Протяжки состоят из следующих основных частей: хвостовика, шейки, передней и задней направляющих, режущей и калибрующей частей, заднего хвостовика (рис.1).
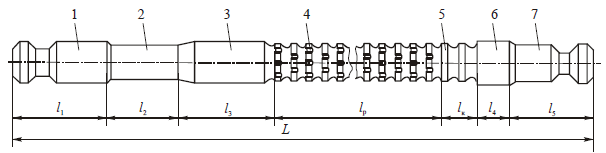
Хвостовик служит для присоединения протяжки к патрону станка. Основные типы и размеры хвостовиков стандартизированы (ГОСТ 4044-70). При этом диаметр хвостовика должен быть меньше диаметра отверстия под протягивание на 1…2 мм.
Шейка и следующий за ней переходный конус выполняют вспомогательную роль. Их длина должна обеспечивать возможность присоединения протяжки к патрону перед началом протягивания. Переходный конус обеспечивает свободное вхождение передней направляющей в протягиваемое отверстие. Диаметр шейки берется меньше диаметра хвостовика на 0,3…1,0 мм.
Передняя направляющая служит для центрирования оси заготовки относительно оси протяжки перед протягиванием, чтобы исключить перекос заготовки, который может привести к поломке протяжки или порче обработанной поверхности. Длина передней направляющей должна быть равна длине L0 протягиваемого отверстия, а при больших длинах — не менее 0,6L0. Форма передней направляющей должна соответствовать форме отверстия в заготовке, а допуск на диаметр направляющей берется по е8.
Задняя направляющая выполняет ту же роль, что и передняя, предохраняя протяжку от перекоса при выходе ее калибрующей части из обработанного отверстия. По длине она несколько меньше длины передней направляющей, а ее диаметр выполняется точнее, с допуском по f7. Форма задней направляющей должна быть такой же, как у протянутого отверстия.
Для автоматического возврата протяжки в исходное положение после протягивания, особенно при больших длине и диаметре протяжки, после задней направляющей иногда предусматривается задний хвостовик, закрепляемый в патроне каретки станка. По форме он подобен переднему хвостовику. Наличие этого хвостовика также предохраняет протяжку от провисания и перекоса в отверстии и позволяет избежать искажения формы и размера обработанного отверстия.
Режущая (рабочая) часть протяжки служит для удаления припуска и формирования поверхности протянутого отверстия. Она содержит черновые и чистовые, а при групповой схеме резания еще и переходные зубья, располагаемые на ступенчато-конической поверхности. Длина режущей части равна произведению числа зубьев на их шаг, который, в свою очередь, зависит от требований к точности протягиваемого отверстия, шероховатости его поверхности и величины снимаемого припуска. Диаметры зубьев рассчитывают исходя из принятой схемы резания.
Калибрующая часть содержит 4…10 зубьев одинакового диаметра, равного диаметру последнего чистового зуба, и служит для калибровки отверстия, уменьшения рассеивания его размеров, а также является запасом на переточку: по мере износа чистовых зубьев калибрующие зубья заточкой могут быть переведены в чистовые. Тем самым увеличивается общий срок службы протяжки.
Калибрующие зубья припуск не срезают, а удаляют микронеровности поверхности, остающиеся после прохода чистовых зубьев, и обеспечивают направление протяжки в отверстии.
Конструкция режущей части протяжки определяется принятой схемой резания, под которой понимают принятый порядок последовательного срезания припуска.
Различают следующие схемы резания: а) по способу деления припуска по толщине и ширине — одинарная и групповая; б) по способу формирования обработанной поверхности — профильная, генераторная и комбинированная.
Рассмотрим первые две схемы на примере обработки круглых отверстий.
Одинарная схема резания характерна тем, что каждый зуб протяжки срезает припуск определенной толщины по всему периметру обрабатываемого отверстия за счет того, что диаметр каждого последующего зуба больше диаметра предыдущего на величину 2αz, где αz — подъем или подача на зуб (αz=sz).
Так как кольцевая стружка недопустима, то для деления стружки по ширине на режущих кромках необходимо делать стружкоделительные канавки V-образной формы (рис.2, а), которые располагают в шахматном порядке при переходе от одного зуба к другому. Стружкоделительные канавки имеют глубину h =0,4.. .1,0 мм и ширину Sк=0,6…1,2 мм в зависимости от диаметра протяжки. Снимаемые каждым зубом стружки получаются в виде отдельных частей с ребром жесткости толщиной 2αz за счет того, что на участке канавки предыдущего зуба стружка не снимается. Ребро жесткости ухудшает свертываемость стружки в канавках между зубьями, из-за чего приходится значительно снижать величину подачи на зуб. Это приводит к нежелательному увеличению длины протяжки. Так, для цилиндрических протяжек ориентировочные значения толщин среза равны: при обработке сталей — αz=0,02…0,04 мм; чугуна — αz=0,03…1,0 мм; алюминия — αz=0,02…0,05 мм; бронзы и латуни — αz=0,05…0,12 мм.
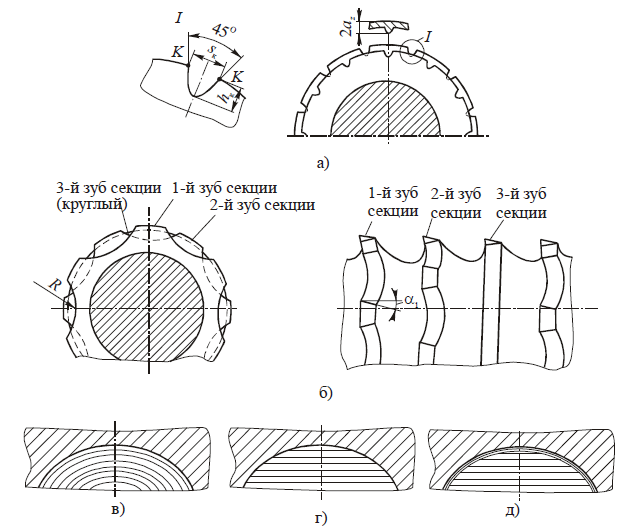
При большей толщине среза жесткость стружки мешает ее завиванию во впадине между зубьями. Стружка упирается в дно впадины, в результате чего возможны ее заклинивание и даже поломка протяжки.
Стружкоделительные канавки прорезают шлифовальным кругом при небольшом (2…3°) поднятии заднего центра протяжки для создания заднего угла по дну канавки. При этом ослабляются режущие кромки зубьев в точках K пересечения канавок с задней поверхностью. Это приводит к более интенсивному износу зубьев на этих участках и, соответственно, к снижению стойкости протяжки.
Схема группового резания (рис.2, б) отличается от вышеописанной тем, что все режущие зубья делятся на группы или секции, состоящие из 2…5 зубьев, в пределах которых зубья имеют одинаковый диаметр. Припуск по толщине делится между группами зубьев, а по ширине — между зубьями группы благодаря широким выкружкам, выполненным в шахматном порядке. Каждый зуб снимает отдельные части припуска участками режущей кромки, где нет выкружек. При этом благодаря большой ширине выкружек снимаемая стружка не имеет ребер жесткости, хорошо скручивается в канавках между зубьями, даже при увеличении толщины среза до az = 0,3…0,4 мм при обработке стали и до az = 1,0…1,2 мм — при обработке чугуна. За счет этого при групповой схеме резания возможно существенное сокращение длины режущей части протяжки.
Широкие выкружки на зубьях обеспечивают увеличение угла стыка выкружек и режущих кромок до 130…150°. Это в сочетании с задними углами α1= 4…6° на вспомогательных режущих кромках, полученными при вышлифовывании выкружек, обеспечивает повышение стойкости протяжек в 2…3 раза по сравнению с одинарной схемой резания.
При проектировании протяжек с групповой схемой резания последний зуб в группе, не имеющий выкружек и выполняющий роль зачистного, делают с занижением на 0,02…0,04 мм по диаметру относительно других зубьев. Это необходимо, чтобы избежать образования кольцевых стружек, возможных при упругом восстановлении обработанной поверхности после прохода прорезных зубьев.
Недостатком групповой схемы резания является повышенная трудоемкость изготовления протяжки по сравнению с одинарной схемой.
Форма режущих кромок зубьев протяжки определяется принятой схемой формирования обработанной поверхности.
При профильной схеме (рис.2, в) контур всех режущих кромок подобен профилю протягиваемого отверстия. При этом в окончательном формировании обработанной поверхности принимают участие только последние зубья, а остальные служат для удаления припуска. При сложной форме отверстий использование такой схемы нецелесообразно, так как усложняет изготовление протяжки. Профильная схема в основном применяется при формировании простых по форме поверхностей, например, круглых или плоских.
При использовании генераторной схемы (рис. 2, г) форма режущих кромок не совпадает с формой обработанной поверхности, которая формируется последовательно всеми зубьями. В этом случае упрощается изготовление протяжки путем шлифования напроход всех зубьев абразивным кругом одного профиля. Однако при этом на обработанной поверхности возможно появление рисок (ступенек) вследствие погрешностей заточки зубьев, что ухудшает качество обработанной поверхности.
При высоких требованиях к шероховатости обработанной поверхности рекомендуется использовать комбинированную схему (рис. 2 , д), при которой два-три последних режущих и калибрующие зубья работают по профильной, а остальные — по генераторной схемам.