Сварочная проволока — проволока для использования в качестве плавящегося электрода либо присадочного металла при сварке плавлением.
Плавящийся электрод для дуговой сварки — металлический электрод, включаемый в цепь сварочного тока для подвода его к сварочной дуге, расплавляющийся при сварке и служащий присадочным металлом.
Присадочная проволока — сварочная проволока, используемая как присадочный металл и не являющаяся электродом.
Электродная проволока — сварочная проволока для использования в качестве плавящегося электрода.
Сварочная проволока используется в качестве электродной проволоки и присадочной проволоки.
Сварочную проволоку изготавливают сплошной или порошковой.
Для электрошлаковой сварки наряду с проволочными электродами применяют пластинчатые электроды, изготовленные из ленты или листов.
Сварочная сплошная проволока.
Среди сварочных материалов сварочные проволоки сплошного сечения используются в наибольшем объеме. Их широко применяют в качестве электродной проволоки при сварке и наплавке плавящимся электродом в среде защитных газов и под флюсом и как присадочную проволоку при сварке и наплавке неплавящимся электродом в среде защитных газов и газовой сварке. Кроме этого, сплошную проволоку применяют при изготовлении покрытых электродов для дуговой сварки.
Сварочную проволоку изготавливают из различных металлов и сплавов.
Сварочную проволоку получают горячей прокаткой и волочением. Если металл шва должен иметь высокую твердость, то проволока плохо деформируется в горячем и холодном состояниях. В этом случае сварочную проволоку изготавливают литьем в виде присадочных прутков длиной до 1000 мм.
Сварочные проволоки выпускают в соответствии с различными стандартами и техническими условиями. Возможность применения сварочной проволоки данной марки отечественной или импортной, изготовленной в соответствии с конкретным стандартом или техническим условием для сварки конкретного изделия определяется нормативными документами на сварку изделий данной группы технических устройств. На основе многолетнего опыта разработаны государственные стандарты:
ГОСТ 2246-70. «Проволока стальная сварочная».
ГОСТ 10543-98. «Проволока стальная наплавочная».
ГОСТ 7871-75. «Проволока сварочная из алюминия и алюминиевых сплавов»
ГОСТ 16130-90. «Проволока и прутки из меди и сплавов на медной основе сварочные».
В каждом из ГОСТов приведены сведения о химическом составе, о диаметрах проволок, о допусках на них, приведены правила приемки, методы испытаний, упаковки, транспортировки и хранения.
Требования ГОСТ 2246-70 распространяются на холоднотянутую сварочную проволоку из низкоуглеродистой, легированной и высоколегированной стали. Этот стандарт регламентирует химический состав 77 марок сварочной проволоки, используемых в качестве электродной, присадочной, наплавочной и для изготовления покрытых электродов для ручной дуговой сварки. Стандарт не регламентирует механические свойства металла шва, так как они зависят от многих других факторов (доли участия основного металла, марки флюса, защитного газа, режима сварки и т. д.).
В стандарте предусмотрены диаметры проволок (мм): 0,3; 0,5; 0,8; 1,0; 1,2; 1,4; 1,6; 2,0; 2,5; 3,0; 4,0; 5,0; 6,0; 8,0; 10,0; 12,0 и предельные отклонения по ним. Для получения проволок с минимальным содержанием вредных примесей, газов, неметаллических включений по требованию потребителя проволока может быть изготовлена из стали, выплавленной электрошлаковым (Ш), вакуумнодуговым (ВД) переплавом или в вакуумноиндукционных печах (ВИ). По виду поверхности проволока выполняется неомедненная или омедненная (О). Стандарт дает примеры условного обозначения проволок.
Пример условного обозначения проволоки для сварки (наплавки) диаметром 1,2мм, марки Св-08Г2С с омедненной поверхностью:
Проволока 1,2 Св-08Г2С-О ГОСТ 2246-70.
Пример условного обозначения проволоки сварочной диаметром 4 мм, марки Св-04Х19Н9, предназначенной для изготовления электродов:
Проволока 4 Св-04Х19Н9-Э ГОСТ 2246-70.
Условные обозначения марок проволоки состоят из индекса Св (сварочная) и следующих за ним цифр и букв. Цифры, следующие за индексом Св, указывают среднее содержание углерода в сотых долях процента. Последующие буквы указывают на содержание в проволоке химических элементов, обозначаемых следующими буквами: Б — ниобий; В — вольфрам; Г — марганец; Д — медь; М — молибден; Н — никель; С — кремний; Т — титан; Ф — ванадий; Х — хром; Ц — цирконий; Ю — алюминий.
Цифры, следующие за буквенными обозначениями химических элементов, указывают среднее содержание элемента в процентах. При содержании элементов менее 2% цифра не ставится. Более точное содержание элементов дано в стандарте. Буква А в конце условных обозначений марок низкоуглеродистой и легированной проволок указывает на повышенную чистоту металла по содержанию серы и фосфора. В проволоке марки Св-08АА сдвоенная буква А указывает на пониженное содержание серы и фосфора по сравнению с проволокой марки Св-08А. Для высоколегированных проволок не допускается содержание серы и фосфора свыше 0,035%.
Проволока выпускается в виде прутков, в кассетах, катушках и бухтах в герметичной упаковке. Масса используемых катушек зависит от диаметра проволоки и вида сварочного оборудования для механизированной или автоматической сварки и колеблется в пределах от 0,5 до 80 кг. При роботизированной сварке применяют и емкости массой до 250 кг.
При дуговой сварке сталей в защитных газах часть проволоки теряется на разбрызгивание. При этом капли расплавленного электродного металла покрывают основной металл. Трудоемкость очистки изделия сопоставима с трудоемкостью операции сварки. Поэтому ведутся работы по созданию проволок, обеспечивающих более устойчивое горение дуги. Одним из способов, уменьшающих разбрызгивание, является введение в состав проволок материалов с низкой работой выхода электронов. При этом присадки должны иметь температуру кипения, превышающую температуру кипения стали. Этим условиям удовлетворяют редкоземельные металлы, такие как церий, лантан, неодим и другие. Введение в проволоку марки Св-08Г2С редкоземельных элементов в количестве 0,01-0,07% улучшает перенос электродного металла при сварке в среде углекислого газа и уменьшает разбрызгивание.
ГОСТ 10543-98 распространяется на горячекатаную и холоднокатаную проволоку из углеродистой, легированной и высоколегированной стали, предназначенную для механизированной электродуговой наплавки. В ГОСТе приведены твердость наплавленного металла и примерное назначение наплавляемых изделий для каждой марки проволоки. Проволоки классифицируются по химическому составу.
ГОСТ 7871-75 распространяется на тянутую и прессованную проволоку из алюминия и алюминиевых сплавов для сварки плавлением. ГОСТ предусматривает выпуск 14 марок тянутой и прессованной проволоки из алюминия (А1 более 99,5%), алюминиево-марганцевого сплава (СвАМц), алюминиево-магниевых сплавов (СвАМг3, СвАМг4 и др.), алюминиево-кремнистых сплавов (СвАК5 и др.) диаметром 0,8-12,5 мм.
ГОСТ 16130-90 «Проволока и прутки из меди и сплавов на медной основе сварочные» регламентирует хим. состав, диаметры проволок (0,8-8,0 мм) и прутков (6 и 8 мм). Этот стандарт содержит также рекомендации по применению проволок и прутков.
Сварочная порошковая проволока.
Порошковая проволока — сварочная проволока, состоящая из металлической оболочки, заполненной порошкообразными веществами.
Порошок (сердечник), состоящий из смеси минералов, руд, ферросплавов и металлов, предназначен для газошлаковой защиты, раскисления и легирования расплавленного металла, а также для стабилизации дугового разряда. В качестве газообразующих материалов используют карбонаты кальция, магния, натрия (например, мрамор, магнезит, кальцинированную соду), и органические вещества (целлюлозу, крахмал, древесную муку). В качестве шлакообразующих материалов используют рутиловый концентрат, алюмосиликаты, окислы щелочноземельных металлов, флюоритовый концентрат. В качестве раскислителей применяют активные элементы, обладающие высоким сродством к кислороду, в виде ферросплавов (ферромарганец, ферросилиций и др.) и металлических порошков. Легирующие материалы, такие как марганец, кремний, хром, бор, никель и другие, обеспечивающие металлу шва необходимые свойства, вводят также в виде ферросплавов и металлических порошков. Введение дополнительного металла в виде железного порошка (до 30%) позволяет увеличить производительность наплавки и улучшить сварочно-технологические свойства. В качестве компонентов сердечника можно использовать порошки из различных материалов без обработки и связующих веществ. Это дает широкую возможность изменять составы порошковых сердечников и создавать такие композиции, которые невозможно получить в других сварочных материалах. По составу сердечника порошковые проволоки делятся, также как и электроды, по виду покрытия на: рутилорганические, рутиловые; рутил-основные и основные.
Оболочкой для большинства порошковых проволок для сварки и наплавки сталей, сплавов и чугуна является холоднокатаная лента толщиной 0,2-0,8 мм из низкоуглеродистой стали, имеющая высокую пластичность, необходимую для формования и волочения проволоки. Оболочка порошковой проволоки для сварки и наплавки цветных металлов соответствует свариваемому металлу.
По конструкции порошковые проволоки могут быть классифицированы на бесшовные (рис. 1а) и шовные (рис. 1б-д) с одним (рис. 1б) и двумя загибами (рис. 1в, г), а также двухслойные (рис. 1д). Шовную порошковую проволоку изготавливают из ленты. Введение части оболочки внутрь сердечника (рис. 1в-д) обеспечивает более равномерное плавление его и более эффективную защиту металла от воздуха. При размещении всех металлических порошков во внутренней части двухслойной конструкции проволоки (рис. 1д), а газообразующих и шлакообразующих материалов в наружной полости сердечника, обеспечивается лучшая защита расплавленного металла.
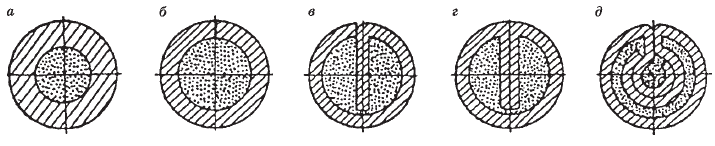
Бесшовные проволоки (рис. 1а) изготавливают из пластичной трубы, заполненной наполнителем, волочением. Ее можно получать малого диаметра (до 1 мм) и обмеднять. Такая проволока негигроскопична. Отношение массы порошкового наполнителя проволоки к массе оболочки находится в пределах 15-40%. Чем больше это отношение, тем легче обеспечить качественную защиту расплавленного металла и легирование металла шва.
По способу защиты порошковые проволоки делятся на самозащитные и используемые с дополнительной защитой зоны сварки газом или флюсом. Наиболее часто в качестве защитной среды используют углекислый газ. Сварка в углекислом газе порошковой проволокой имеет ряд преимуществ по сравнению со сваркой сплошной проволокой. Порошковая проволока, содержащая шлакообразующие и раскислители, позволяет хорошо раскислить металл сварочной ванны, интенсивно обработать его шлаком и снизить содержание в нем газов и неметаллических включений. Швы получаются гладкими, с плавным переходом от основного металла ко шву. Содержащиеся в сердечнике проволоки вещества, обеспечивающие стабильность горения дуги, приводят к минимальному разбрызгиванию и набрызгиванию на свариваемые детали.
Самозащитная проволока — электродная проволока, содержащая вещества, которые защищают расплавленный металл от вредного воздействия воздуха при сварке. Самозащитные проволоки содержат газообразующие и шлакообразующие вещества в достаточном количестве для сварки без дополнительной защиты газом.
Порошковая проволока — универсальный сварочный материал, пригодный для сварки сталей практически любого легирования и для наплавки слоев с особыми свойствами. Порошковую проволоку выпускают диаметром 1-3,2 мм. Для сварки во всех пространственных положениях используют в основном проволоки малых диаметров (чаще диаметром 1,2 мм).
Применение порошковых проволок позволяет обеспечивать производительность расплавления до 10-11 кг/ч, что выше, чем при сварке в углекислом газе сплошной проволокой (до 6-8 кг/ч), и выше, чем при ручной дуговой сварке покрытыми электродами (до 4 кг/ч).
ГОСТ 26271-84 дает классификацию, сортамент и технические требования на порошковую проволоку для сварки углеродистых и низколегированных сталей с временным сопротивлением до 900 МПа диаметром 1,2-6 мм.
По условиям применения сварочную порошковую проволоку подразделяют на газозащитную (ПГ), применяемую для сварки в углекислом газе или газовых смесях, и самозащитную (ПС) — для сварки без дополнительной защиты.
В соответствии с допустимыми пространственными положениями сварки и условиями формирования сварного шва проволоки подразделяют: для нижнего (Н); нижнего и горизонтального на вертикальной плоскости (Г); нижнего, горизонтального на вертикальной плоскости и вертикального (В); для всех положений (У); горизонтального на вертикальной плоскости с принудительным формированием шва (ГП); вертикального с принудительным формированием шва (ВП) и всех положений с принудительным формированием шва (УП).
Стандарт приводит марки отечественных порошковых проволок и дает пример их условного обозначения. Например, проволока марки ПП-АН3 диаметром 3,0 мм, самозащитная (ПС), по значению предела текучести наплавленного металла типа 44, по химическому составу наплавленного металла категории А, обеспечивающей ударную вязкость наплавленного металла не ниже 35 Дж/см2 при температуре -20°С (2), для сварки в нижнем положении (Н): ПП-АН3 3,0 ПС44-А2Н ГОСТ 26271-84.
Проволока порошковая наплавочная
Проволоки предназначены для наплавки поверхностных слоев для работы в условиях абразивного износа и износа от трения при больших удельных давлениях и повышенных температурах, а также в агрессивных средах. ГОСТ 26101-84 «Проволока порошковая наплавочная» приводит марки отечественных проволок, их химический состав, твердость наплавленного металла и типичные объекты (детали) наплавки.
В соответствии с ГОСТ 26101-84 различают проволоку, предназначенную для наплавки под флюсом (Ф), в защитном газе (Г), без дополнительной защиты — самозащитную (С) и универсальную (У) — для сварки под флюсом, в защитном газе и без дополнительной защиты.
По конструкции проволоки могут быть трубчатой стыковой (Т), трубчатой с нахлестом кромки (Н) и двухслойной (Д).
Условное обозначение наплавочной порошковой проволоки по стандарту, например, марки ПП-Нп-30Х5Г2СМ, трубчатой стыковой конструкции (Т), самозащитной (С), диаметром 2,6 мм: ПП-Нп-30Х5Г2СМ-Т-С 2,6 ГОСТ 26101-84.
Лента порошковая наплавочная.
Для дуговой механизированной наплавки поверхностных слоев с особыми свойствами применяют порошковые ленты (ПЛ), состоящие из металлической оболочки и порошка-наполнителя из легирующих материалов и флюса. В соответствии с ГОСТ 26467-85 выпускают ленты шириной 10-18 мм и толщиной 3 и 3,8 мм, предназначенные для наплавки под флюсом (Ф), или без дополнительной защиты (самозащитная порошковая лента) — С, или для наплавки под флюсом и без дополнительной защиты (универсальная порошковая лента) — У. Условное обозначение наплавочной порошковой ленты по стандарту, например, марки ПЛ-Нп-350Х25Н3С3 двухзамковой универсальной: ПЛ-Нп-350Х25Н3С3-А-У ГОСТ 26467-85.
Порошковую ленту поставляют намотанную на кассеты.
Лента наплавочная спеченая.
Наплавочную ленту спеченную (ЛС) изготовляют спеканием порошкообразных компонентов, обеспечивая ей необходимые прочностные и пластические свойства. Ленты поставляют потребителям в рулонах и применяют преимущественно при автоматической наплавке под флюсом для наплавки износостойких и коррозионностойких слоев.
Прутки для наплавки.
Литые прутки для наплавки деталей, работающих в условиях абразивного изнашивания с ударными нагрузками, а также при повышенных температурах в условиях коррозии и эрозии, согласно ГОСТ 21449-75* «Прутки для наплавки», выпускают диаметром 4, 5, 6 и 8 мм длиной 300-500 мм
пяти марок: 3 на основе железа — Пр-С27 (тип ПрН-У45Х28Н2СВМ), Пр-С1 (тип ПрН-У30Х28Н4С3), Пр-С2 (тип ПрН-У20Х17Н2) и 2 на основе кобальта — ПрВ3К (тип ПрН-У10ХК63В5), Пр-В3К-Р ( тип ПрН-У20ХК57В10).
ГОСТ 16130-90 «Проволока и прутки из меди и сплавов на медной основе сварочные» приводит марки прутковых материалов для наплавки контактов в электротехнических приборах, для наплавки деталей, подверженных коррозии при работе в морской воде и в условиях, где необходимы коррозионная и износостойкость.
Выпускают прутки и из других металлов и сплавов длиной до 1000 мм для использования их в качестве дополнительного присадочного металла при ручных дуговых способах сварки неплавящимися электродами и газовой сварке.
Порошки для наплавки и напыления.
Порошки применяют для наплавки и напыления плазменным или газопламенным способом износостойкого слоя на детали машин и оборудования, работающего в условиях воздействия абразивного изнашивания, коррозии, эрозии при повышенных температурах или в агрессивных средах. В соответствии с ГОСТ 21448-75* выпускают порошки с разной величиной частиц: 1,25-0,8 мм — крупный (К); 0,8-0,4 мм — средний (С); 0,4-0,16 мм — мелкий (М) и менее 0,16 мм — очень мелкий (ОМ). ГОСТом предусмотрено 8 марок порошков: ПГ-С27 ( тип ПН- У40Х28Н2С2ВМ), ПГ-С1 (тип ПН-У30Х28Н4С4), ПГ-УС25 (тип ПН-У50Х38Н), ПГ-ФБХ6-2 (тип ПН-У45Х35ГСР), ПГ- АН1 (тип ПН-У25Х30СР), ПГ-СР2 (тип ПН-ХН80С2Р2), ПГ-СР3 (тип ПН- ХН80С3Р3). Порошки поставляют в металлических банках массой до 50 кг.