Обработка резьбовых поверхностей — это операция, которая осуществляется посредством снятия слоя материала (стружки) с обрабатываемой поверхности или без снятия стружки, т. е. пластическим деформированием. В первом случае речь идет о нарезании резьбы, а во втором — о ее накатывании. При сборке и ремонте оборудования и проведении монтажных работ применяется нарезание или накатывание резьбы вручную или с помощью ручных механизированных инструментов.
Резьбовой стержень, имеющий на всей длине или на некоторой ее части винтовую поверхность, называют винтом, а отверстие, имеющее винтовую поверхность, — гайкой.
Элементы резьбы (рис. 1) — определенные числовые параметры, характеризующие резьбу.
Шаг резьбы Р — это расстояние в миллиметрах между вершинами двух соседних витков резьбы, измеренное параллельно ее оси.
Высота профиля Н — расстояние от вершины резьбы до основания профиля, измеренное в направлении, перпендикулярном оси резьбы.

α — угол профиля; Р — шаг резьбы; d — наружный диаметр резьбы; d1 — внутренний диаметр резьбы; d2 — средний диаметр резьбы; Н — высота профиля резьбы
Рис. 3.24. Элементы треугольной резьбы: а — угол профиля; Р — шаг резьбы; d — наружный диаметр резьбы; d1 — внутренний диаметр резьбы; d2 — средний диаметр резьбы; Н — высота профиля резьбы
Угол профиля α — угол между прямолинейными участками сторон профиля резьбы.
Наружный диаметр резьбы d — это наибольший диаметр резьбы, который измеряют по ее вершинам в направлении, перпендикулярном оси.
Внутренний диаметр резьбы — это наименьшее расстояние между противоположными впадинами резьбы, измеренное перпендикулярно оси.
Средний диаметр резьбы d2 — это диаметр условной окружности, проведенной посередине профиля резьбы между дном впадины и вершиной выступа, измеренный в направлении, перпендикулярном оси.
Инструменты и приспособления для нарезания наружной и внутренней резьбы вручную. Для нарезания наружной и внутренней резьбы вручную применяют специальные резьбонарезные инструменты (метчики и плашки) и приспособления, позволяющие создать вращающий момент на инструменте, необходимый для обеспечения сил резания в процессе обработки.
Метчик (рис. 2) состоит из двух частей: рабочей, которая обеспечивает процесс резания, и хвостовой, на конце которой выполнен квадратный выступ для установки воротка. Рабочая часть метчика включает в себя режущую (заборную) часть, которая обеспечивает удаление основного припуска на обработку, и калибрующую, осуществляющую окончательную обработку резьбы. Метчики для ручного нарезания резьбы изготавливают в виде комплектов из двух-трех штук (черновой, средний и чистовой), которые помечают круговыми рисками на хвостовой части (одна, две и три риски соответственно).
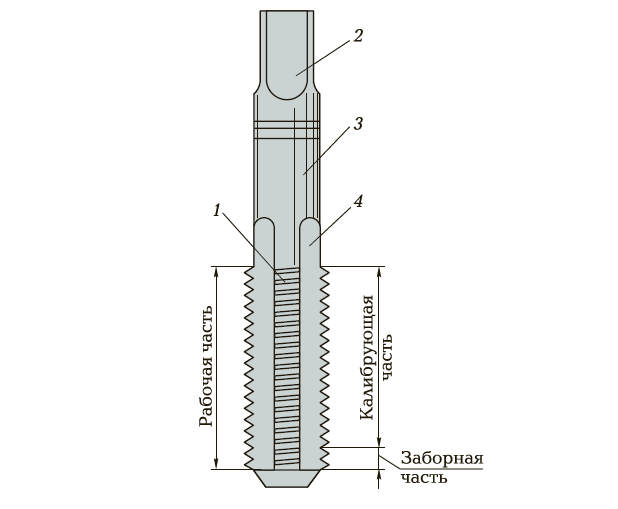
1 — нитка (виток); 2 — квадрат; 3— хвостовик; 4 — канавка
Для создания крутящего момента на режущем инструменте (метчике) применяют специальные приспособления — воротки различных конструкций.
Универсальный вороток (рис. 3) представляет собой рамку с двумя сухарями — подвижным и неподвижным, образующими квадратное отверстие и обеспечивающими закрепление хвостовой части метчика.
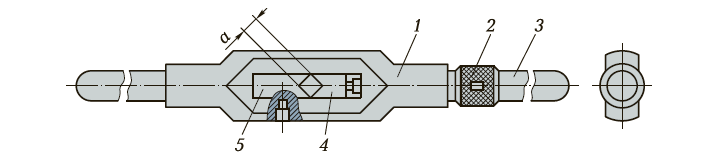
1 — рамка; 2 — муфта; 3 — рукоятка; 4, 5 — соответственно подвижный и неподвижный сухарь; а — сторона квадрата
Вороток с выключающимися кулачками (предохранительный) (рис. 4, а) позволяет предохранять метчик от поломок за счет выведения из зацепления кулачков корпуса и втулки, когда усилие, передаваемое воротком, превышает допустимое.
Торцевой вороток (рис. 4, б) применяют при нарезании резьбы в труднодоступных местах, так как он позволяет работать одной рукой.
Вороток с трещоткой (рис. 4, в) служит для нарезания резьбы в труднодоступных местах, когда за один раз вороток может быть повернут на небольшой угол.
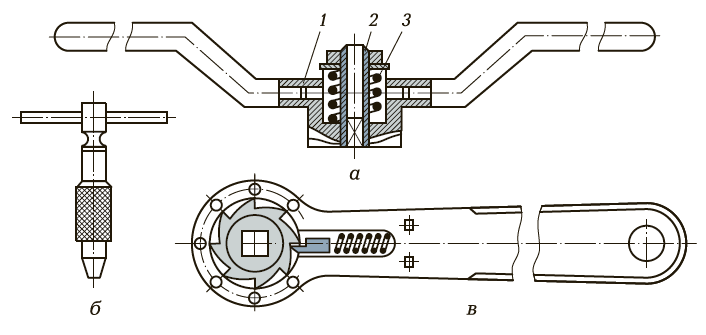
а — предохранительный: 1 — корпус; 2 — втулка; 3 — пружина; б — торцевой; в — с трещоткой
Плашка — инструмент для нарезания наружной резьбы, состоящий из двух частей: заборной и калибрующей. Их назначение такое же, как и у соответствующих частей рабочей части метчика. При ручном нарезании резьбы применяют плашки различных конструкций.
Круглые плашки (рис. 5, а) представляют собой резьбовое кольцо с несколькими канавками для образования режущих кромок и отвода стружки. Их изготавливают цельными и разрезными. Благодаря своим пружинящим свойствам плашки позволяют регулировать величину среднего диаметра нарезаемой резьбы.
Квадратные плашки (рис. 5, б) состоят из двух половин, которые укрепляют в специальной рамке с рукоятками — клуппе.
Клупп обеспечивает возможность регулирования среднего диаметра нарезаемой резьбы.

а — круглая: 1 — заборная часть; 2 — калибрующая часть; 3 — стружечная канавка; б — квадратная (раздвижная): 1 — клупп; 2 — плашка
Для создания вращательного момента и обеспечения процесса резания при нарезании наружной резьбы плашками применяют специальные приспособления — воротки (для круглых плашек) и клуппы (для разрезных плашек).
Вороток для круглых плашек (рис. 6) представляет собой круглую рамку с выточкой, в которой помещается круглая плашка, удерживаемая от проворачивания при помощи трех стопорных винтов. Четвертый винт позволяет регулировать средний диаметр резьбы при применении для ее нарезания разрезной круглой плашки.
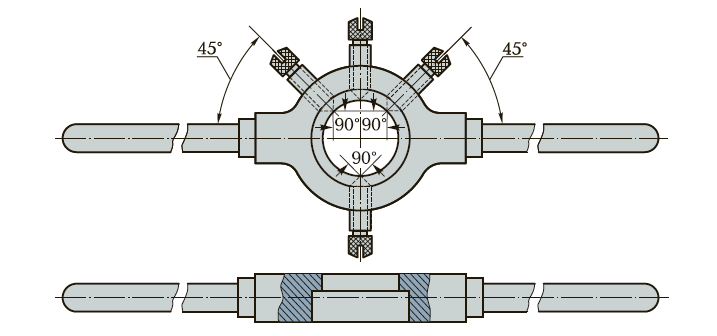
Клупп (см. рис. 5, б) представляет собой квадратную рамку с выступами, в которые входят пазы плашки. Одну из половин плашки можно перемещать при помощи винта, регулируя величину среднего диаметра нарезаемой резьбы.
Ручной механизированный инструмент для нарезания внутренней резьбы может быть оснащен как пневматическим, так и электрическим приводом.
Резьбонарезатель с пневматическим приводом (рис. 7) предназначен для нарезания резьбы небольшого диаметра. Пневматический двигатель 1 приводит во вращение шпиндель 4. При нажатии на рукоятку 3 корпуса происходит нарезание резьбы. При ослаблении нажатия на рукоятку 3 шпиндель 4 под воздействием пружины смещается и происходит реверсирование его движения. При этом метчик 5 ускоренно вывинчивается из отверстия заготовки 6. Включение инструмента осуществляется нажатием на курок 2.
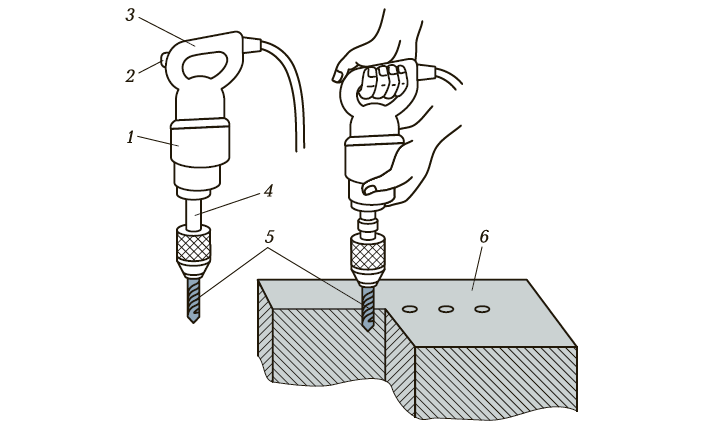
1 — пневмодвигатель; 2 — курок; 3 — рукоятка; 4 — шпиндель; 5 — метчик; 6 — заготовка
Резьбонарезатель с электрическим приводом (рис. 8) снабжен встроенным электрическим двигателем, реверсивным механизмом и редуктором.
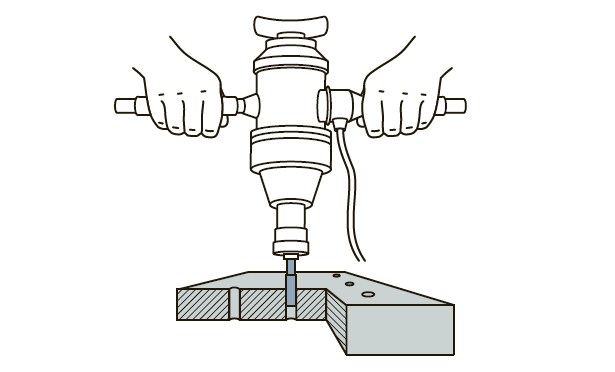
Подготовка стержней и отверстий под нарезание резьбы. В процессе нарезания резьбы происходит не только удаление слоя материала с поверхности заготовки, но и пластическое деформирование обрабатываемой поверхности, которое сопровождается выдавливанием части металла заготовки из впадин витков резьбы к вершинам. Это явление должно учитываться при определении диаметров стержней и отверстий под нарезание резьбы. Поэтому размеры заготовок целесообразно определять при помощи справочных таблиц, в которых они приводятся с учетом всех факторов, влияющих на процесс резания.
На практике диаметр отверстия под резьбу выбирают равным ее номинальному размеру, уменьшенному на величину шага. Например при нарезании резьбы М10 диаметр отверстия должен быть 10 — 1,5 = 8,5 мм.
При нарезании наружной резьбы диаметр стержня должен быть меньше номинального диаметра резьбы на 0,1 …0,2 мм в зависимости от ее размера.
При обработке наружной и внутренней резьбы необходимо придерживаться ряда правил.
- Нарезание резьбы вручную необходимо выполнять при обильном смазывании метчика или плашки машинным маслом.
- При нарезании резьбы вручную следует периодически срезать образующуюся стружку обратным ходом метчика или плашки на 1/2 оборота.
- После нарезания резьбы необходимо произвести контроль ее качества: внешним осмотром (не допуская задиров и сорванных ниток) и резьбовым калибром, проходная часть которого должна навинчиваться легко, от руки.
Правила нарезания наружной резьбы вручную сводятся к следующему.
- Проверить перед нарезанием резьбы диаметр стержня, который должен быть меньше номинального размера резьбы на 0,1 …0,2 мм.
- Выполнить на вершине стержня заборную фаску таким образом, чтобы она была концентрична оси стержня. При этом ее диаметр не должен быть меньше внутреннего диаметра резьбы, а угол наклона относительно оси стержня должен составлять 60°.
- Следует закреплять стержень в тисках прочно, проверяя его перпендикулярность зажимным губкам при помощи угольника.
Правила обработки внутренней резьбы вручную следующие.
- Проверить соответствие диаметра отверстия размеру нарезаемой резьбы.
- Проверить соответствие глубины отверстия требованиям чертежа при нарезании глухой резьбы.
- Проверить при помощи угольника перпендикулярность оси метчика плоскости заготовки, в отверстии которой нарезается резьба.
- Использовать при нарезании резьбы все метчики комплекта.
- Периодически очищать от стружки глухие отверстия при нарезании в них резьбы.
Нарезание резьбы на трубах осуществляется с применением специальных инструментов — клуппов и резьбонарезных гребенок.
Клупп с раздвижными плашками (рис. 9) — устройство, наиболее часто применяемое для нарезания наружной резьбы на трубах. Клупп комплектуют набором раздвижных плашек для нарезания резьбы диаметром 1/2…3/4; 1…11/4; и 11/2 …2″. Клупп смонтирован таким образом, что перемещающиеся в его корпусе 1 четыре плашки 5 могут одновременно приближаться к центру или расходиться от него. Перемещение плашек обеспечивается специальным поворотным устройством, приводимым в действие рукояткой 4. Точная установка плашек на размер нарезаемой резьбы производится по лимбу, размещенному на корпусе, а установочные перемещения осуществляются за счет червячной передачи 3. После установки положение плашек фиксируют специальным устройством — «собачкой». Усилие резания передается на инструмент при помощи рукояток 2.
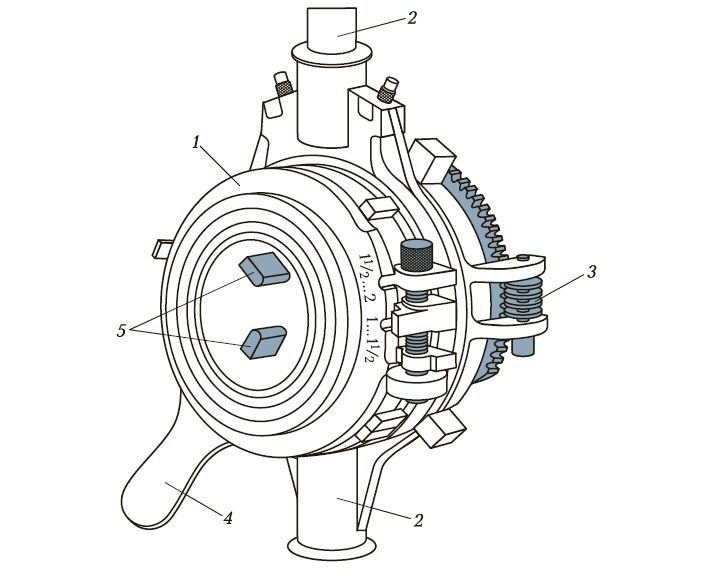
1 — корпус; 2 — рукоятки; 3 — червячная передача; 4 — рукоятка перемещения плашек; 5 — плашки
Круглая резьбонарезная гребенка (рис. 10, а) применяется для нарезания трубной резьбы на токарных и сверлильных станках. Гребенки выпускаются комплектами из четырех штук. Нарезание резьбы производится с применением специальной винторезной самооткрывающейся головки (рис. 10, б).

Для облегчения работы инструмента, повышения качества получаемой при нарезании резьбы применяют СОТС. Их выбор зависит от материала обрабатываемой заготовки. Например, для охлаждения стальных заготовок (конструкционная, инструментальная и легированная сталь) применяют эмульсию. Для охлаждения чугуна и алюминия следует использовать керосин. Нарезание резьбы в медных, латунных и бронзовых заготовках может производиться без охлаждения.