Трубопроводные системы применяют в силовых установках (для подвода воды и топлива), станках и в другом технологическом оборудовании (для подвода масла к местам смазки и зажимным устройствам и охлаждающей жидкости в зону обработки), в прессовом оборудовании (для подвода жидкостей и газов к силовым цилиндрам).
Трубопровод состоит из труб, соединяемых между собой и с конструктивными элементами оборудования при помощи специальных соединительных элементов, крепежных деталей и арматуры.
В зависимости от назначения различают трубопроводы высокого, среднего и низкого давления. Для всех видов трубопроводов общим требованием является чистота проходного отверстия, полная непроницаемость, долговечность и простота обслуживания.
В зависимости от назначения трубопроводной системы используют чугунные, стальные, медные, латунные, алюминиевые и пластиковые трубы. Наиболее распространено применение стальных труб. В зависимости от способа изготовления различают цельнотянутые (бесшовные) и сварные трубы.
Для передачи охлаждающей жидкости используют, как правило, обычные водопроводные трубы. Для передачи горячей воды и пара — бесшовные трубы, для рабочих жидкостей в системах гидравлического привода — стальные цельнотянутые трубы, для подвода смазывающих масел — медные трубы.
Соединения трубопроводов могут быть неподвижными разъемными и неподвижными неразъемными (однако в некоторых случаях используют подвижные соединения элементов трубопроводов). К неподвижным разъемным соединениям относятся соединения на резьбе, выполненные с помощью специальных соединительных элементов — фитингов и фланцев (рис. 1, а—ж), а к неподвижным неразъемным соединениям относятся соединения, выполняемые сваркой, напрессовкой, отбортовкой и развальцовкой (рис. 1, з—к).
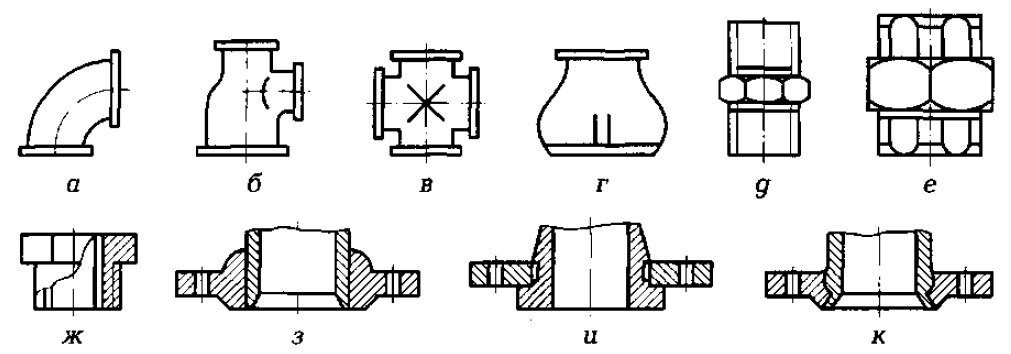
а — угольник; б — тройник; в — крестовидный переходник; г — переходная муфта; д, е — контргайка; ж — футорка; з—к — соединение с фланцем соответственно напрессовкой, развальцовкой, отбортовкой.
Все операции, выполняемые при сборке трубопроводных систем, могут быть подразделены на заготовительные и сборочные.
К заготовительным операциям относятся разметка, отрезка, очистка, гибка труб, отбортовка, развальцовка, сварка и сборка деталей в сборочные единицы, проверка и контроль по размерам, форме и внешнему виду, гидравлические испытания и маркировка.
Наиболее сложная операция — гибка труб, которая может производиться как вручную, так и механическим способом с наполнителем или без него. Наиболее важным является выбор радиуса гибки, так как он оказывает существенное влияние па работу трубопровода. Радиус гибки выбирают в зависимости от диаметра трубы и толщины ее стенки,
На сборочные операции сборочные единицы поступают в подготовленном виде, т.е. соответствующей длины и с нарезанной на концах трубы резьбой. Соединительные элементы, крепежные детали и арматура, поступающие на сборку, также должны быть окончательно подготовлены и проверены для монтажа в трубопроводной системе.
При сборке необходимо обеспечить соосность соединяемых груб, а также параллельность торцов труб и соединительных фланцев. Несоблюдение этих условий является причиной возникновения нагрузок, которые могут вывести трубопровод из строя.
В зависимости от назначения трубопроводных систем различаются технологические процессы их сборки.
Сборка трубопроводных систем на фитингах.
Стальные трубы, на концах которых нарезана резьба, соединяют между собой специальными соединительными элементами — фитингами, которые изготавливают стальными или из ковкого чугуна. Применение фитингов при сборке обеспечивает соединение труб под различными углами, предусматривает выполнение отведений и обеспечивает переход от одного диаметра трубы к другому.
Герметичность соединения при помощи фитингов достигается за счет смазывания резьбовой части соединяемых деталей перед сборкой свинцовым суриком или цинковыми белилами с предварительной подмоткой резьбы льняной или пеньковой пряжей.
Магистральные трубы, соединяемые при помощи прямых соединительных муфт, имеющих на наружной поверхности ребра для захвата их трубным ключом, могут иметь короткую или длинную резьбу.
При сборке труб с короткой резьбой (рис. 2, а) на конце трубы 2 нарезается резьба такой длины, чтобы она была на 2 — 3 витка меньше половины длины соединительной муфты 1. Сбег в конце резьбы при сборке заклинивает муфту, что обеспечивает плотность соединения. Соединения труб с короткой резьбой применяют только для неразъемных трубопроводов, так как после сборки такие соединения разъединить невозможно.
Сборка труб на сгоне (рис. 2, 6) производится, если по условиям работы трубопроводную систему необходимо разбирать. В этом случае одна из труб имеет короткую резьбу, а вторая длинную. Участок трубы с длинной резьбой называют сгоном. Длину этого участка выбирают таким образом, чтобы после установки на нем соединительной муфты и гайки остался участок резьбы не менее чем с двумя нитками. Соединения на сгоне можно применять только при сборке трубопроводов с цилиндрической резьбой.

а — с короткой резьбой; б — на сгоне; 1 — муфта; 2 — труба; 3 — контргайка
При помощи соединений на фитингах монтируют водяные, паровые и некоторые другие трубопроводы, работающие при давлении, не превышающем 16 МПа. Для соединения труб при помощифитингов применяют трубные ключи различных конструкций (рис. 3, а — д).
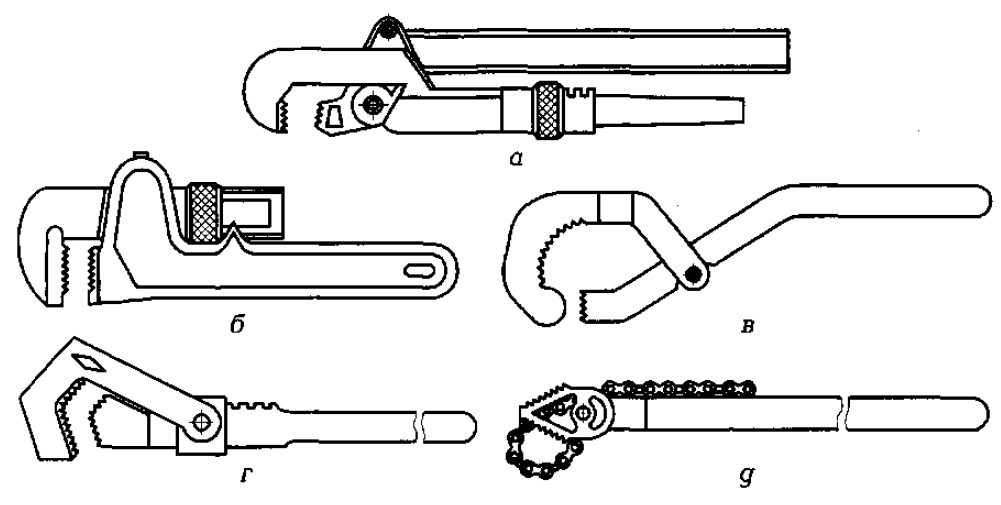
а — рычажный; б — разводной; в — специальный; г — накидной; д — цепной
Сборка трубопроводных систем на фланцах.
При сборке трубных соединений на фланцах их закрепляют на трубе сваркой, на резьбе, развальцовкой или отбортовкой (см. рис. 1, з—к). При этом необходимо обеспечить соосность трубопроводов и параллельность торцевых поверхностей фланцев. В процессе сборки между фланцами устанавливают прокладки, которые обеспечивают герметичность соединения. Фланцы крепят между собой, используя болты или шпильки. Прокладки вырезают так, чтобы они но форме соответствовали фланцу. Изготавливают прокладки из уплотняющего материала и промазывают с двух сторон герметизирующим составом (олифа, белила, специальные герметизирующие пасты — герметики). Соединения затягивают гайками, контролируя при этом параллельность торцевых поверхностей фланцев при помощи щупа.
В различных конструкциях трубопроводов широко применяют плоские уплотняющие прокладки. В зависимости от назначения различают прокладки:
- мягкие эластичные из однородного материала (картон, бумага, войлок, асбест, резина, паронит, свинец);
- мягкие эластичные комбинированные (металлические с асбестовой сердцевиной, асбестопрорезиненные);
- пасты и мастики.
От материала и толщины прокладки зависит надежность соединения.
Выбор того или иного прокладочного материала зависит от назначения трубопроводной системы.
Сборка трубопроводных систем развальцовкой.
При сборке труб развальцовкой (рис. 4) концы развальцованных труб 4 соединяют штуцером 1 и закрепляют при помощи гайки 2 и ниппеля 3. В некоторых случаях в этих соединениях используются медные прокладки, повышающие его герметичность.
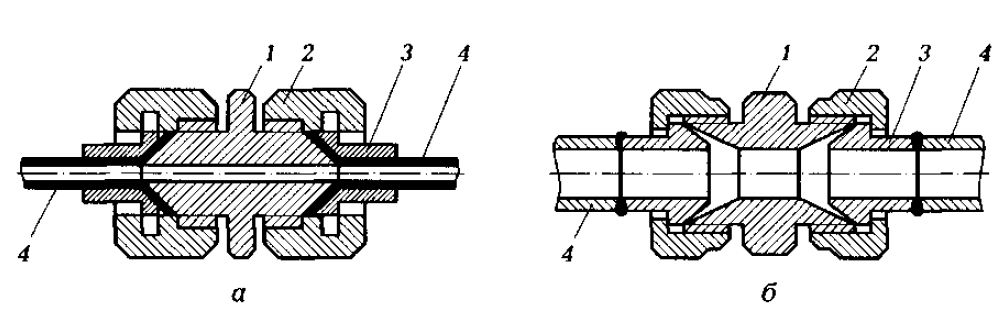
1 — штуцер; 2 — накидная гайка; 3 — ниппель; 4 — труба
Соединение трубопроводных систем с использованием клеев.
Для соединения труб в трубопроводных системах при помощи клеев применяют соединения бандажного типа, клеемеханические соединения, соединения муфтой и враструб (рис. 5).
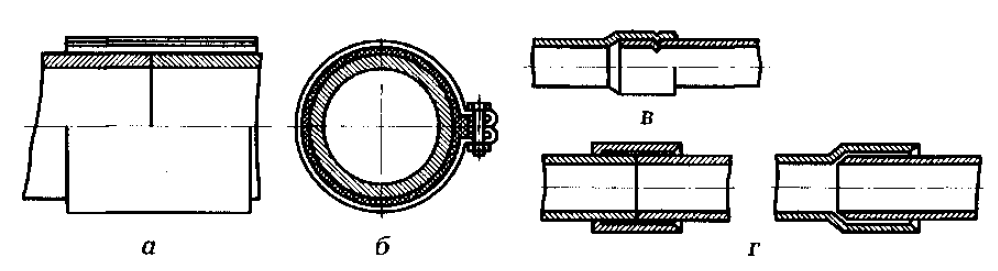
а, б — стыковое; в — клеемеханическое; г — муфтой и враструб
Клеевые соединения бандажного типа (рис. 5, а и б) выполняют путем многослойной намотки на концы стыка стальных труб ленты из стеклоткани с нанесенным на ее поверхность слоем эпоксидного клея. Фиксация взаимного положения концов стыкуемых труб обеспечивается за счет применения струбцин с призматическими поверхностями рабочей части. Зачистка труб перед склеиванием осуществляется на участках длиной не менее 0,7 диаметра трубы. Зачищенные поверхности перед склеиванием обезжиривают ацетоном или бензином. Намотка подготовленной ленты с нанесенным на нее клеевым составом на концы соединяемых груб осуществляется вручную, туго и без перекосов. Середина ленты при этом должна располагаться в месте стыка труб. Для получения необходимой прочности и герметичности соединение должно быть выдержано при температуре окружающего воздуха 5… 17 °C в течение четырех суток или при температуре 17…25°С в течение двух суток. Для сокращения времени выдержки и увеличения прочности клеевого соединения применяют искусственные условия, выдерживая соединение в течение трех часов при температуре 80 °С или в течение полутора часов при температуре 120 °С . Соединенные клеевым методом трубы можно перемещать только их переноской, категорически запрещается их перемещение волочением или сбрасывание с высоты.
Клеемеханическое соединение трубопроводов (рис. 5, в) выполняют, нанося клей на наружную поверхность конца трубы и внутреннюю поверхность раструба или муфты. После нанесения клея конец трубы вводится в раструб или в муфту и обжимается по периметру. После обжатия соединение выдерживается до полимеризации клея. Длина участка трубы, входящего в раструб или в муфту, должна составлять не менее 1,2 ее диаметра.
Соединения труб муфтой и враструб (рис. 5, г) отличаются от клеемеханических тем, что обжатие муфты или раструба не выполняется.
Сборка винипластовых трубопроводов. Сборка таких трубопроводов производится при помощи раструбов привариваемыми или резьбовыми муфтами, а также при помощи фланцев, закрепляемых сваркой или отбортовкой.
Соединения винипластовых труб при помощи раструбов могут быть неподвижными, выполняемыми при помощи сварки и клеев, или подвижными, выполненными с использованием резиновых колец. Подвижные соединения трубопроводов, выполненных из винипластовых труб, используют в целях компенсации температурного изменения длины трубопровода. Раструбные соединения для винипластовых труб выпускаются диаметром 8… 150 мм.
Соединение винипластовых труб сваркой встык не получило широкого распространения, так как прочность сварного шва для винипласта составляет всего 65…80% от прочности самого материала, что приводит при выполнении сварных соединений к появлению слабых (непрочных) мест в системе трубопровода. Изготовление раструбов и оттягивание бортов трубы из винипласта производится с предварительным нагревом. Нагрев осуществляют в ванне, наполненной глицерином или минеральным маслом, при температуре 150… 170°C. После нагрева трубу закрепляют в тисках, а в ее нагретую часть вводят стальную оправку соответствующего диаметра и формы, разогретую до температуры 100… 120 °C. Образующийся раструб охлаждают и после этого извлекают оправку из трубы. Длина раструба зависит от диаметра трубы.
Для склеивания винипластовых трубопроводов используют 20%-ный раствор перхлорвиниловой смолы в ацетоне или раствор дихлорэтана.
Сборка полиэтиленовых труб производится при помощи раструбов, муфт, металлических гаек сваркой или склеиванием. Прочность швов при стыковой сварке всего на 10% ниже прочности основного материала, что не приводит к существенному снижению прочности такого соединения.
Полиэтиленовые трубы склеивают после их обработки хромовой кислотой, что позволяет изменить полярность полиэтилена, в результате чего он приобретает способность склеиваться обычными клеями.
Для защиты от коррозии деталей, находящихся в контакте с полиэтиленом, нельзя использовать масляные краски и битумные лаки.
Трубопроводы после сборки испытывают на прочность и герметичность. При испытании трубопровод наполняют водой и отмечают те места, в которых наблюдается утечка жидкости. Затем воду выпускают и уплотняют отмеченные места. При гидравлических испытаниях трубопровода проверяют прочность всех его элементов и герметичность соединений под давлением, предусмотренным техническими условиями на сборку.