Дуговая сварка под флюсом — это дуговая сварка, при которой дуга горит под слоем сварочного флюса. Процесс отличается от других видов сварки наибольшей производительностью, высоким уровнем механизации сварочных работ и лучшими гигиеническими условиями труда. Экономичность процесса определяется снижением расхода сварочных материалов за счет сокращения потерь металла на угар, разбрызгивание (не более 3%) и лучшего использования тепла дуги.
Сварку под флюсом применяют для изготовления машиностроительных изделий, крупногабаритных резервуаров, строительных конструкций и труб из сталей, никелевых сплавов, меди, алюминия, титана и их сплавов.
Особенности процесса сварки под флюсом.
Сущность сварки под флюсом.
При этом способе сварки электрическая дуга горит под слоем сварочного флюса между электродной (сварочной) проволокой и свариваемым металлом (рис 1). Флюс засыпают впереди дуги из бункера слоем толщиной 40…80 и шириной 40…100 мм. Ролики специального механизма подают электродную проволоку в дугу. Дуга перемещается в направлении сварки с помощью специального механизма (автоматическая сварка) или вручную (механизированная сварка). Сварочный ток, переменный или постоянный, прямой или обратной полярности, подводится от источника к электродной проволоке и изделию.
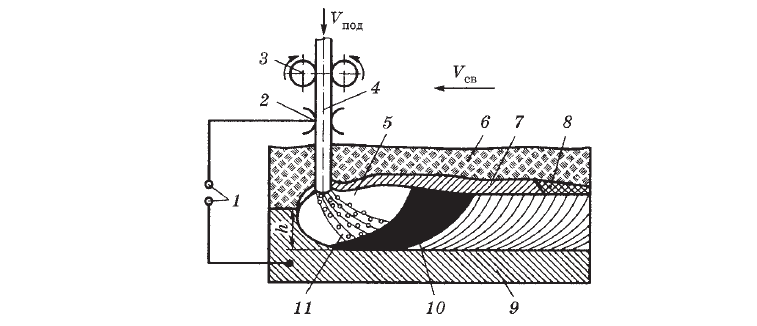
1 — источник тока; 2 — скользящий контакт (токоподвод); 3 — подающий ролик; 4 — электродная проволока; 5 — парогазовый пузырь; 6 — флюс; 7 — расплавленный флюс; 8 — затвердевший шлак; 9 — свариваемый (основной) металл; 10 — сварочная ванна; 11 — сварочная дуга; Ксв,^под — скорость сварки и подачи электродной проволоки; h — глубина проплавления основного металла.
Сварочная дуга горит в газовом пузыре, образованном в результате плавления флюса и металла и заполненном парами металла, флюса и газами. Перенос электродного металла осуществляется каплями, размер которых уменьшается с ростом тока и увеличивается с повышением напряжения, и мало влияет на потери на угар и разбрызгивание. Жидкая пленка флюса изолирует от воздуха зону сварки, а затвердевший флюс образует на поверхности шва шлаковую корку, которая затем отделяется от поверхности шва. Масса флюса, идущего на шлаковую корку, обычно равна массе расплавленной сварочной проволоки.
Роль флюса при сварке.
Флюс влияет на устойчивость дуги, формирование и химический состав металла шва, стойкость швов против образования пор и кристаллизационных трещин.
Устойчивость дуги повышает наличие во флюсе оксидов щелочных и щелочноземельных металлов, которые увеличивают электрическую проводимость и длину дугового промежутка. Соединения фтора, напротив, снижают эти показатели. Таким образом, в зависимости от химического состава флюсы обладают разными стабилизирующими свойствами.
Форма шва определяется стабилизирующими свойствами флюса, его насыпной массой и гранулометрическим составом. Флюс с плохими стабилизирующими свойствами, укорачивая дугу, приводит к формированию узких швов с большой глубиной проплавления и высоким усилением. Флюс с хорошими стабилизирующими свойствами позволяет удлинить дугу, получить широкие швы с малым проплавлением и небольшой высотой усиления.
Насыпная масса флюса пемзовидных плавленых флюсов (0,7…0,9 г/см3) меньше стекловидных (насыпная масса 1,4…1,7 г/см3) одинакового химического состава, поэтому на плавление пемзовидного флюса требуется вдвое меньше энергии и ширина швов больше.
Гранулометрический состав флюса (размер его зерен) также влияет на форму шва. Под мелким флюсом швы получаются более узкие, с большей глубиной проплавления и с большей высотой усиления, чем при использовании крупнозернистого флюса.
Химический состав металла шва определяется взаимодействием между жидким шлаком и металлом. Длительность этого взаимодействия обычно очень невелика и при дуговой сварке может колебаться от нескольких секунд до 1 минуты. Взаимодействие прекращается после затвердевания металла и шлака. Несмотря на кратковременность реакции, взаимодействие между шлаком и металлом при дуговой сварке, как правило, проходит очень энергично, что обусловлено высокими температурами расплавленных металла и шлака, значительными поверхностями их контакта и относительно большим количеством шлака (в среднем 30…40% массы металла).
Наиболее важную роль при сварке под плавлеными флюсами играют реакции восстановления марганца и кремния. Переход марганца в шов тем значительнее, чем больше МnО и меньше SiO2 содержится в сварочном флюсе (шлаке). Чем более кислый флюс, тем переход марганца меньше. Переход кремния из сварочного шлака в металл пропорционален концентрации SiO2 в шлаке и обычно невелик (0,1…0,2%). Увеличение основности флюса снижает переход кремния из шлака в металл.
Поры в швах появляются при повышенной влажности флюса и недостаточной защите зоны сварки от воздуха (малый слой флюса, большие зазоры между свариваемыми кромками) за счет растворения водорода и образования СО2. Компоненты флюса CaF2 и SiO2 способствуют образованию HF, нерастворимого в жидком металле, поэтому содержание водорода в металле шва и вероятность образования пор уменьшаются. Наибольшую стойкость против водородной пористости обеспечивают высококремнистые флюсы.
Чем более развита поверхность зерен флюса, тем больше выделяется газообразных фторидов и тем интенсивней связывается водород в сварочной ванне в нерастворимые соединения. Максимально развитую поверхность имеют пемзовидные флюсы, поэтому они наиболее эффективны против образования пор.
Стойкость швов против образования трещин при сварке низкоуглеродистых и низколегированных сталей обеспечивают высококремнистые флюсы с высоким содержанием оксидов марганца (35…40%). Увеличение содержания марганца в металле сварочной ванны и введение в нее алюминия и титана повышает стойкость швов против образования кристаллизационных трещин, уменьшая вредное влияние серы. Применение флюсов, окисляющих углерод в сварочной ванне, также способствует увеличению стойкости швов против трещин.
Электродные материалы при сварке под флюсом.
В промышленности преимущественное применение находит способ сварки под флюсом сварочной проволокой диаметром от 2 до 5 мм. Однако в некоторых случаях сварку и особенно наплавку целесообразно выполнять ленточными электродами. Лента, применяемая для этих электродов, имеет толщину до 2 мм и ширину до 40 мм. Изменяя форму ленты, можно изменить и форму поперечного сечения шва, достигая повышенной глубины проплавления по его оси или получая более равномерную глубину проплавления по всему сечению шва.
Производительность процесса сварки под флюсом.
По сравнению с ручной дуговой сваркой производительность увеличивается в 5…12 раз. При сварке под флюсом ток по электродной проволоке проходит только в ее вылете (участке от токоподвода до дуги), длина которого обычно не превышает 70 мм. Поэтому нет ограничений по температуре нагрева проволоки и можно использовать повышенные (25…200 А/мм2) плотности сварочного тока. Появляется возможность сваривать металл повышенной толщины без разделки кромок или уменьшить угол разделки и, следовательно, количество электродного металла, необходимого для ее заполнения. Металл шва состоит на 80% из переплавленного основного металла. В результате скорость сварки может быть значительно увеличена. Соответственно, возрастает производительность процесса.
Качество сварного соединения при сварке под флюсом.
Высокое качество достигается за счет надежной защиты расплавленного металла от взаимодействия с воздухом, его металлургической обработки и легирования расплавленным шлаком. Наличие шлака на поверхности шва уменьшает скорость кристаллизации металла сварочной ванны и скорость охлаждения сварного соединения. В результате металл шва не имеет пор, содержит пониженное количество неметаллических включений. Улучшение формы шва и стабильности его размеров, особенно глубины проплавления, обеспечивает постоянство химического состава и других свойств по всей длине шва.
Недостатки сварки под флюсом.
Повышенная жидкотекучесть расплавленного металла и флюса делает возможной сварку только в нижнем положении при отклонении плоскости шва от горизонтальной не более чем на 10…15°С.
Способы сварки под флюсом.
Наиболее часто сварку ведут одним электродом или одной дугой. Для расширения технологических возможностей и повышения производительности сварки можно использовать несколько одновременно горящих дуг.
Многоэлектродная сварка под флюсом.
В этом случае питание дуг сварочным током производится от одного источника. При сварке двумя электродами, если расстояние между ними менее 20 мм, образуется единая сварочная ванна. Электроды могут располагаться поперек или вдоль стыка кромок или занимать промежуточное положение (рис. 2, а). Поперечное расположение электродов применяют для сварки отдельных слоев многослойных швов при увеличенных зазорах в стыке между кромками, а также наплавки. Последовательное расположение электродов позволяет увеличивать глубину проплавления (рис. 2, в).
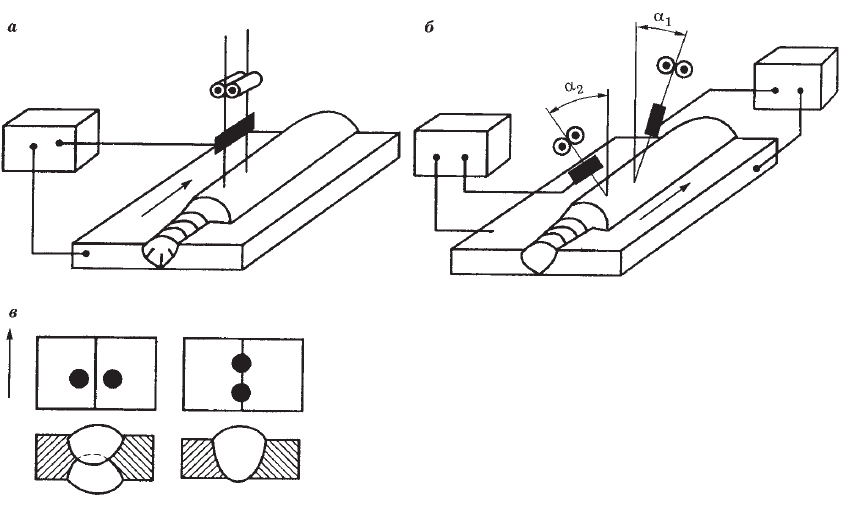
Многодуговая сварка под флюсом.
При этом способе каждый электрод присоединен к отдельному источнику постоянного, переменного тока, или дуги питаются разнородными токами. Образовавшиеся дуги могут гореть в одном газовом пузыре. Электроды располагаются перпендикулярно свариваемой поверхности или наклонно в плоскости, параллельной направлению сварки (рис. 2, б). При отклонении первой дуги на угол α1 растет глубина проплавления, а при отклонении второй дуги на угол α2 увеличивается ширина шва, определяемая этой дугой. Это позволяет избежать подрезов по кромкам шва, резко повысить скорость сварки, а значит, и производительность процесса.
При увеличенном расстоянии между электродами дуги горят в раздельные сварочные ванны. Обычно в таком случае электроды располагаются перпендикулярно поверхности изделия. Сварка по этой схеме позволяет уменьшить вероятность появления закалочных структур в металле шва и околошовной зоны. Это объясняется тем, что первая дуга выполняет предварительный подогрев, который уменьшает скорость охлаждения металла шва и околошовной зоны после прохода второй дуги. Вторая дуга частично переплавляет первый шов и термически обрабатывает его. Изменяя сварочный ток каждой дуги и расстояние между ними, можно получать требуемый термический цикл сварки и таким образом регулировать свойства металла сварного соединения.
Сварка с дополнительной присадкой.
Стыковые швы с разделкой кромок и угловые швы, где требуется большое количество наплавленного металла, иногда выполняют с подачей дополнительного порошкового присадочного металла (ППМ). ППМ предварительно засыпают в зазор между кромками или подают на вылет электрода с помощью специальных дозаторов. Это на 50…70% увеличивает количество наплавляемого металла, повышает производительность сварки, позволяет вести сварку по увеличенным зазорам, снизить перегрев металла шва и уменьшить ширину зоны термического влияния.
Подготовка и сборка деталей под сварку под флюсом.
Основные типы соединений, конструктивные элементы и их размеры регламентируются двумя стандартами: ГОСТ 8713-79 и ГОСТ 11533-75.
Сборка деталей под сварку под флюсом.
Подготовка элементов к сварке под флюсом проводится любым механическим способом или методом термической резки (кислородной, плазменной). Очистка может производиться как механическими способами, так и газопламенной обработкой.
Сборку элементов со стыковыми швами проводят на стеллажах или специальных приспособлениях. Если свариваемые кромки имеют разную толщину, то должен быть сделан скос с одной или двух сторон листа большей толщины. Допустимые смещения (превышение) свариваемых кромок друг относительно друга приведены ниже.
Толщина листов, мм | до 4 | 4…10 | более 10 |
Допустимые смещения кромок, мм | 1 | 2 | 0,5S, но не более 3 мм |
Зазор и взаимное расположение листов при сварке стыковых швов без разделки кромок фиксируется прихватками и технологическими планками. Длина прихваток 50…100 мм, расстояние между прихватками по длине стыка 500…550мм, высота усиления прихватки 3…4 мм. Сварку следует начинать на входных, а заканчивать на выходных технологических планках (рис. 3, а), которые после остывания шва удаляют.
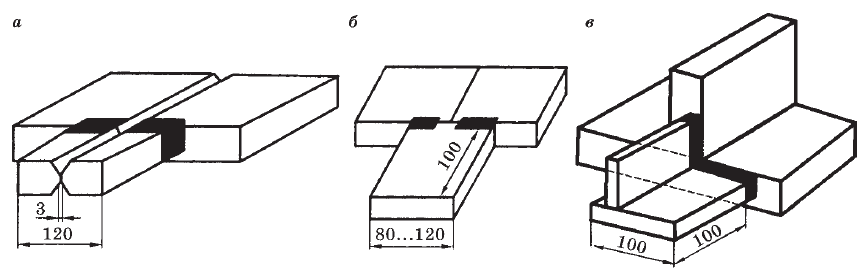
При сборке стыковых соединений с разделкой кромок прихватки по длине стыка ставить не рекомендуется. Листы перед сваркой скрепляют концевыми планками (рис. 3, б). Разделка кромок входных и выходных технологических планок должна быть такая же, как и кромок основного соединения. Длина выходной планки должна быть на 40…50 мм больше кратера основного шва, ширина обычно равна 80…120 мм.
Сборку тавровых соединений обычно выполняют в специальных кондукторах, либо на стеллажах по разметке. Перед сваркой элементы соединяют прихватками (длина прихваток 80…120 мм, катет < 5 мм, расстояние между прихватками 500…600 мм). Перед сваркой к детали приваривают концевые планки (рис. 3, в) и при сварке «в лодочку», если зазор между элементами превышает 2 мм, выполняют подварочный шов со стороны, противоположной первому шву.
Формирующие приспособления при сварке под флюсом.
При сварке однопроходных стыковых швов с проплавлением металла на всю толщину или первого прохода многослойного шва может произойти вытекание сварочной ванны и образование прожога. Для предупреждения прожогов используют формирующие подкладки (съемные из меди, остающиеся из стали, флюсовые подушки, керамические подкладки и гибкие формирующие ленты). Высокое качество шва обеспечивается при плотном поджатии подкладок. Зазор между подкладкой и кромками не должен превышать 1 мм. Если между подкладкой и изделием есть зазоры, то в шве образуются протеки и прожоги.
Сварка на медной подкладке, удаляемой после сварки, весьма распространена. Для провара корня шва и формирования обратного валика в подкладке делают канавку (рис. 4, а — б). Для предупреждения проплавления подкладки в канавку предварительно засыпают флюс. Подкладка может быть неподвижной или скользящей.
Остающуюся стальную подкладку используют в некоторых случаях при сварке сталей. Ее толщина составляет до 40% толщины свариваемого металла (но не более 4…5 мм) при ширине 30…50 мм (рис. 4, в.). Сварной шов должен частично проплавлять и подкладку. Стальную подкладку под стыком закрепляют на прихватках, что требует кантовки изделия. Кроме того, увеличивается расход металла. Зазор между подкладкой и деталью может быть причиной появления трещин в шве при переменных нагрузках.
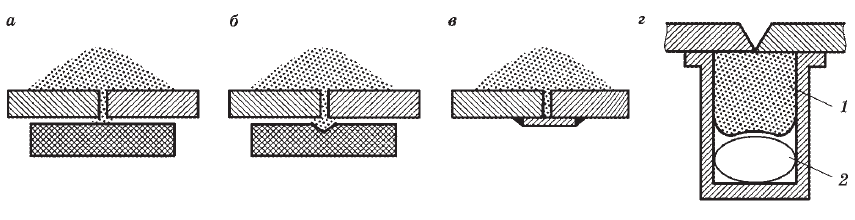
а — медная; б — медная с канавкой; в — стальная; г — флюсовая подушка; 1 — флюс; 2 — брезентовый рукав.
Сварка с предварительной подваркой корня шва технологически более удобна. Подварочный шов можно выполнять вручную покрытыми электродами или плавящимся электродом в защитном газе. Глубина провара должна достигать 1/3 толщины свариваемого металла. Требования к равномерности зазора по длине стыка снижаются.
Сварка на флюсовой подушке (рис. 4, г) допускает меньшую точность сборки стыка под сварку, чем сварка на подкладке. Свариваемые листы укладывают на стеллаж, в котором смонтирована флюсовая подушка. Воздух, подаваемый в брезентовый рукав, поджимает лоток с флюсом.
При сварке кольцевых швов изнутри флюс снаружи поджимается флюсоременной подушкой, движение которой обеспечивается за счет трения о поверхность изделия (рис. 5, а). Сварка первым слоем производится изнутри сосуда, а последующими — снаружи.
При сварке снаружи кольцевых швов труб диаметром до 800 мм часто применяют флюсомедные подкладки, которые могут быть неподвижными или перекатывающимися (рис. 5, б — в).
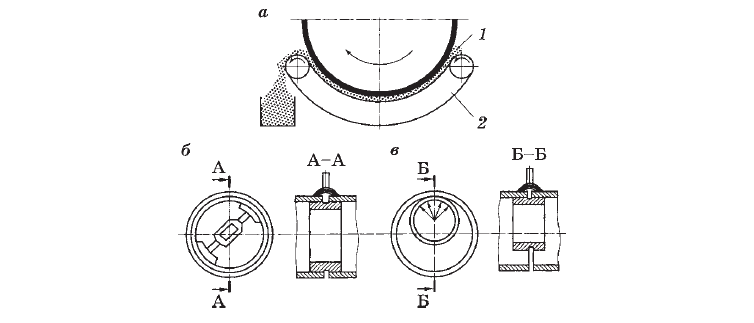
Применяют также самоклеящиеся гибкие флюсонесущие ленты, ленты из стекловолокна, съемные подкладки одно- или многоразового пользования из спрессованного флюса или многослойного керамического формирующего материала в виде специальных пластин. Подкладки закрепляют с помощью эксцентриков, рычажных и винтовых поджимов и другими способами. Если формирование обратного валика при сварке на весу или съемных подкладках является неудовлетворительным, корень шва вырубают или выплавляют и заваривают подварочным швом.
Параметры режима при сварке под флюсом.
Параметры режима условно можно разбить на основные и дополнительные. Основными являются: величина, род и полярность тока, напряжение дуги, диаметр и скорость подачи электродной проволоки, скорость сварки (табл. 1). К дополнительным параметрам режима можно отнести: длину вылета электродной проволоки, состав и строение флюса (плотность, размеры частиц), положение изделия и электрода при сварке.
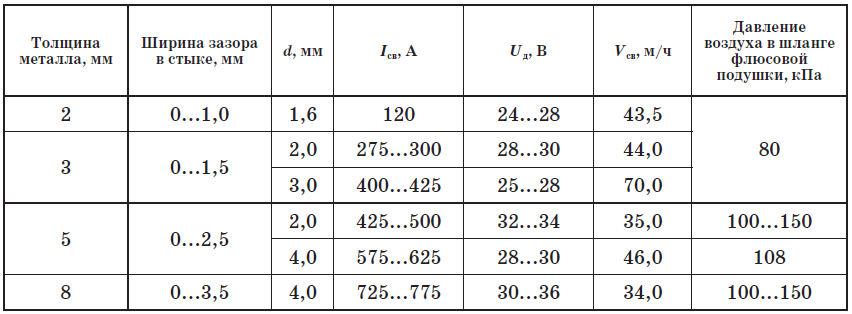
Сварочный ток оказывает наибольшее влияние на форму и размеры шва. При его увеличении (рис. 6, а) интенсивно повышаются глубина проплавления и высота усиления шва, а его ширина возрастает незначительно. Род и полярность тока тоже оказывают влияние на глубину провара. По сравнению с постоянным током прямой полярности сварка на постоянном токе обратной полярности на 40…50%, а на переменном на 25…30% увеличивает глубину проплавления.
Увеличение напряжения на дуге увеличивает ширину сварного шва, глубина проплавления практически не меняется, высота усиления снижается (рис. 6, б).
Диаметр электродной проволоки оказывает значительное влияние на форму и размеры шва, особенно на глубину проплавления, которая возрастает при уменьшении диаметра используемой электродной проволоки.
Скорость подачи электродной проволоки для поддержания стабильного горения дуги при данном диаметре должна соответствовать определенной силе сварочного тока и напряжению на дуге. С увеличением вылета электрода скорость подачи при постоянстве остальных параметров режима необходимо повышать. При использовании легированных проволок с повышенным электрическим сопротивлением скорость подачи должна возрастать.
Влияние скорости сварки (рис. 6, в) на глубину проплавления и ширину шва носит сложный характер. Сначала при увеличении скорости сварки давление дуги все больше вытесняет жидкий металл, толщина прослойки жидкого металла под дугой уменьшается и глубина проплавления возрастает. При дальнейшем увеличении скорости сварки (более 20 м/ч) заметно уменьшается погонная энергия и глубина проплавления начинает уменьшаться. Во всех случаях при увеличении скорости сварки ширина шва уменьшается. При скорости сварки более 70…80 м/ч по обеим сторонам шва возможны несплавления с кромками основного металла или подрезы.
Влияние вылета в диапазоне 50…150 мм при диаметре электрода более 3 мм на форму сварного шва не существенно (рис. 6, г).
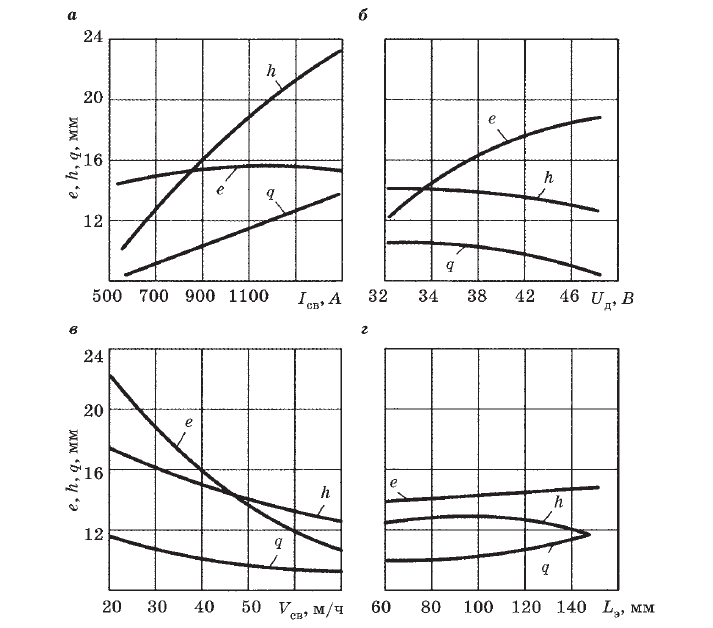
Наклон электрода вдоль шва и положение детали также оказывают влияние на форму шва. Обычно сварку выполняют вертикально расположенным электродом, но в отдельных случаях она может производиться с наклоном электрода углом вперед или углом назад. При сварке углом вперед жидкий металл подтекает под дугу, толщина его прослойки увеличивается, а глубина проплавления уменьшается. При сварке углом назад прослойка уменьшается, проплавление возрастает.
Наклон изделия изменяет глубину проплавления. При сварке на подъем глубина проплавления растет и увеличивается вероятность прожога. При сварке на спуск металл сварочной ванны, подтекая под дугу, уменьшает глубину проплавления и появляется опасность образования несплавлений и шлаковых включений.
Изменение температуры изделия в пределах от -60 до +350°С практически не влияет на форму шва. При подогреве изделия до более высокой температуры возрастает глубина и особенно ширина шва.
Техника сварки под флюсом различных типов швов и соединений.
Стыковые соединения и швы.
Односторонними однопроходными стыковыми швами соединяют металл толщиной до 20 мм. Более толстый металл сваривают двусторонними однопроходными или многопроходными швами.
При односторонней сварке металла толщиной 4…6 мм без разделки кромок стремятся уменьшить зазор при сборке. Стыки более толстого металла (10…12 мм) для увеличения глубины провара собирают с зазором. Но в обоих случаях формирующие подкладки или подварка обязательны.
Сварка на весу (без подкладок) возможна только при условии плотной и точной сборки стыка без зазоров. Глубина провара не должна превышать 2/3 толщины металла, в противном случае возможны прожоги. Сварку на весу односторонних швов применяют для неответственных конструкций из тонкого металла или конструкций, в которых по условиям эксплуатации допустим непровар в корне шва.
Двусторонняя автоматическая сварка менее производительна, чем односторонняя, но более надежна, так как на качество швов в меньшей степени влияет изменение режимов сварки, точность сборки, не требуется сложных устройств для формирования корневой части шва.
Сварка первого шва по этой технологии выполняется на флюсовой подушке или на весу. Сварка второго шва с обратной стороны выполняется после зачистки корневого участка первого шва. Техника сварки первого прохода такая же, как и для односторонних швов.
Во всех случаях режимы сварки необходимо выбирать таким образом, чтобы глубина провара первого слоя составляла примерно половину толщины свариваемого металла. Второй шов сваривают с более глубоким проваром, равным 0,65…0,7 толщины свариваемого металла.
Многопроходные двусторонние стыковые швы применяют для соединения металла средних и больших толщин (преимущественно более 20 мм) с обязательной разделкой кромок. Число слоев определяется толщиной металла и режимом сварки. При многопроходной сварке предпочтительнее Х-образная разделка.
При соединении металлов большой толщины (до 300 мм) сварку ведут в узкий зазор (щелевая разделка) между свариваемыми кромками шириной 16…36 мм. Это позволяет уменьшить деформации и остаточные напряжения в швах.
Сварка тавровых, угловых и нахлесточных соединений.
Сварку угловых швов в таких соединениях выполняют вертикальным электродом «в лодочку», наклонным электродом в угол или вертикальным электродом с оплавлением кромки верхнего листа.
При сварке «в лодочку» (рис. 7, а) шов формируется хорошо, но применение подкладок затруднено, поэтому зазор между деталями не должен превышать 1,5 мм. Техника сварки при положении «в лодочку» не отличается от сварки стыковых швов с разделкой кромок. За один проход можно сварить шов
с катетом до 14 мм. Для обеспечения провара при различной толщине свариваемых элементов сварку осуществляют в несимметричную «лодочку» или несимметрично наклонным электродом.

а — вертикальным электродом таврового соединения «в лодочку»; б и в — наклонным электродом таврового и нахлесточного соединений; г — наклонным электродом многопроходного шва таврового соединения; д — вертикальным электродом нахлесточного соединения; е — вертикальным электродом углового соединения с подкладкой; 1—3 — последовательность выполнения проходов; 4 — подкладка.
Способ сварки наклонным электродом «в угол» не требует специальных мер против вытекания жидкого металла, поэтому допустима сборка с зазором до 3 мм. Возможность образования подреза на вертикальной полке не позволяет при однопроходной сварке получать шов с катетом более 6 мм. Для предупреждения подреза электрод смещают (рис. 7, б и в). Многопроходные швы выполняют так, чтобы ранее наложенный валик препятствовал стеканию металла и шлака при сварке последующих слоев (рис. 7, г).
Сварку нахлесточных соединений вертикальным электродом с оплавлением верхней кромки (рис. 7, д) применяют, когда толщина листа не превышает 8 мм. При этом формируются угловые швы с вертикальным катетом, равным толщине верхнего листа. Горизонтальный катет обычно больше вертикального в 1,5…2 раза.
Угловые соединения можно сваривать вертикальным электродом с медной подкладкой (рис. 7, е) или с гибкими самоклеящимися флюсонесущими лентами.
Сварку нахлесточных и тавровых соединений иногда выполняют точечным или прорезным швом. В этом случае для предупреждения вытекания расплавленного флюса и металла зазор между деталями не должен превышать 1 мм.
Точки можно сваривать с проплавлением верхнего листа толщиной до 10 мм (рис. 8, б) или по предварительно подготовленным отверстиям в верхнем листе, если его толщина более 10 мм (рис. 8, а). При сварке с отверстием диаметр электрода должен быть равен 0,2…0,25 диаметра отверстия.
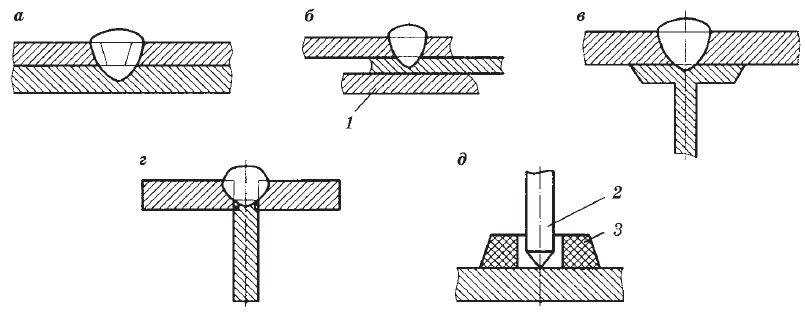
Прорезные швы также могут выполняться по предварительно подготовленным отверстиям удлиненной формы или с проплавлением верхнего листа при его толщине до 10 мм (рис. 8, в и г). Общим недостатком таких швов является трудность контроля их качества и в частности провара нижнего листа.
Приварка шпилек под флюсом.
Для приварки шпилек используют специальные установки и флюсовые шайбы (смесь из 90% флюса и 10% жидкого стекла) высотой 6-10 мм с наружным диаметром 15-20 мм (рис. 8, д). При диаметре шпильки более 8 мм для облегчения возбуждения дуги привариваемый конец затачивают на угол 90°. После обрыва дуги и образования достаточной сварочной ванны шпильку быстро подают до упора.
Сварка стыков труб под флюсом.
Сварку стыковых соединений трубопроводов под флюсом выполняют в нижнем положении с наружной и внутренней стороны стенки трубы. В связи с возможностью стекания шлака минимальный диаметр свариваемых труб обычно более 150 мм. Для регулирования глубины проплавления и формы шва электрод смещают навстречу вращению трубы. Сварку корневого шва часто выполняют ручной дуговой или сваркой в защитных газах плавящимся электродом.