Сверление — операция по образованию сквозных и глухих отверстий в сплошном материале, выполняемая при помощи режущего инструмента — сверла. Сверление может осуществляться ручными пневматическими и электрическими машинами и на сверлильных станках.
Ручные сверлильные устройства применяют при необходимости получения отверстий диаметром до 12 мм в материалах небольшой твердости (пластические массы, цветные металлы и сплавы, конструкционные стали).
Для обработки отверстий большого диаметра, повышения производительности труда и качества обработанной поверхности используют настольные и стационарные (вертикально- и радиальносверлильные) станки.
Рассверливание является разновидностью сверления и применяется для увеличения диаметра ранее просверленного отверстия. В качестве инструмента, так же, как и для сверления, применяют сверло. Не рекомендуется рассверливать отверстия, полученные в заготовках методами литья, ковки или штамповки.
Обработка отверстий методами сверления и рассверливания позволяет получить точность размеров до 10-го квалитета и шероховатость обработанной поверхности до Rz 80 мкм.
Сверла применяют при обработке отверстий в сплошном материале и рассверливании предварительно обработанных отверстий. Классифицируют сверла в зависимости от их конструкции: спиральные, центровые, перовые, ружейные и кольцевые (трепанирующие головки). Выбор конструкции сверла зависит от характера выполняемых работ и от диаметра обрабатываемого отверстия и его глубины.
Спиральные сверла (рис. 1, а) изготавливают с цилиндрической (диаметром до 20 мм) и конической (диаметром свыше 5 мм) хвостовой частью. Сверла с коническим хвостовиком имеют лапку, которая облегчает извлечение сверла из шпинделя станка или переходной втулки.
Центровочные сверла (рис. 1, б) предназначены для выполнения центровых отверстий в торцевой поверхности заготовок, подлежащих токарной обработке.
Перовые сверла (рис. 1, в) применяют для обработки металлов низкой твердости, например баббитов, и неметаллических материалов.
Ружейные сверла (рис. 1, г) применяют для сверления глубоких и сверхглубоких отверстий диаметром 3…30 мм с соотношением глубины сверления к диаметру отверстия более 5.
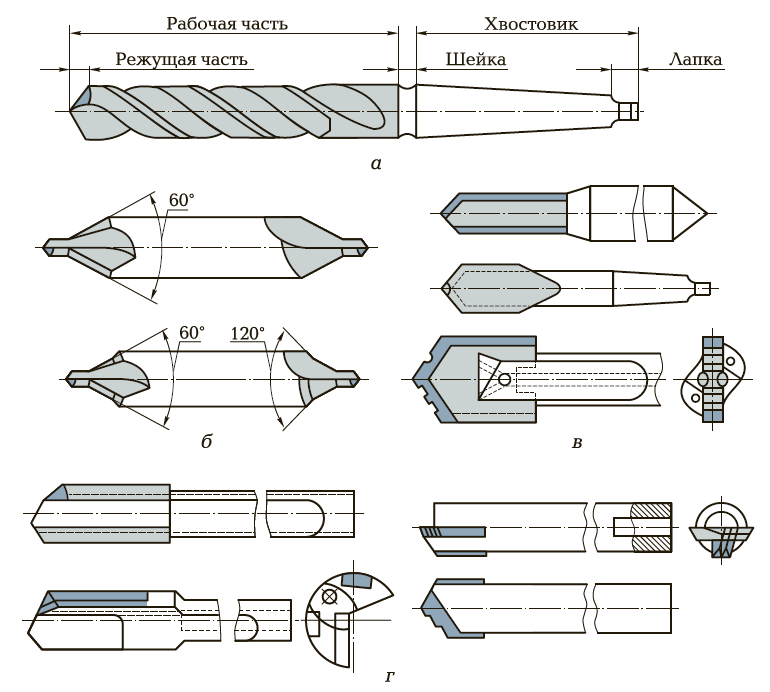
а — спиральные; б — центровочные; в — перовые; г — ружейные для глубокого сверления
Кольцевые сверла (рис.2) применяют при обработке в сплошном материале отверстий диаметром более 50 мм.
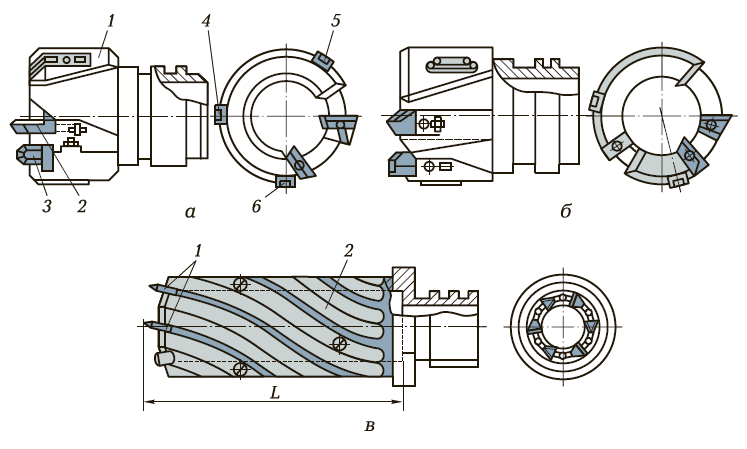
а — двурезцовые: 1 — корпус; 2, 3 — сменные резцы; 4 — 6 — направляющие пластины; б — трехрезцовые; в — многорезцовые: 1 — резцы; 2 — корпус; L — длина рабочей части
В процессе эксплуатации происходит износ рабочей (режущей) части сверл, что приводит к потере их режущей способности.
Поскольку в процессе выполнения слесарных и слесарно-сборочных работ наиболее часто применяют спиральные сверла, остановимся именно на их эксплуатации.
Износ спиральных сверл происходит преимущественно по задней поверхности на пересечении режущих кромок с ленточками (рис. 3). Восстановить режущие свойства сверла можно за счет его заточки.
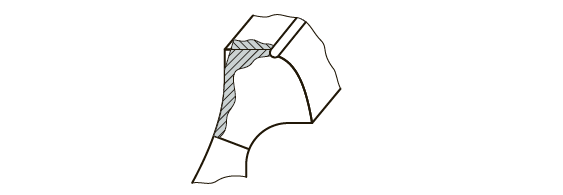
Заточка спиральных сверл позволяет восстановить режущие свойства сверла. При заточке режущей части сверла придают различную форму, выбор которой зависит от характера выполняемых работ и обрабатываемого материала.
Одинарная заточка (рис. 4, а) применяется при сверлении отверстий диаметром до 12 мм в заготовках из стали или чугуна.
Одинарная заточка с подточкой перемычки (рис. 4, б) применяется при обработке отверстий диаметром 12…80 мм в заготовках из стального литья, покрытого коркой.
Одинарная заточка с подточкой перемычки и ленточки (рис. 4, в) применяется при обработке отверстий диаметром 12…80 мм в заготовках из стали и стального литья со снятой коркой.
Двойная заточка с подточкой перемычки (рис. 4, г) применяется при обработке отверстий диаметром 12…80 мм в заготовках из чугунного литья, покрытого коркой.
Двойная заточка с подточкой перемычки и ленточки (рис. 4, д) применяется при обработке отверстий диаметром 12…80 мм в заготовках из чугунного литья со снятой коркой.
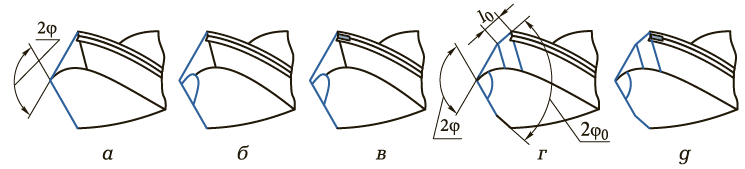
а — одинарная; б — одинарная с подточкой перемычки; в — одинарная с подточкой перемычки и ленточки; г — двойная с подточкой перемычки; д — двойная с подточкой перемычки и ленточки;
2φ — угол при вершине; 2φ0 — угол дополнительной заточки; l0— ширина дополнительной заточки
При обработке отверстий с применением ручного и стационарного оборудования применяют специальные приспособления для установки инструментов и заготовок.
Приспособления для установки инструментов служат для их соединения с устройствами, передающими вращательное движение инструменту.
Сверлильные патроны служат для установки инструмента с цилиндрической хвостовой частью. Сверлильные патроны изготавливают различных конструкций: кулачковые, цанговые и др.
Трехкулачковый сверлильный патрон (рис. 5, а) обеспечивает достаточно высокую точность центрирования инструмента относительно оси обрабатываемого отверстия.
Двухкулачковый сверлильный патрон аналогичен по конструкции трехкулачковому, однако точность центрирования обрабатывающего инструмента относительно оси отверстия у него менее точная.
Цанговый сверлильный патрон (рис. 5, б) предназначен для закрепления сверл с цилиндрическим хвостовиком небольшого диаметра и обеспечивает очень высокую точность центрирования обрабатывающего инструмента относительно оси отверстия.
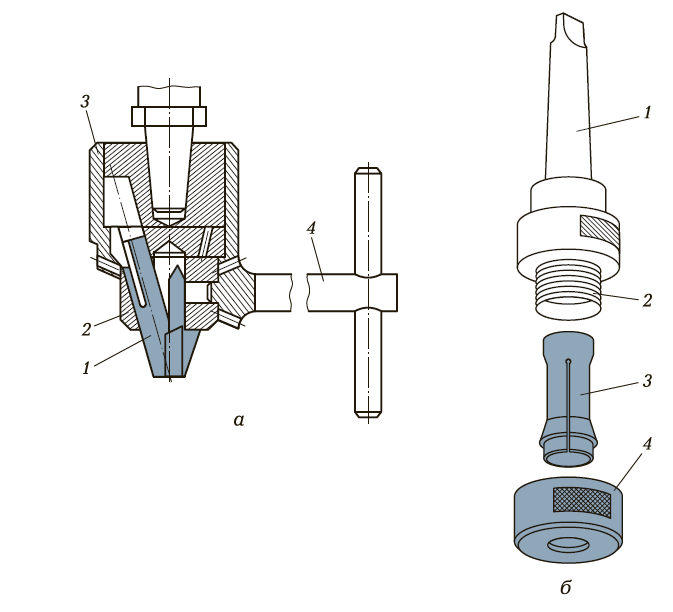
а — трехкулачковый сверлильный патрон: 1 — кулачок; 2 — гайка; 3 — обойма; 4 — ключ; б — цанговый сверлильный патрон: 1 — хвостовик; 2 — цилиндрическая часть; 3 — разрезная цанга; 4 — кольцо
Приспособления для установки заготовок служат для правильной установки и закрепления заготовок на столе станка. Выбор приспособлений в значительной степени зависит от того, какое оборудование применяют при обработке отверстий. Наиболее часто для закрепления заготовок применяют прихваты, призмы, угольники, машинные тиски различных конструкций, кондукторы и т.д.
Прихваты (рис. 6, а) и призмы (рис. 6, б) применяют для закрепления заготовок с плоскими и цилиндрическими поверхностями.
Жесткая (рис. 6, в) и регулируемая (рис. 6, г) угловые плиты предназначены для установки и закрепления на столе станка заготовок разной, иногда достаточно сложной формы, например рычагов.
Винтовые (рис. 6, д) и быстродействующие (рис. 6, е) машинные тиски применяют при обработке заготовок сложной формы.
Кондукторы обеспечивают правильное расположение режущего инструмента относительно обрабатываемого отверстия. Применение кондукторов экономически обосновано только в условиях серийного и массового производства.
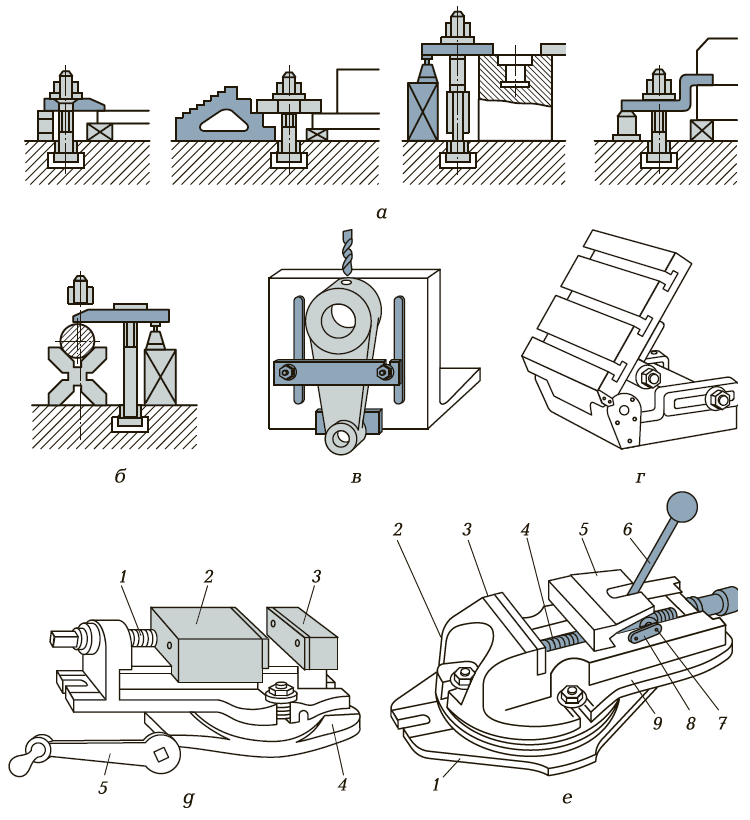
а — прихваты; б — призма; в — жесткая угловая плита; г — регулируемая угловая плита; д — винтовые машинные тиски: 1 — ходовой винт; 2 — подвижная губка; 3 — неподвижная губка; 4 — основание; 5 — рукоятка; е — быстродействующие машинные тиски: 1 — заготовка; 2 — поворотная часть; 3 — неподвижная губка; 4 — установочный винт; 5 — подвижная губка; 6 — рукоятка; 7 — эксцентриковый вал; 8 — двойной кулачок; 9 — основание
Оборудование для обработки отверстий подразделяют на ручное, ручное механизированное и стационарное.
Ручное оборудование — оборудование, в котором в качестве привода используется мускульная энергия человека. К этому оборудованию относятся ручные дрели и трещотки.
ручная дрель предназначена для сверления отверстий вручную.
Трещотка применяется в тех случаях, когда для обработки отверстия невозможно использование ручной дрели и сверлильного станка.
Ручное механизированное оборудование может иметь как электрический, так и пневматический привод и отличается большим разнообразием конструктивных решений. Выбор конструкции ручного механизированного оборудования зависит от характера и условий выполнения работ.
Электрические дрели применяют для сверления отверстий диаметром до 10 мм (легкий тип), 15 мм (средний тип) и 32 мм (тяжелый тип).
Пневматические дрели изготавливают в двух вариантах: легкого и тяжелого типа.
Стационарное оборудование устанавливается на постоянном месте, при этом обрабатываемую заготовку доставляют к нему. К этому виду оборудования относят настольные, вертикальные и радиальные сверлильные станки.
Настольные сверлильные станки (рис. 7) отличаются большим разнообразием конструкций и обеспечивают получение отверстий диаметром до 25 мм.
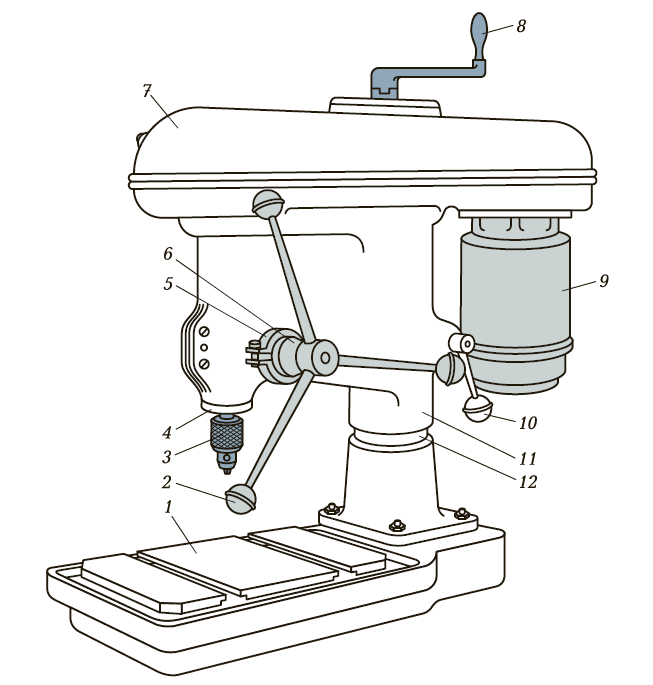
1 — стол; 2, 8, 10 — рукоятки; 3 — трехкулачковый патрон; 4 — шпиндель; 5 — хомутик; 6 — лимб; 7 — кожух; 9 — электрический двигатель; 11 — корпус; 12 — колонна
Вертикально-сверлильный станок (рис. 8) — основной и наиболее распространенный тип сверлильных станков, применяемых для обработки отверстий в заготовках сравнительно небольшого размера. На вертикально-сверлильных станках возможно выполнение сверления, зенкерования, зенкования, цекования и развертывания. На вертикально-сверлильных станках выполняют обработку отверстий диаметром до 50 мм.
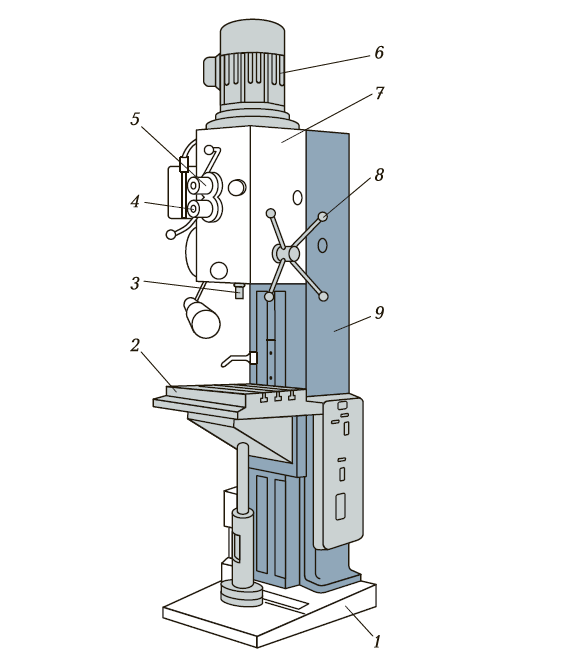
1 — фундаментная плита; 2 — стол; 3 — шпиндель; 4 — коробка подач; 5 — коробка скоростей; 6 — электрический двигатель; 7 — сверлильная головка; 8 — рукоятка; 9 — колонна
Радиально-сверлильные станки (рис. 9) обладают теми же технологическими возможностями, что и вертикально-сверлильные. Их отличительная особенность состоит в том, что шпиндельная головка станка может перемещаться относительно обрабатываемой заготовки в разных направлениях, обеспечивая обработку крупногабаритных заготовок без их переустановки, а следовательно, и без повторной выверки, относительно режущего инструмента.
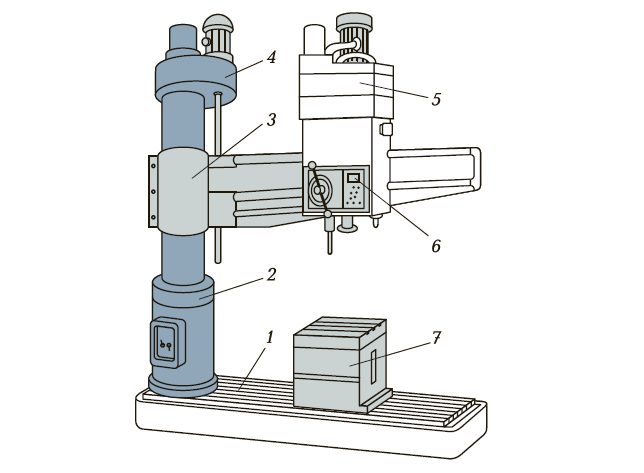
Рис. 9. Радиально-сверлильный станок:
1 — фундаментная плита; 2 — цоколь; 3 — рукав; 4 — механизм подъема; 5 — шпиндельная головка; 6 — пульт управления; 7 — стол
Расчет режимов резания осуществляется в следующей последовательности:
- выбирают по справочным таблицам величину подачи в зависимости от характера обработки, требований к качеству обработанной поверхности, материала сверла и других технологических данных;
- определяют по справочным таблицам скорость инструмента с учетом технологических возможностей станка, режущих свойств материала инструмента и физико-механических свойств материала заготовки;
- рассчитывают частоту вращения шпинделя в соответствии с выбранной скоростью резания. Полученную величину сравнивают с паспортными данными станка и принимают равной ближайшему наименьшему значению этой частоты;
- рассчитывают действительную скорость резания, с которой будет производиться обработка.