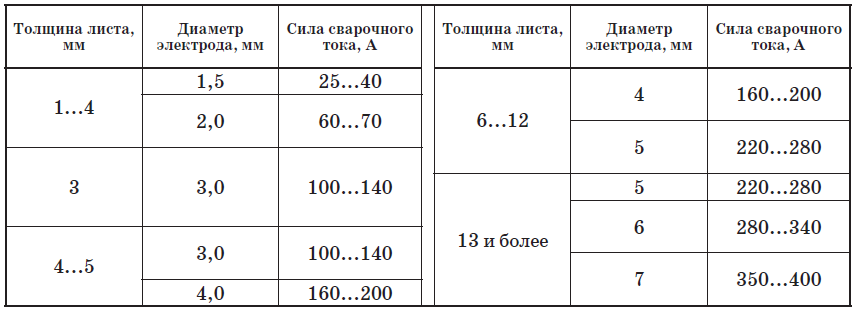
Нижнее положение является наиболее удобным для сварки, так как капли электродного металла легко переходят в сварочную ванну под действием собственного веса, и жидкий металл не вытекает из нее. Кроме того, наблюдение за сваркой в нижнем положении более удобно. В процессе сварки электрод наклоняют по направлению сварки на угол 10-20° (рис. 8, а — б).
В вертикальном положении расплавленный металл сварочной ванны стремится стечь вниз, поэтому вертикальные швы выполняют короткой дугой при переносе электродного металла с короткими замыканиями дугового промежутка. Вертикальные швы выполняют как снизу вверх, так и сверху вниз (рис. 8, в).
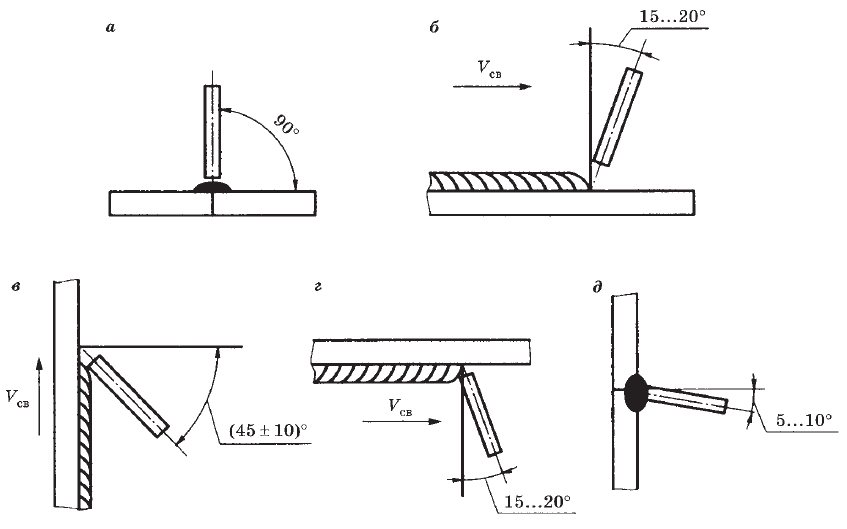
а, б — в нижнем; в — вертикальном (снизу вверх); г — потолочном; д — горизонтальном положениях.
В первом случае застывший металл шва удерживает сварочную ванну. Для полного предотвращения вытекания жидкого металла ванны осуществляют поперечные движения электродом, которые позволяют управлять тепловым потоком и получать валик увеличенной ширины, равной 2-3 диаметрам электрода, что обеспечивает быстрое затвердевание жидкого металла.
Сварку сверху вниз применяют при малой толщине металла или при выполнении первого слоя многослойного шва. В этом случае подтекающий под дугу жидкий металл уменьшает возможность образования сквозных прожогов. Для улучшения условий формирования шва амплитуда колебаний электрода должна быть небольшой, а дуга очень короткой.
В горизонтальном положении для предупреждения стекания жидкого металла ванны скос кромок стыковых соединений делают на одной верхней детали (рис. 8, д). В нахлесточных соединениях удержанию расплавленного металла способствует горизонтальная кромка нижнего листа. Колебательные движения электродом совершают по спирали.
В потолочном положении (рис. 8, г) сила тяжести препятствует переносу электродного металла и вызывает стекание расплавленного металла, поэтому объем сварочной ванны должен быть небольшим. Это достигают применением электродов малого диаметра (3…4 мм) и небольших сварочных токов. Основным условием получения качественного шва является поддержание короткой дуги путем периодических замыканий электрода с ванной жидкого металла. Одновременно электроду сообщают поперечные колебательные движения.
Повышение производительности ручной сварки.
Существует три основных направления повышения производительности: во-первых, за счет увеличения коэффициента наплавки, во-вторых, за счет большей доли участия основного металла в формировании шва и, в-третьих, при использовании специальных методов сварки покрытыми электродами.
Введение в состав покрытия железного порошка приводит к повышению коэффициента наплавки до 18 г/А-ч. В этом случае в образовании шва принимает участие не только металл электродного стержня, но и металл, вводимый в состав покрытия. Например, при увеличении в рутиловом покрытии электродов содержания железного порошка с 20% до 50…60% производительность сварки в нижнем положении возрастает примерно в 1,5…2 раза.
Сварка с глубоким проплавлением позволяет увеличивать долю участия основного металла в металле шва, чем и обеспечивается повышение производительности. При этом способе сварку ведут, опираясь покрытием электрода на кромки свариваемого металла. Используют электроды с повышенной толщиной покрытия при массе покрытия 60…80% массы стержня и отношении диаметра электрода к диаметру стержня 1,5…1,6. Таким способом удается выполнять одностороннюю сварку встык без разделки кромок стальных листов толщиной 8…10 мм и двустороннюю сварку листов толщиной 16…18 мм.
Сварка наклонным электродом (рис. 9, а) позволяет повысить производительность труда в 2,5…3 раза за счет одновременного обслуживания одним сварщиком до 3…4 постов. При этом способе используют приспособление, состоящее из штанги, электрически изолированной от свариваемого металла, и обоймы, к которой подводят ток от источника питания сварочной дуги. Для фиксирования штанги на изделии используют струбцины или постоянные магниты. Плавящийся покрытый электрод устанавливают наклонно, опирают на изделие и закрепляют в обойме, которая во время плавления электрода скользит под действием силы тяжести по штанге, при этом дуга перемещается вдоль свариваемых кромок, образуя шов. Этим способом можно выполнять стыковые и угловые швы.
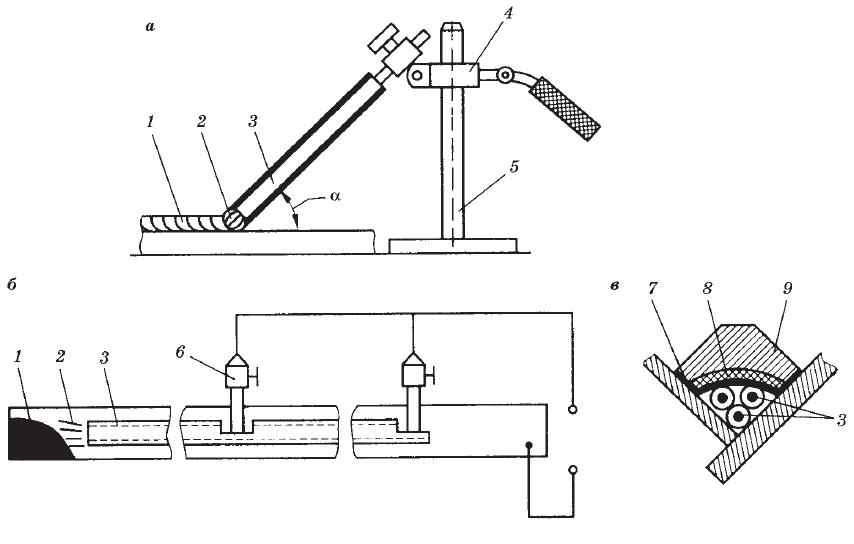
1 — шов; 2 — дуга; 3 — электрод; 4 — обойма; 5 — штанга; 6 — контакт; 7 — бумага; 8 — слой меди; 9 — стальная накладка; а — угол наклона электрода.
Для сварки используют специальные электроды, которые при диаметрах 4…8 мм имеют длину 450…1000 мм, а при диаметрах 6…10 мм — длину 700…1200 мм. Сварочный ток подбирают из расчета
Iсв = (40…45)d, А.
Сварка лежачим электродом также позволяет обслуживать одновременно несколько постов. При этом способе специальный покрытый плавящийся электрод укладывают вдоль свариваемых кромок (рис. 9, б — в). При диаметрах электродов 4 и 8 мм толщина покрытия составляет соответственно 1,5 и 3 мм, а длина электродов — 700 и 900 мм.
Многослойную сварку выполняют, укладывая три или более электродов в разделку кромок стыка или в угол таврового соединения при положении «в лодочку». Ток к электродам подается от нескольких источников.