Общие сведения об автоматизации сборочных работ.
Автоматизация сборочных работ связана с передачей машинам, механизмам и приборам не только исполнительных функций, что имеет место при механизации технологических процессов, но и функций управления этими процессами. Автоматизация технологического процесса может быть полной и неполной. Наиболее часто в промышленности встречается неполная автоматизация технологического процесса сборки, которая сводится к полуавтоматической и автоматической сборке отдельных узлов, а общая сборка осуществляется вручную. Наибольшее распространение полуавтоматическая и автоматическая сборка получили в таких отраслях, как автомобиле- и приборостроение, радиотехническая промышленность.
Сложность автоматизации технологических процессов сборки связана с их значительным разнообразием, что приводит к необходимости создания большой номенклатуры самого различного сборочного оборудования, вызывая существенные затруднения в его изготовлении и внедрении.
В целях сокращения номенклатуры сборочного оборудования для различных технологических процессов сборки необходима типизация этих процессов, которая напрямую связана с технологичностью конструкций деталей и сборочных единиц, применяемых в собираемом узле. Для оценки технологичности деталей, сборочных единиц и механизмов в целом с учетом возможности их автоматической сборки используют различные критерии. Основным из этих критериев является число деталей в собираемом узле (должно быть минимальным). Сложные изделия, состоящие из большого числа деталей, необходимо компоновать из отдельных функциональных блоков, состоящих из 4—12 деталей, которые могут быть собраны независимо друг от друга. Облегчает внедрение автоматической сборки применение унифицированных конструктивных элементов у деталей, входящих в сборочную единицу. Кроме того, должна быть предусмотрена возможность установки всех входящих в сборочную единицу деталей на неподвижную базовую деталь при использовании простейших рабочих движений, а также возможность установления допусков на размеры собираемых деталей, обеспечивающих сборку по методу полной взаимозаменяемости.
Технологические процессы автоматической сборки.
При автоматической сборке наиболее целесообразным является использование типовых технологических процессов, которые применяются главным образом в условиях серийного, крупносерийного и массового производства с устойчивой номенклатурой собираемых изделий.
Основой для разработки типовых технологических процессов автоматической сборки является классификация деталей и сборочных единиц, имеющих различные конструктивные формы и размеры. Детали и сборочные единицы классифицируют по конструктивным, и технологическим признакам, на основе которых их объединяют в группы. Для каждой группы изделий выбирают схему технологического процесса сборки и типовые средства автоматизации.
Технологические процессы автоматической сборки могут быть различными по содержанию, последовательности выполнения сборочных операций, составу применяемого автоматизированного, оборудования и технологической оснастки.
В технологическом процессе автоматической сборки различают два вида операций: основные и вспомогательные. К основным относятся операции, связанные со сборкой разъемных (резьбовых, шпоночных, шлицевых и т.п.) и неразъемных (заклепочных, сварных, клеевых, вальцованных и т.п.) соединений. К вспомогательным операциям автоматической сборки следует отнести подачу деталей к сборочному оборудованию; их ориентирование в положении, необходимом для выполнения соединения; входной контроль; подачу в рабочую зону.
Типовой технологический процесс автоматической сборки включает в себя:
- загрузку деталей, подлежащих сборке, в загрузочное устройство;
- предварительную пространственную ориентацию деталей в загрузочном устройстве;
- подачу собираемых деталей в зону сборки па устройство, обеспечивающее базирование собираемых деталей и их взаимную ориентацию относительно друг друга с требуемой точностью;
- соединение и фиксацию в требуемом положении собираемых деталей;
- контроль качества сборки;
- транспортирование сборочной единицы на следующую операцию или ее съем.
Ориентирование деталей, подлежащих автоматической сборке, состоит из трех этапов: предварительного (в загрузочном устройстве); промежуточного (осуществляется питателем, подающим детали от загрузочного устройства в зону сборки) и окончательного (на сборочной позиции перед началом процесса автоматической сборки).
В качестве загрузочных в процессе автоматической сборки применяют два типа устройств: магазинные и бункерные. В магазинных устройствах детали располагаются рядами с промежутками или без промежутков между ними, а в бункерном — навалом.
Технологическое оборудование для автоматизации сборочных работ.
Конструктивные особенности изделий и особенности технологического процесса их сборки приводят к большому числу конструктивных решений сборочного автоматического оборудования. Такое оборудование подразделяется на одно- и многопозиционное.
Однопозиционное сборочное оборудование.
Если сборочные операции на автоматизированном оборудовании производятся без перемещения базовой детали, то такое оборудование называют одпопозиционным. На однопозиционном оборудовании, как правило, можно собирать изделия, состоящие из двух-трех деталей, К этому типу оборудования относятся механизированные установки, полуавтоматы и автоматы. Однопозиционное оборудование просто по конструкции и надежно в работе, что обусловливает его достаточно широкое применение в сборочном процессе.
Механизированные установки применяют для механизации сборочных процессов в условиях мелкосерийного и единичного производства. К этому виду оборудования относятся прессы, стационарные гайко- и шпильковерты, гидравлические скобы и ряд других устройств.
При использовании однопозиционных сборочных полуавтоматов основные рабочие действия (собственно сборка) выполняются автоматически, а установка базовой и присоединяемых к ней деталей осуществляется вручную.
Многопозиционное сборочное оборудование.
Многопозиционное оборудование можно подразделить на четыре типа:
- дискретного действия, когда сборочные операции выполняются во время остановки транспортирующего устройства, перемещающего базовую деталь;
- ограниченно-прерывистого действия, когда собираемые детали находятся в движении, а рабочие органы неподвижны или имеют ограниченное перемещение относительно неподвижной базы;
- непрерывного действия, когда все рабочие операции выполняются при непрерывном движении базовой детали и рабочих органов автоматического оборудования;
- непрерывно-дискретного действия, когда часть рабочих операций осуществляется во время остановки транспортирующего органа, а часть — в процессе его движения.
Многопозиционное сборочное оборудование включает в себя механизированные, автоматизированные и автоматические сборочные линии.
Механизированные сборочные линии — это линии, на которых основная часть сборочных операций выполняется с применением механизированных инструментов и оборудования. Собираемая сборочная единица перемещается с одной рабочей позиции на другую при помощи конвейера. Съем собранного изделия производится вручную.
Автоматизированные сборочные линии — это линии, на которых основная часть сборочных операций осуществляется с применение полуавтоматического и автоматического оборудования, а оставшиеся операции сборки выполняются, как правило, с применением механизированного инструмента и оборудования. По компоновке автоматизированное многопозиционное оборудование может быть конвейерного или роторного типа.
Оборудование роторного типа применяют при сборке изделий, содержащих до десяти деталей. Если число деталей в сборочной единице превышает это количество, то более целесообразно применение оборудования конвейерного типа.
Автоматическая сборочная линия — это комплекс основного, вспомогательного и подъемно-транспортного оборудования, которое позволяет осуществлять сборочный процесс без участия человека.
Многопозиционное сборочное оборудование оснащено транспортными устройствами, обеспечивающими перемещение базовой детали с одной сборочной позиции на другую.
По степени синхронизации сборочных операций автоматические линии можно подразделить на синхронные, несинхронные и комбинированные.
Синхронные сборочные линии применяют в условиях массового производства при сборке крупногабаритных изделий. На таких линиях сборочная единица последовательно перемещается с одной сборочной позиции на другую с определенным временным интервалом. На синхронных автоматических линиях не предусмотрено межоперационных заделов, что приводит к остановке работы линии в тех случаях, когда из строя выходит хотя бы один механизм.
Несинхронные автоматические линии состоят из замкнутого транспортера, на котором располагаются приспособления-спутники с собираемыми изделиями. Приспособления-спутники не связаны жестко с транспортером, что позволяет, в случае необходимости, создавать межоперационные заделы. Несинхронные линии имеют ряд преимуществ по сравнению с синхронными:
- наличие нескольких приспособлений-спутников между рабочими позициями позволяет компенсировать вынужденные простои отдельных единиц сборочного оборудования;
- возможность сочетать как ручные, так и автоматические операции сборки;
- возможность встраивать в автоматическую линию оборудование, цикл работы которого отличается от цикла работы линии;
- достаточно легко осуществляемая наладка линии на сборку изделий различной конфигурации.
Комбинированные сборочные линии сочетают в себе в той или иной степени участки синхронных и несинхронных линий.
Гибкие производственные системы и сборочные центры.
Необходимыми условиями для создания гибких производственных, систем (ГПС) являются:
- наличие автоматизированного сборочного оборудования с числовым программным управлением (ЧПУ);
- наличие автоматизированных транспортных устройств и автоматических складов материалов, деталей и сборочных единиц, которые управляются с помощью микропроцессорной техники.
Для ГПС характерен модульный принцип компоновки сборочного и вспомогательного оборудования. Отличительной особенностью таких систем является технологическая гибкость, что позволяет применять их в условиях любого типа производства.
В условиях массового производства ГПС обеспечивают рост производительности труда на 50 …60% по сравнению с синхронными сборочными линиями.
В условиях мелкосерийного производства применение ГПС позволяет эффективно осуществлять насыщение сборочного производства средствами механизации и автоматизации, создавать комплексно-механизированные рабочие места сборщиков, сборочные участки и цеха с технологическими комплексами по всему циклу склад—сборка—испытание—установка.
Сборочные центры представляют собой установки широкоуниверсального назначения, которые оснащены манипуляторами для смены сборочного инструмента, подачи собираемых деталей и осуществления сборочных работ. Сборочные центры обеспечивают сборку изделий различных типов, состоящих из большого числа деталей; обладают высокой гибкостью и универсальностью
Специальные методы автоматической сборки.
На практике автоматическую сборку применяют при сборке несложных узлов, состоящих, в большинстве случаев, из мелких деталей (например, штифтов, шайб, втулок). Автоматизация осуществляется за счет использования специальных вращающихся устройств, как правило, пневматического действия. Одно из таких устройств показано на рис. 1, а. Устройство состоит из барабана 3, имеющего горизонтальную ось вращения. В одной из стенок барабана установлена съемная доска L В доске выполнены гнезда со сквозными отверстиями. Размер отверстий соответствует размеру соединяемых деталей 2. Подлежащие сборке детали загружают в барабан навалом.
Под воздействием сжатого воздуха, подаваемого в барабан по трубопроводу 4, детали перемещаются и ориентируются по гнездам с отверстиями. После заполнения всех гнезд съемная доска переставляется в следующий барабан, а ее место занимает новая.
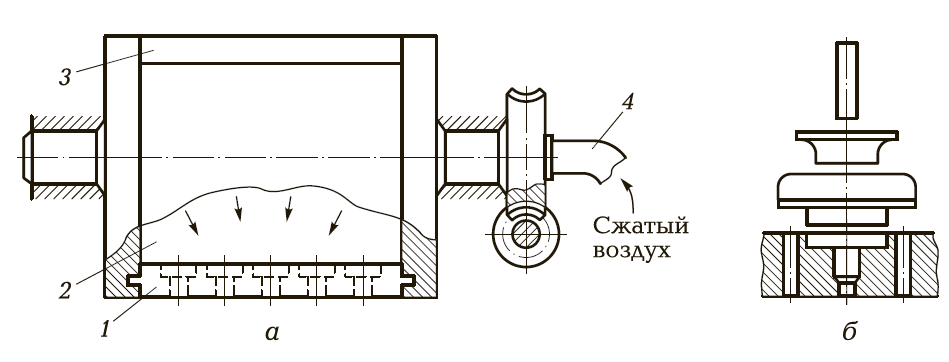
а — схема барабана; 1 — съемная доска; 2 — детали; 3 — барабан; 4 — трубопровод; б — конструкция собираемого узла
Во втором барабане операция повторяется. Доска переставляется из барабана в барабан до тех пор, пока все детали собираемого узла не займут свои места в гнездах сменной доски (рис. 1, б).
Автоматическая сборка соединений с зазорами также может осуществляться в специальных автоматических установках во вращающемся потоке воздуха (вихревым методом).
Такая установка представляет собой трубу (рис. 2), в которой создают вращающийся вихревой поток. Деталь 3 помещают в трубу 2 с зазором 1…5 мм. Под воздействием вращающегося потока воздуха деталь совершает колебательные движения, траектория которых зависит от параметров детали и трубы и характеристики вихревого потока.
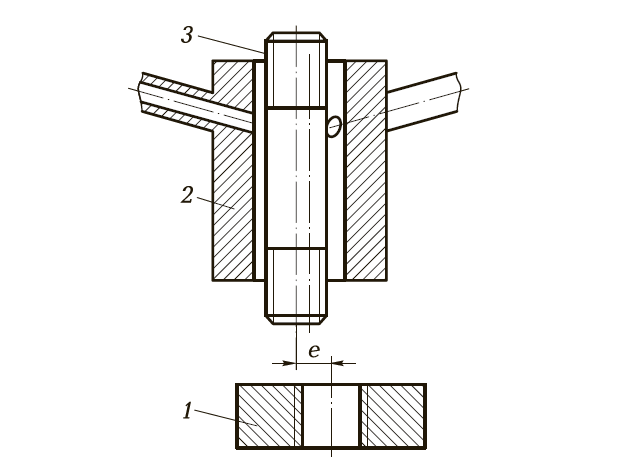
1, 3 — собираемые детали; 2 — ориентирующая труба; е — отклонение собираемых деталей друг от друга
Метод относительной ориентации деталей во вращающемся потоке воздуха характеризуется наличием осевой силы, которая создается этим потоком и может достигать 100 Н. Наиболее целесообразно применение этого метода для выполнения соединения пар деталей, конструкции которых приведены на рис. 3.
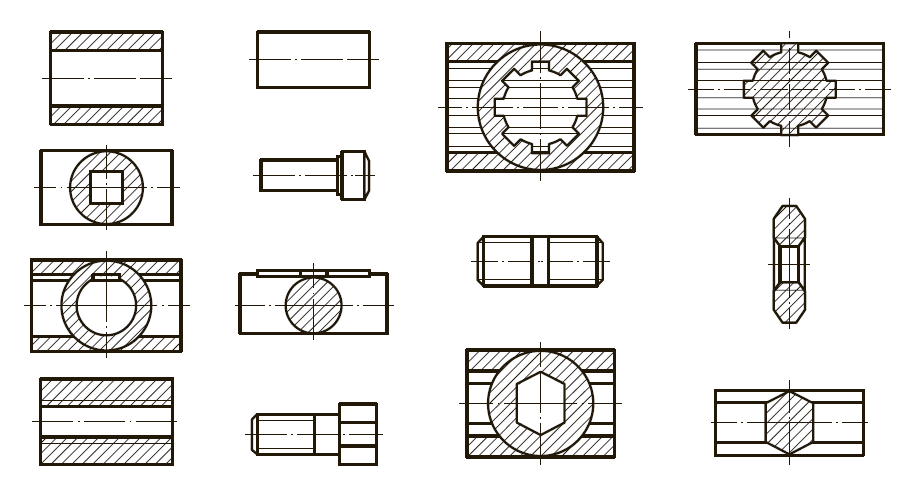