Подшипник скольжения состоит из корпуса и помещенного в него вкладыша, на который опирается вал. Корпус изготавливают обычно из чугуна, а вкладыш — из материала, который в паре с материалом вала обеспечивает наименьший коэффициент трения. Для изготовления вкладышей подшипника используют антифрикционные чугуны, бронзы, а также пластические массы, выбор которых зависит от условий работы подшипника скольжения. При изнашивании замена вкладыша дешевле, чем замена подшипника в целом.
По конструкции различают подшипники с разъемным и неразъемным корпусом.
Вкладыш неразъемного подшипника скольжения выполняется в виде втулки, которая устанавливается (чаще всего прессованием) в отверстие корпуса.
Вкладыш разъемного подшипника состоит из двух частей: нижней и верхней, которые монтируют в корпусе и крышке подшипника.
При работе в режиме жидкостного трения применяют подшипники скольжения с сегментными вкладышами, которые обеспечивают образование нескольких масляных клиньев, а соответственно, и надежную работу узла.
В подшипниках скольжения для увеличения несущей способности и увеличения надежности работы применяют самоустанавливающиеся сегменты.
В современном машиностроении применение подшипников скольжения ограничено определенными условиями эксплуатации. В основном их используют в следующих случаях: для быстроходных валов, при работе которых долговечность подшипников качения очень мала; при необходимости особо точной установки валов; при применении в механизме валов очень большого диаметра, для которых не изготавливают серийно подшипники качения; для коленчатых валов, когда в процессе сборки требуется разъемный подшипник; для валов, испытывающих ударные нагрузки (используются демпфирующие свойства масляного слоя подшипника скольжения); если по условиям эксплуатации подшипник работает в воде или в агрессивных средах; для тихоходных передач, так как в этих случаях подшипник скольжения оказывается проще по конструкции и дешевле, чем подшипник качения.
В зависимости от условий эксплуатации используют подшипники скольжения различных конструкций: радиальные, воспринимающие нагрузки, перпендикулярные оси вала; упорные (подпятники), воспринимающие нагрузки, направленные вдоль оси вала; радиально-упорные, которые могут одновременно воспринимать нагрузки, направленные как перпендикулярно оси вала, так и вдоль нее (такие подшипники применяют крайне редко; при одновременном действии радиальных и осевых нагрузок чаще применяют одновременную установку в узел радиального и упорного подшипников).
К узлам с подшипниками скольжения предъявляют следующие технические требования:
- конструкция подшипника и материал, из которого он изготовлен, должны быть такими, чтобы трение и износ были минимальными;
- конструкция подшипника должна обеспечивать достаточную прочность и жесткость, чтобы противостоять усилиям, воздействующим на подшипник вследствие деформации;
- поверхности контакта должны воспринимать действующие на них усилия без выдавливания смазки, а также отводить теплоту, возникающую за счет сил трения в процессе работы подшипника;
- конструкция подшипника должна обеспечивать простоту сборки и обслуживания;
- отверстие в подшипнике должно иметь правильную цилиндрическую форму;
- торцы подшипника должны быть перпендикулярны его оси;
- отверстия всех опор вала должны быть соосны;
- втулки неразъемных подшипников скольжения должны надежно закрепляться в корпусе;
- вкладыши разъемных подшипников скольжения должны быть точно подогнаны по гнездам корпуса и крышки;
- в разъемных подшипниках толщина прокладок для регулирования зазора должна быть не более 2 мм;
- слой залитого в подшипники баббита должен быть ровным, без раковин и отслоений.
Для повышения КПД, а также для снижения до минимума трения, изнашивания и нагрева сопрягаемых поверхностей применяют различные типы смазочных материалов.
В зависимости от толщины масляного слоя различают несколько режимов работы подшипников скольжения: сухое трение (работа без смазки) — в нормально работающих подшипниках скольжения не встречается; полусухое трение — имеет место при неустоявшемся режиме работы подшипника скольжения, а также при недостаточной смазке (коэффициент трения при этом составляет 0,1 …0,5); полужидкостное трение, при котором большая часть поверхности контакта разделена слоем смазки, но отдельные элементы сопрягаемых поверхностей соприкасаются (коэффициент трения при этом составляет 0,008…0,08; в этом режиме работает большинство подшипников скольжения); жидкостное трение, при котором смазка полностью отделяет вращающуюся цапфу от неподвижной опоры (коэффициент трения в этом случае составляет 0,001…0,008; в режиме жидкостного трения работают точно изготовленные подшипники при относительно малых нагрузках и больших скоростях вращения (например, подшипники шлифовальных станков).
Уменьшение скорости скольжения, увеличение нагрузки и температуры нагрева подшипников скольжения в процессе работы могут привести к нарушению режима жидкостного трения и переходу к работе в режиме полужидкостного трения.
Для обеспечения наиболее благоприятного для работы подшипника скольжения режима жидкостного трения необходимо создать избыточное давления в местах сопряжения деталей подшипникового узла. Создание избыточного давления может быть обеспечено гидростатическим (с помощью насоса) или гидродинамическим (с помощью вращения вала) путем. При вращении вал под воздействием внешних сил занимает эксцентрическое положение, и в зазор, возникающий между валом и подшипником, поступает масло. В образовавшемся масляном клине создается избыточное гидродинамическое давление, обеспечивающее жидкостное трение.
Для смазывания подшипников скольжения применяют различные смазывающие материалы, которые подразделяют на жидкие и густые (консистентные), твердые и газообразные.
Основным смазочным материалом являются жидкие масла, которые хорошо распределяются по сопрягаемым поверхностям, обладают малым внутренним трением и хорошо работают в значительном диапазоне температур.
Консистентные смазки применяют в подшипниках скольжения в тех случаях, когда требуется надежная герметизация подшипникового узла.
Твердые смазочные материалы используют для смазывания подшипниковых узлов с подшипниками скольжения, работающими при больших температурах.
Воздушную смазку применяют в подшипниковых узлах с подшипниками скольжения быстроходных и мало нагруженных валов.
Для равномерного распределения смазки по всей поверхности сопряжения во вкладышах подшипников скольжения делают канавки, которые обычно размещают в мало нагруженной части подшипника. Если подшипник в процессе работы испытывает большие нагрузки, то помимо смазочных канавок выполняют еще и смазочные карманы (специальные углубления, в которых размещается запас смазки). Наличие в подшипнике скольжения смазочного кармана способствует попаданию смазки по смазочным канавкам в наиболее нагруженные места. Длина смазочных канавок в целях предотвращения вытекания масла из подшипника скольжения не должна превышать 0,8 длины его рабочей поверхности.
Сборка неразъемных подшипников скольжения.
Перед началом сборки неразъемного подшипника скольжения необходимо проверить соответствие геометрических размеров и формы посадочных мест на валу и во втулке требованиям чертежа. Контроль геометрических размеров и формы посадочных мест осуществляется универсальными (микрометр, микрометрический нутромер) или специальными (калибр-скобы и калибр-пробки) измерительными инструментами. После проверки посадочных размеров производят запрессовку втулки в корпус. Поскольку размер отверстия во втулке вследствие пластического деформирования в процессе запрессовки уменьшается, то после установки втулки в корпус необходимо восстановить номинальный размер ее отверстия развертыванием или растачиванием. В связи с тем что в процессе возникновения нагрузок в ходе эксплуатации подшипникового узла с подшипником скольжения возможно проворачивание втулки в корпусе, необходимо предупредить такую возможность, осуществив ее стопорение от возможного проворачивания.
Запрессовка втулки в корпус может быть осуществлена молотком с использованием специальных оправок, на прессе (ручном винтовом или стационарном) или методом глубокого охлаждения (применяют, как правило, при установке тонкостенных втулок в корпус большой массы).
При запрессовке втулок в корпус неразъемного подшипника скольжения весьма важно обеспечить соосность втулки и отверстия в корпусе, для чего рекомендуется применять приспособления, обеспечивающие центрирование втулки относительно оси отверстия в корпусе (рис. 1).
Втулку 1 надевают на оправку 2, которая центрируется в стойке 3. При приложении усилия оправка 2 перемещается вместе со втулкой, которая запрессовывается в отверстие корпуса 4.
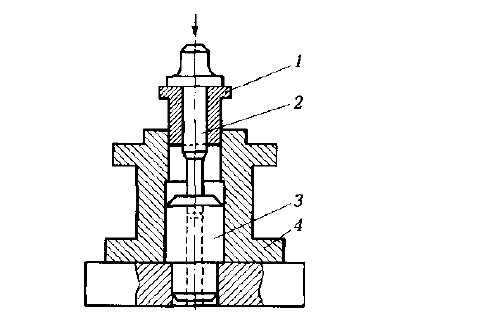
1 — втулка; 2 — оправка; 3 — стойка; 4 — корпус
Для лучшего направления втулки в отверстие на направляющей поверхности должны быть предусмотрены фаски или направляющие пояски. Если посадка втулки в корпус осуществляется с большим натягом, то для уменьшения сил трения при запрессовке применяют машинное масло.
Механизировать процесс запрессовки втулок в корпус можно, используя специальную установку (рис. 2). Эта стационарная установка монтируется на основании 12 и состоит из насосной станции 11, подъемника 9 с консольной стрелой 7, механизма подъема 8 и двух сменных силовых цилиндров. Силовой цилиндр 5 подключают к насосной станции гибким шлангом 6 и устанавливают по оси отверстия корпусной детали, используя с этой целью механизм подъема 8. С помощью кулачков 13 цилиндр центрируют по отверстию, используя кольцевые риски планшайбы 3. Втулку, подлежащую запрессовке, устанавливают на штоке 2 силового цилиндра и фиксируют ее положение при помощи закладной чеки 1 и гайки. После включения с кнопочного пульта 4 силового цилиндра 5 происходит запрессовка втулки. Для подключения установки к централизованной сети подачи сжатого воздуха служит кран 10.
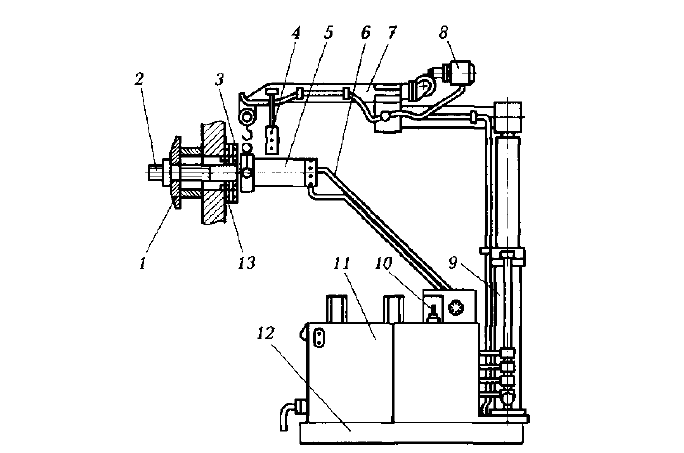
1 — чека; 2 — шток цилиндра; 3 — планшайба; 4 — кнопочный пульт; 5 — силовой гидравлический цилиндр; 6 — гибкий шланг; 7 — стрела; 8 — механизм подъема; 9 — подъемник; 10 — кран управления; 11 — насосная станция; 13 — основание; 13 — кулачок
Запрессовку втулок в корпус неразъемного подшипника скольжения можно совместить с последующей сборочной операцией — восстановлением номинальных размеров и формы отверстия во втулке. Для этого рекомендуется использовать специальное приспособление (рис. 3). На запрессовываемую в корпус 1 втулку 2 устанавливают прессующий элемент устройства — корпус 5 с гильзой 3, в окнах которой расположены шарики 4, при этом хвостовик протяжки 6, проходя через отверстия втулки и корпуса, соединяется тягой 9 с захватным устройством протяжного станка. При сообщении протяжке осевого усилия ее коническая часть упирается в шарики, вызывая перемещение гильзы 3 до тех пор, пока гайка 8, установленная в корпусе 5 приспособления, не упрется в корпус 1 базовой детали, вызвав относительное перемещение гильзы 3 в крайнее нижнее положение. При таком перемещении гильзы 3 шарики попадают в выточку в корпусе 5 приспособления, обеспечивая свободное перемещение протяжки вниз и обработку отверстия в запрессованной втулке до номинального размера. Момент окончания запрессовки определяется положением гайки 8 на корпусе 5 приспособления, которое фиксируется контргайкой 7.
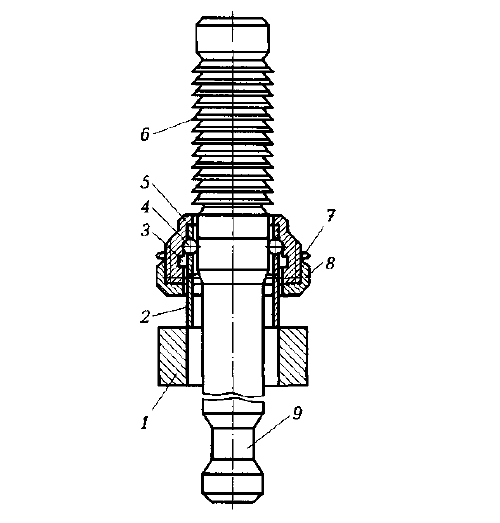
После установки втулки в корпус с необходимым натягом следует принять меры по предотвращению ее проворачивания в процессе работы механизма. С этой целью втулку дополнительно закрепляют в корпусе с помощью винтов или штифтов, которые устанавливают или по торцевым поверхностям, или по поверхностям сопряжения (рис. 4).
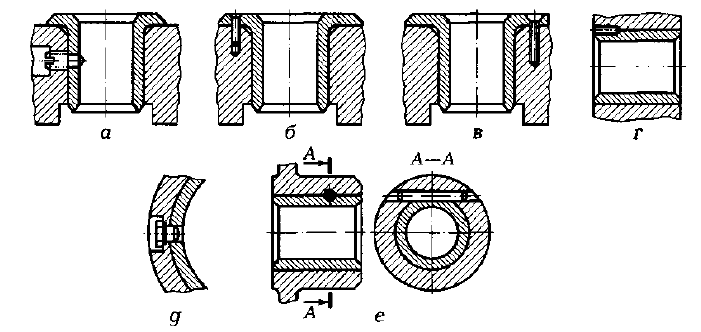
а — резьбовым стопором; б, в — штифтом и винтом по отверстию в буртике; г — резьбовым штифтом; д — гладким стопором; е — штифтом по касательной
Подготовка отверстий под винты или штифты производится после запрессовки втулки в отверстие корпуса, т, е. по месту, и зависит от выбранного способа стопорения: при закреплении втулки стопорным винтом во втулке сверлят сквозное отверстие (рис. 4, а); при стопорении штифтом по отверстию в буртике втулки сверлят отверстие в корпусе, а штифт устанавливают с натягом, накернивая его (рис. 4, б); при закреплении втулки винтом по отверстию в буртике (рис. 4, в) сверлят отверстие в корпусе под резьбу, используя отверстие в буртике в качестве кондуктора, затем рассверливают отверстие в буртике и зенкуют его под головку установочного винта; при стопорении втулки в корпусе винтом или штифтом вдоль образующей или перпендикулярно ей (рис. 4, г, е) отверстие сверлят в корпусе и втулке одновременно таким образом, чтобы его ось совпадала с образующей втулки по ее наружному диаметру; при креплении втулки гладким стопором он удерживается в отверстии за счет посадки (рис. 4, д), поэтому отверстие в этом случае сначала сверлят, а затем развертывают.
При реализации всех описанных методов стопорящие детали не должны выступать из корпуса, а должны быть утоплены не менее чем на 0,3 мм.
Для обеспечения нормальной работы неразъемного подшипника скольжения необходимо тщательно проверить состояние его рабочей поверхности, так как наличие перекоса или повреждения рабочей части втулки ведет к неравномерному распределению масляного слоя и появлению местного сухого трения, результатом чего является неравномерная работа вала и его быстрое изнашивание.
От правильной установки подшипников зависит работа всего механизма в целом, поэтому основным требованием при сборке подшипниковых узлов с неразъемными подшипниками скольжения является обеспечение соосности всех подшипниковых опор, в которых будет установлен вал.
Если в механизме устанавливают несколько валов, то помимо соосности подшипников каждого вала необходимо обеспечить параллельность и перпендикулярность всех осей подшипников многоопорных валов.
Конструкция и сборка разъемных подшипников скольжения.
Разъемные подшипники скольжения состоят из корпуса и крышки, внутри которых установлены вкладыши из чугуна, бронзы или биметаллические.
Вкладыши могут быть тонкостенными, толстостенными и с нормальной толщиной стенки. Причем критерием отнесения вкладышей к тому или иному типу является не абсолютная толщина его стенки, а ее отношение к наружному диаметру вкладыша. Если это отношение более 0,065, вкладыш считают толстостенным, если менее 0,045 — тонкостенным. В том случае если это отношение находится в интервале между приведенными значениями, толщина стенки вкладыша считается нормальной.
При сборке разъемных подшипников скольжения тонкостенные вкладыши подбирают по гнездам в корпусе и крышке на прилегание «на краску» и устанавливают их с натягом. Плотность прилегания вкладыша к гнезду корпуса и крышки достигается за счет его пластического деформирования. После установки валов в подшипниковые опоры осуществляют приработку вкладыша к сопрягаемой поверхности вала, для чего в зазор подается смазка. Приработка начинается с малых частот вращения, которые постепенно доводят до номинального значения. В процессе приработки уменьшаются и сглаживаются микронеровности, а также упрочняется поверхность вкладыша. В процессе приработки необходимо следить за температурой подшипника, которая не должна превышать 60 °C.
Превышение температуры подшипника в процессе приработки свидетельствует о некачественной сборке или пригонке деталей узла или о неудовлетворительном поступлении смазки в зону трения. В этом случае приработку следует приостановить, определить наличие дефектов сборки или пригонки и устранить их.
Толстостенные вкладыши обычно изготавливают из низкоуглеродистой стали, чугуна или бронзы и заливают баббитом. Толщину слоя баббита выбирают в пределах до 0,01 внутреннего диаметра вкладыша, но в любом случае она не должна превышать 2 мм.
Марку баббита для заливки толстостенного вкладыша выбирают в зависимости от режима работы подшипника и его назначения (табл. 1).
Сборка разъемных подшипников скольжения связана с выполнением пригоночных работ, которые ведут в два этапа — пригонка вкладыша к гнездам корпуса и крышки подшипника и пригонка посадочного места вкладыша по шейке вала.
Выполняется пригонка методом шабрения с контролем по пятну контакта «на краску», при этом число пятен контакта должно составлять не менее 5 на 1 см2, располагаясь равномерно не менее чем на 75 % площади поверхности вкладыша.
Окончательно пригонка вкладыша осуществляется при установленной на корпус крышке.
Для определения мест, которые необходимо пришабрить, производят последовательно затягивание и отпускание гаек, крепящих крышку подшипника к корпусу всех подшипниковых опор, тарированным ключом с заданным усилием и проворачивают вал на 2 — 3 оборота. После этого производят окончательное пришабривание верхней и нижней половин вкладышей по следам, которые остались после проворачивания вала.
Таблица 1. Технические характеристики баббитов и их назначение
Марка | Характеристика нагрузки | Давление, МПа | Окружная скорость, м/с | Область применения |
Б88 | Спокойная Ударная | 20 15 | 50 50 | При больших скоростях и высоких динамических нагрузках |
Б83 | Спокойная | 15 | 50 | При больших скоростях и средних нагрузках |
Б83С | Ударная | 15 | 50 | Тоже |
БН | Спокойная Ударная | 10 7,6 | 30 30 | При средних скоростях и средних нагрузках |
Б16 | Спокойная | 10 | 30 | В подшипниках, работающих без изменения нагрузки |
БС6 | Ударная | 15 | — | В подшипниках автотракторных двигателей |
Радиальные зазоры между валом и стенкой вкладыша проверяют, проворачивая вал при установленных между ним и верхней половиной вкладыша калиброванных латунных пластинах. Если по условиям работы требуются большие зазоры, их размер определяют при проворачивании вала по степени деформации свинцовой проволоки, установленной между шейкой вала и вкладышем. Для регулирования радиального зазора в разъемных подшипниках скольжения предусмотрена установка прокладок между корпусом и крышкой, которые представляют собой набор пластин толщиной 0,05… 0,8 мм. Осевые зазоры в узлах с разъемными подшипниками скольжения, которые должны находится в пределах 0,1…0,8 мм, проверяют щупом или индикатором при предельных осевых перемещениях вала.
О качестве сборки подшипникового узла можно судить по характеру вращения вала. Если вал вращается с трудом, это указывает на заниженные зазоры между шейкой вала и вкладышем.
Зазор между шейкой вала и вкладышем должен быть определенной величины, которая составляет примерно 0,001D + 0,05 мм, где D — диаметр шейки вала. Величину зазора между шейкой вала и вкладышем определяют при помощи шаблона, представляющего собой набор калиброванных латунных пластин, последовательно устанавливаемых в зазор. При установке в зазоре пластин, размер которых соответствует по величине его минимальному значению, вал должен легко проворачиваться. Когда величина устанавливаемых в зазор пластин соответствует его максимальному значению, вал должен заклиниваться.
Сборка подшипника жидкостного трения.
Сборка подшипников жидкостного трения, которые представляют собой разновидность подшипников скольжения — операция весьма ответственная и должна осуществляться в специальном помещении. После проверки качества изготовления всех комплектующих деталей на соответствие требованиям чертежа и технических условий на сборку их промывают в масле и бензине, сушат и покрывают тонким слоем специального масла.
Подшипник жидкостного трения (рис. 5) состоит из двух основных деталей: конической массивной втулки 9 и вкладыша 8 с тонким слоем баббитовой заливки. Смазочный материал поступает к сопрягаемым деталям подшипника через отверстие 7 и отводится через отверстие 12. При эксплуатации подшипника смазка захватывается втулкой 9, установленной на шейке вала и вращающейся во вкладыше 8, и направляет в клиновой зазор между этими втулками. Осевые усилия передаются через кольцо 5 (закрытое крышкой 4) на упорное кольцо 6. Втулка 9 крепится на валу шпонкой 11 и кольцом 1, которое навинчивается на кольцо 2, состоящее из двух половин. Кольцо 2 вставляется в кольцевой паз и фиксируется штифтом 3. Для предохранения подшипника от загрязнения устанавливают уплотнительные кольца 10. Подушку 15 подшипника фиксируют в станине 14 приливом 16 и эксцентриком 13, который поворачивается валиком 17, приводимым в движение от рукоятки 18.
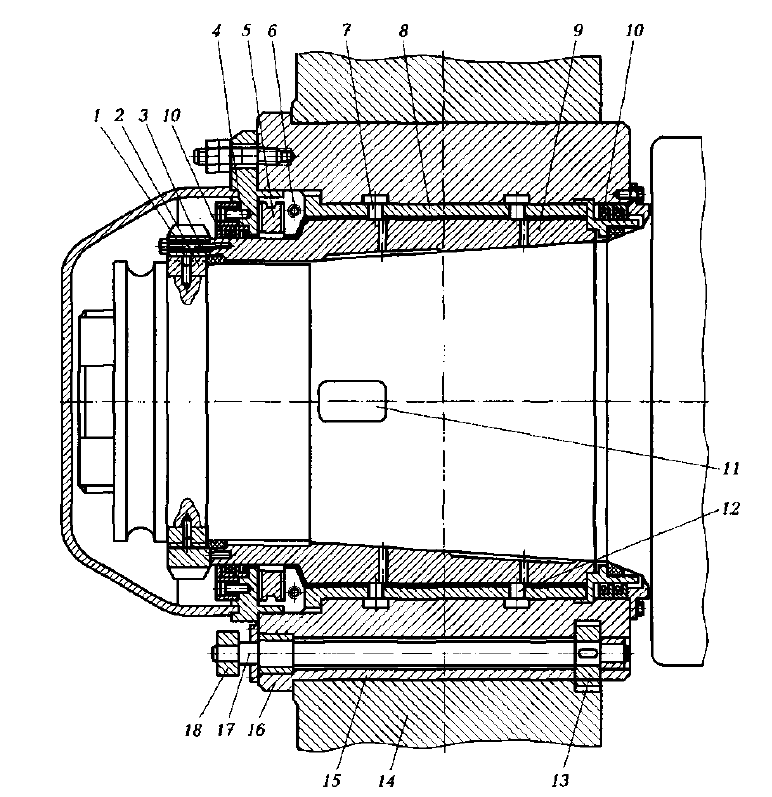
1, 2, 5, 6, 10 — кольца; 3 — штифт; 4 — крышка; 7, 12 — отверстия для подвода и отвода масла; 8 — вкладыш; 9 — коническая втулка; 11 — шпонка; 13 — эксцентрик; 14 — станина; 15 — подушка; 16 — прилив; 17 — валик; 18 — рукоятка
Сборку подшипника жидкостного трения (рис. 6) начинают с того, что подушку 2 располагают на стеллаже в вертикальном положении и запрессовывают в нее штифт 3. Затем устанавливают в подушку 2 втулку-вкладыш 1 таким образом, чтобы паз на буртике втулки-цапфы 5 совместился со штифтом 3. После этого в подушку устанавливают втулку-цапфу 5 с полукольцами 4, используя при этом технологическую шайбу 6. Далее устанавливают упорное кольцо 9, навинчивая гайку 8 до упора, а затем гайку отпускают, обеспечивая осевой зазор. На заключительном этапе сборки устанавливают крышку 10 с запрессованным в нее штифтом 7 так, чтобы штифт вошел в отверстие гайки 8, обеспечивая ее фиксирование от самопроизвольного отвинчивания. Собранный узел поворачивают на 180° и крепят к задней крышке 11. После этого собранный подшипник устанавливают на вал (см. рис. 5), предварительно поместив в его паз шпонку 11, а в кольцевую выточку — резьбовое кольцо 2, положение которого зафиксировано штифтом 3. После установки подшипника проверяют равномерность прилегания уплотнительного кольца 10 и производят пробное прокручивание вала в подшипниках.
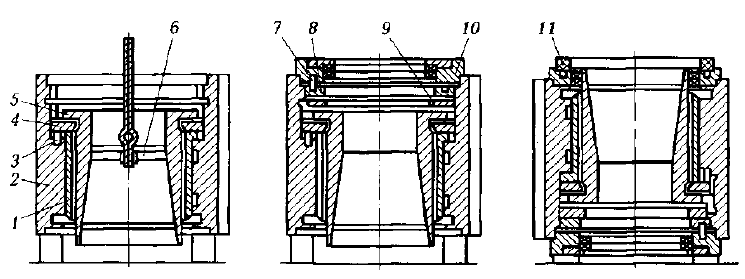
1 — втулка-вкладыш; 2 — подушка; 3.7 — штифты; 4 — полукольцо; 5 — втулка-цапфа; 6 — технологическая шайба; 8 — гайка; 9 — упорное кольцо; 10, 11 — крышки
Контроль качества сборки подшипниковых узлов.
Основным критерием работоспособности подшипника скольжения является правильная установка подшипниковых опор, обеспечивающая их соосность. С этой целью при монтаже подшипниковых опор во время их предварительной установки применяют контрольный или макетный вал, относительно которого производится установка подшипниковых опор. Соосность подшипниковых опор можно проверить несколькими способами: эталонным валом; линейкой и щупом; струной и микрометрическим нутромером; оптическим методом.
Наиболее простой является проверка соосности при помощи эталонного вала, который при установке в подшипниковые опоры должен свободно проходить через все отверстия опор.
При контроле линейкой и щупом линейку прикладывают к стенкам вкладышей, а щупом контролируют зазор между линейкой и вкладышем каждой из опор (этим способом может быть проверена соосность подшипниковых опор, находящихся на расстоянии, не превышающем 2 м.
Контроль соосности подшипниковых опор, к которым не предъявляют высоких требований, осуществляют при помощи натянутой струны, которая служит геометрической осью проверяемых опор, и нутромера. Этот способ может быть использован как при вертикальном, так и при горизонтальном расположении подшипниковых опор.
Наибольшей точности контроля соосности подшипниковых опор удается добиться при использовании оптических методов с применением специальных приборов — телескопа и коллиматора.
Для контроля точности сборки отдельно стоящих подшипниковых опор применяют метод измерения нагрузок под каждой из опор при помощи динамометров, которые устанавливают в лапах опор, и по их показаниям регулируют положение осей. Этот метод применяют при контроле крупногабаритных подшипников.