Сварные соединения.
По форме сопряжения соединяемых деталей различают следующие типы сварных соединений: стыковое, угловое, тавровое, нахлесточное и торцовое. Применяют также соединения нахлесточные с точечными или пробочными и прорезными швами, выполненными дуговой сваркой.
Стыковое соединение (рис. 1, а) представляет собой сварное соединение двух деталей, расположенных в одной плоскости и примыкающих друг к другу торцовыми поверхностями. Оно наиболее распространено в сварных конструкциях, поскольку имеет ряд преимуществ перед другими видами соединений.
Нахлесточное соединение представляет собой сварное соединение, в котором соединяемые элементы расположены параллельно и частично перекрывают друг друга (рис. 1, б).
Торцовое соединение — это соединение, в котором боковые поверхности элементов примыкают друг к другу (рис. 1, в).
Угловое соединение представляет собой сварное соединение двух элементов, расположенных под углом друг к другу и сваренных в месте примыкания их кромок (рис. 1, г).
Тавровое соединение (рис. 1, д) — это соединение, в котором к боковой поверхности одного элемента примыкает под углом и приварен торцом другой элемент. Как правило, угол между элементами прямой.
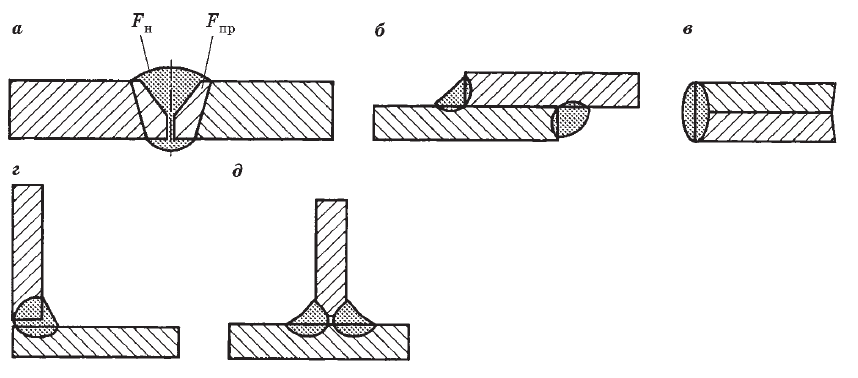
а — стыковое; б — нахлесточное; в — торцовое; г — угловое; д — тавровое
Сварные швы.
В зависимости от типов сварных соединений различают стыковые, угловые, точечные и прорезные сварные швы.
Стыковые швы выполняют при сварке стыковых соединений, угловые — при сварке угловых, тавровых и нахлесточных соединений, точечные и прорезные — в тавровых и нахлесточных соединениях.
По форме поперечного сечения сварные швы бывают стандартные, выпуклые и вогнутые (рис. 2).
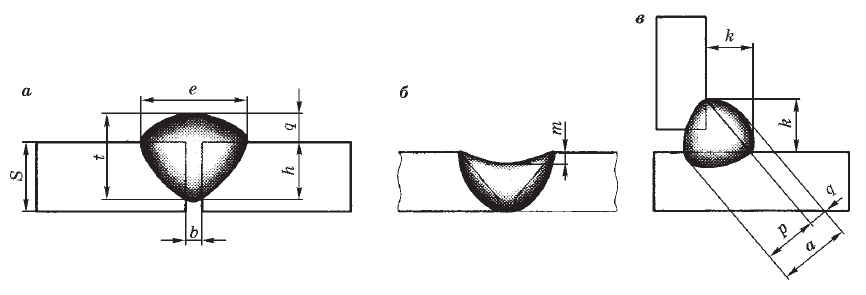
S — толщина детали; e — ширина; q — выпуклость (усиление); m — вогнутость (ослабление); h — глубина проплавления; t — толщина стыкового шва; b — зазор в стыке; k — катет углового шва; p — расчетная высота углового шва; a — толщина углового шва.
По числу слоев сварные швы могут быть однослойными и многослойными (рис. 3).
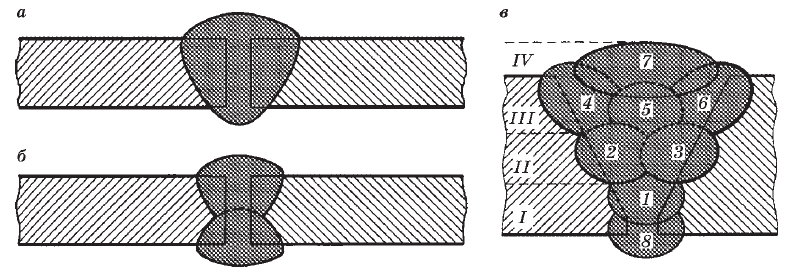
Слой — это часть металла сварного шва, которая состоит из одного или нескольких валиков, располагающихся на одном уровне поперечного сечения шва.
Валик — это металл шва, наплавленный или переплавленный за один проход.
Часть сварного шва, наиболее удаленную от его лицевой поверхности, называют корнем шва.
В зависимости от расположения швов в конструкции сварку выполняют в разных пространственных положениях, основными из которых являются: нижнее, горизонтальное, вертикальное и потолочное (рис. 4).

1 — нижнее; 2 — вертикальное или горизонтальное; 3 — потолочное.
По характеру выполнения различают одно- и двусторонние швы, выполняемые как на весу, так и на различного рода подкладках и флюсовых подушках.
Часть двустороннего шва, выполняемую предварительно для предотвращения прожогов при последующей сварке или накладываемую в последнюю очередь в корень шва для обеспечения высокого качества шва, называют подварочным швом.
По условиям работы швы подразделяют на рабочие, воспринимающие внешние нагрузки, и связующие (соединительные), предназначенные только для скрепления частей изделия и не рассчитанные на восприятие внешних нагрузок.
Изображения и обозначения швов сварных соединений на чертежах изделий должны соответствовать Единой системе конструкторской документации (ЕСКД). Независимо от вида сварки видимый шов сварного соединения условно изображают сплошной основной линией, а невидимый — штриховой. Обозначение шва отмечают линией-выноской, заканчивающейся односторонней стрелкой. Характеристика шва, расположенного на лицевой стороне листа (видимый шов), проставляется над полкой линии-выноски, а под полкой —для шва на обратной стороне листа (невидимый шов). Структура условного обозначения стандартного шва приведена на рисунке 5.
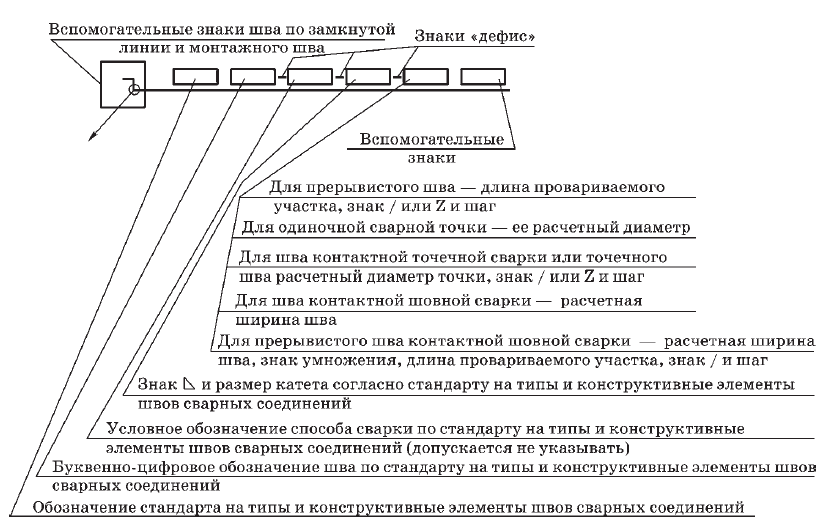
Ниже перечислены основные стандарты на виды и конструктивные элементы швов сварных соединений для различных видов сварки:
- ГОСТ 5264-80 «Ручная дуговая сварка. Соединения сварные»;
- ГОСТ 8713-79 «Сварка под флюсом. Соединения сварные»;
- ГОСТ 14771-76 «Дуговая сварка в защитном газе. Соединения сварные»;
- ГОСТ 15164-78 «Электрошлаковая сварка. Соединения сварные»;
- ГОСТ 14806-80 «Швы сварных соединений. Дуговая сварка алюминия и алюминиевых сплавов»;
- ГОСТ 16098-80 «Соединения сварные из двухслойной коррозионно-стойкой стали»;
- ГОСТ 16038-80 «Швы сварных соединений трубопроводов из меди и медно- никелевого сплава»;
- ГОСТ 11533-75 «Автоматическая и полуавтоматическая дуговая сварка под флюсом. Соединения сварные под острыми и тупыми углами»;
- ГОСТ 27580-88 «Дуговая сварка алюминия и алюминиевых сплавов. Соединения сварные под острыми и тупыми углами».
Этими стандартами в зависимости от толщины металла устанавливаются формы поперечного сечения сварного шва и размеры конструктивных элементов подготовленных кромок и выполненных швов, которым присваивают условные буквенно-цифровые обозначения.
Буквенная часть указывает на вид сварного соединения: С — стыковое; У — угловое; Т — тавровое; Н — нахлесточное. Цифры являются порядковым номером типа шва в данном конкретном стандарте.
Условные обозначения основных способов сварки следующие: Р — ручная дуговая сварка (штучным электродом); ЭЛ — электроннолучевая сварка; Ф — дуговая сварка под слоем флюса; ПЛ — плазменная и микроплазменная сварка; УП — сварка в активном газе (или смеси активного и инертного газов) плавящимся электродом; ИП — сварка в инертном газе плавящимся электродом; ИН — сварка в инертном газе неплавящимся электродом; Г — газовая сварка.
Сварные швы подразделяются также по положению в пространстве (рис. 6).
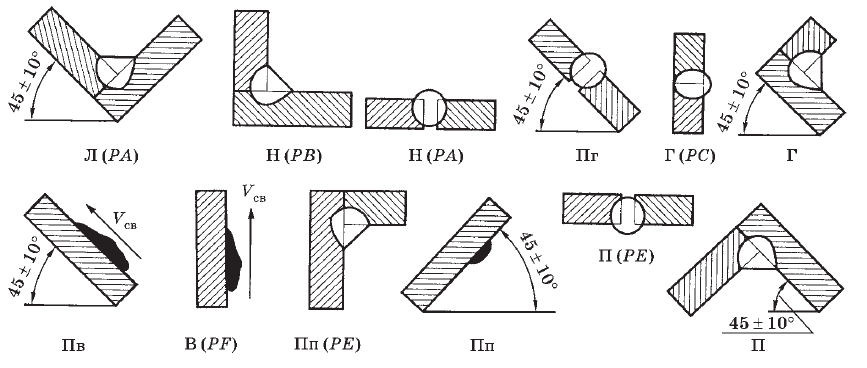
По протяженности различают швы непрерывные (сплошные) и прерывистые. Непрерывный шов — это сварной шов без промежутков по длине, прерывистый шов имеет промежутки по длине. Прерывистые швы могут быть цепными или шахматными (рис. 7, а).
По отношению к направлению действующих усилий швы подразделяют на: продольные, поперечные, комбинированные и косые (рис. 7, б).
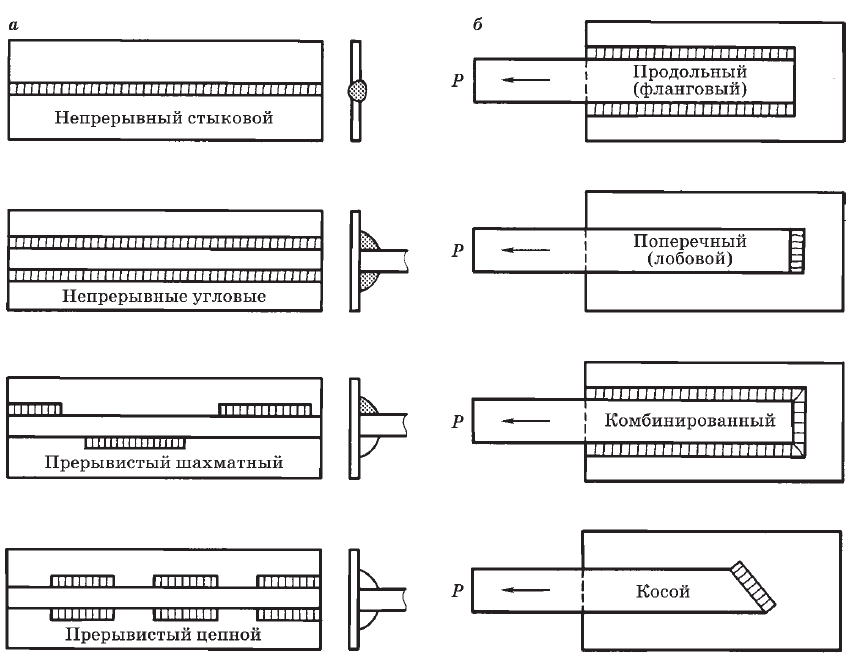
Для обозначения сварных швов используют также вспомогательные знаки (табл. 1). Все элементы условного обозначения располагаются в указанной последовательности и отделяются друг от друга дефисом. Буквенные обозначения способа сварки необходимо проставлять на чертеже только в случае применения в данном изделии нескольких видов сварки. Можно не указывать на полке мини-выноски обозначения стандарта, если все швы в изделии выполняются по одному стандарту. В этом случае следует сделать соответствующее указание в примечаниях на чертеже.

Примеры условного обозначения сварных швов приведены в таблице 2.
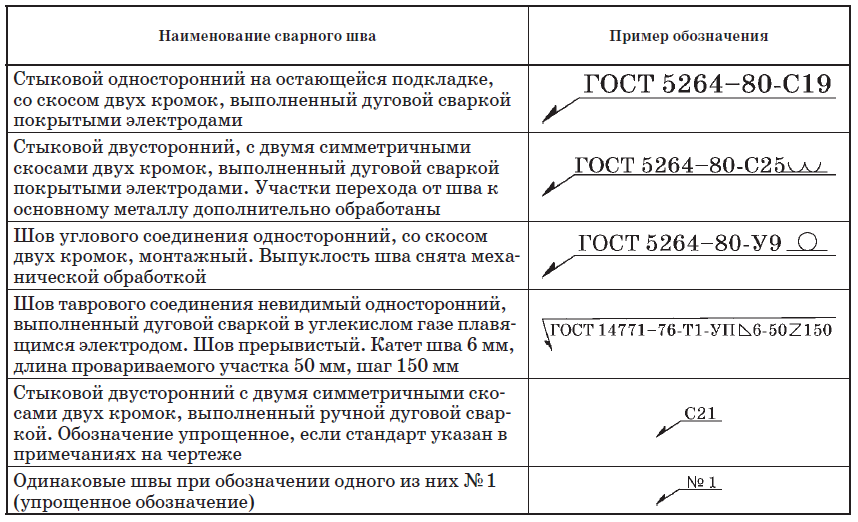
Конструктивные элементы сварных соединений.
Торцовые поверхности деталей, подлежащие нагреву и расплавлению при сварке, называют свариваемыми кромками. Для обеспечения проплавления кромок в зависимости от толщины основного металла и способа сварки им придают оптимальную форму, предварительно подготавливая кромки.
При сварке тонкостенных деталей применяют отбортовку кромок. Для толстостенных деталей осуществляют разделку кромок, подлежащих сварке, в виде их наклонного прямолинейного или криволинейного скоса.
На рисунке 8 приведены применяемые формы кромок для различных типов сварных соединений. Основными геометрическими параметрами кромок и соединений, подготовленных и собранных под сварку, являются угол скоса и угол разделки кромок, притупление кромок, зазор, высота отбортовки и радиус закруглений.
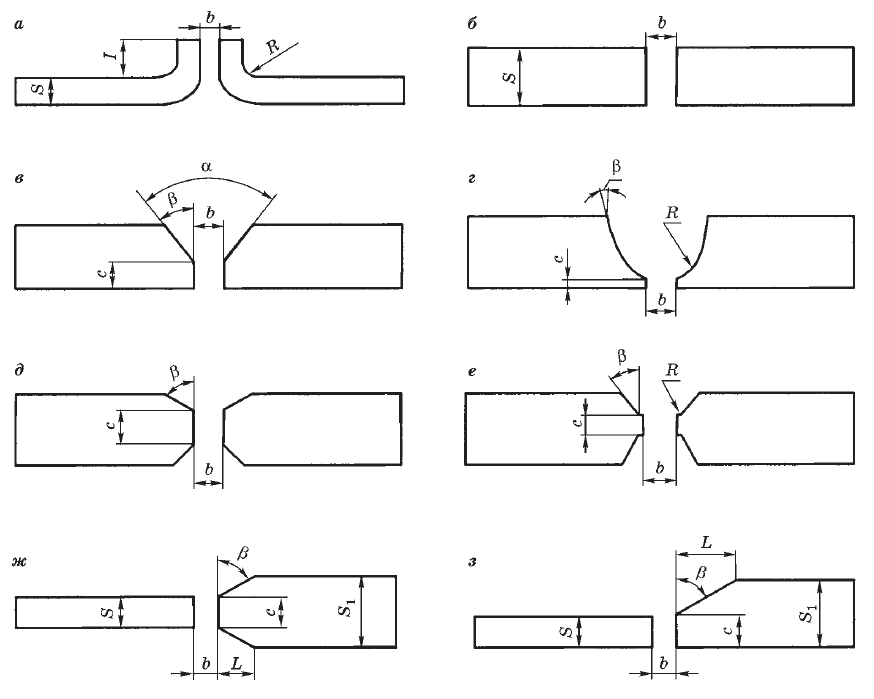
Углом скоса кромки называют острый угол в между плоскостью скоса кромки и плоскостью торца, угол а между скошенными кромками свариваемых частей — углом разделки.
Притуплением кромок называют длину с нескошенной части торца кромки, подлежащей сварке. При одностороннем и двустороннем скосе кромок острый край притупляют для правильного формирования шва и предотвращения образования прожогов.
Зазор — кратчайшее расстояние b между кромками собранных для сварки деталей. Зазор при сборке под сварку определяется толщиной и химическим составом свариваемых сплавов, способом сварки, конструкцией соединяемых деталей и типом соединения.
От типа и угла разделки кромок зависит количество необходимого электродного металла для заполнения разделки, а значит, и производительность сварки. Двусторонний скос кромок, по сравнению с односторонним, позволяет уменьшить объем наплавленного металла в 1,6-1,7 раза. Кроме того, такая разделка обеспечивает меньшую величину деформаций после сварки.